Controlled Low Strength Material ( CLSM)
Introduction
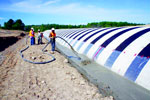 |
Controlled Low-Strength Material (CLSM) is a cementitious fill that is in a flowable state at the time of placement and has lower compressive strength to facilitate further excavation activity. CLSM is also known by several names- Flowcrete, Controlled Density Fill ( CDF), Flowable Mortar, Non-shrink Fill, etc. |
The material has gained appreciable recognition in the USA and Canada as a fill material because of its inherent advantages. These include flowing placement without segregation, self-consolidation, controlled density, controlled strength, ease of excavation, and economy. CLSM as defined by ACI 116R is a material that results in a compressive strength of 8.3 MPa (1200 psi) or less. Most current CLSM applications require unconfined compressive strengths of 2.1 MPa (300 psi) or less.
The upper limit of 8.3 MPa as stated above comes into picture in case of fills where re-excavation is not envisaged. Generally, CLSM mixtures are not designed to resist freezing and thawing, abrasive or erosive forces, or aggressive chemicals. For all practical purposes, CLSM is to be treated as a self-compacted backfill material that is used in place of compacted fill. CLSM is a fluid mixture made of Portland cement, water, and fine aggregate or fly ash or both. Sometimes it also contains an admixture. The consistency of CLSM is like that of a slurry or lean grout, yet several hours after placement the material hardens enough to support traffic loads without settling.
Applications
As stated earlier, the primary application of CLSM is as a structural fill or backfill in lieu of compacted soil. Because CLSM needs no compaction and can be designed to be fluid, it is ideal for use in tight or restricted-access areas where placing and compacting fill is difficult. If future excavation is anticipated, the maximum long-term compressive strength should generally not exceed 2.1 MPa (300 psi). The following applications are intended to present a range of uses for CLSM. . As CLSM is a highly fluid material, consideration must be given to the lateral pressure exerted during placement; lightweight pipes, etc may need to be anchored to prevent flotation.
- Trench Fill
- Structural Fill
- Insulating and Isolation fill
- Conduit Bedding
- Pavement Bases
- Erosion Control
- Void Filling
- Nuclear Facilities
- Bridge Reclamation
Trench Fill-CLSM can be readily placed into a trench, hole or other cavity. Compaction is not required; hence, the trench width or size of excavation can be reduced. Granular or site excavated backfill, even if compacted properly in the required layer thickness, cannot achieve the uniformity and density of CLSM. When backfilling against retaining walls, consideration should be given to the lateral pressures exerted on the wall by flowable CLSM. Where the lateral fluid pressure is a concern, CLSM can be placed in layers, allowing each layer to harden prior to placing the next layer.
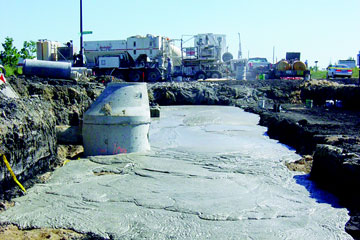 |
Structural Fills-Depending upon the strength requirements, CLSM can be used for foundation support. Compressive strengths can vary from 0.7 to 8.3 MPa (100 to 1200 psi) depending upon application. In the case of weak soils, it can distribute the structures load over a greater area. For uneven or non uniform sub-grades under foundation footings and slabs, CLSM can provide a uniform and level surface. Compressive strengths will vary depending upon project requirements.
Pavement Bases- The CLSM mixture can be directly poured onto the subgrade between the two curb confinements directly from a mixer. When used for pavements, it is necessary that we have a good drainage system in place including curb, gutter, storm sewers and proper pavement grades. Freezing and thawing damage could result in poor durability if the base material is frozen when saturated with water.
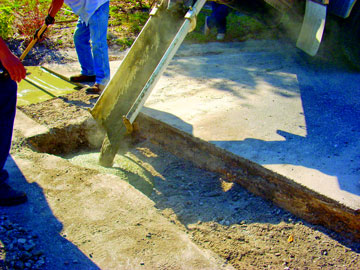 |
Conduit bedding- CLSM provides an excellent bedding material for pipe, electrical, telephone, and other types of conduits. The flowable characteristic of the material allows the CLSM to fill voids beneath the conduit and provide a uniform support. Encasing the entire conduit in CLSM also serves to protect the conduit from future damage. If the area around the conduit is being excavated at a later date, the obvious material change in CLSM versus the surrounding soil or conventional granular backfill would be recognized by the excavating crew, alerting them to the existence of the conduit. Coloring agents have also been used in mixtures to help identify the presence of CLSM.
CLSM Ingredients
Ingredients of CLSM are in no way much different from normal concrete. The mix components are Cement, water, fly ash or other similar products, and fine or coarse aggregates or both. Some mixtures consist of water, cement, and fly ash only. In some special and specific use, CLSM is produced using foaming agents to achieve low density, use of swelling clays such as bentonite to achieve low permeability and to achieve radiation shielding in applications at nuclear facilities, Magnetite or hematite fines are also added. Components of CLSM can be enumerated as;
- Cement – Portland cement
- Fly ash - Coal-combustion fly ash is sometimes used to improve flowability. Its use can also increase strength and reduce bleeding, shrinkage, and permeability. High fly ash-content mixtures result in lower-density CLSM when compared with mixtures with high aggregate contents. Fly ashes used in CLSM mixtures do not need to conform to either Class F or C as described in ASTM C 618.
- Admixture- Air-entraining admixtures and foaming agents can be valuable constituents for the manufacture of CLSM. The inclusion of air in CLSM can help provide improved workability, reduced shrinkage, little or no bleeding, minimal segregation, lower unit weights, and control of ultimate strength development. Higher air contents can also help enhance CLSM’s thermal insulation and freeze-thaw properties.
- Water- water that is compatible for normal concrete can be used for CLSM
- Aggregates- Aggregates are often the major constituent of a CLSM mixture. The type, grading, and shape of aggregates can affect the physical properties, such as flowability and compressive strength.
- Ponded Ash- Ponded ash, typically a mixture of fly ash and bottom ash slurried into a storage/disposal basin, can also be used in CLSM. The proportioning of the ponded ash in the resulting mixtures depends on its particle size distribution. Typically, it can be substituted for all of the fly ash and a portion of the fine aggregate and water. Unless dried prior to mixing, ponded ash requires special mixing because it is usually wet. Basin ash is similar to ponded ash except it is not slurried and can be disposed of in dry basins or stockpiles.
Hardening Time
Hardening time is the approximate period of time required for CLSM to go from the plastic state to a hardened state with sufficient strength to support the weight of a person. Normal factors affecting the hardening time are:
- Type and quantity of cementitious material
- Permeability and degree of saturation of surrounding soil that is in contact with CLSM
- Moisture content of CLSM
- Proportioning of CLSM
- Mixture and ambient temperature
- Humidity; and
- Depth of fill.
Segregation
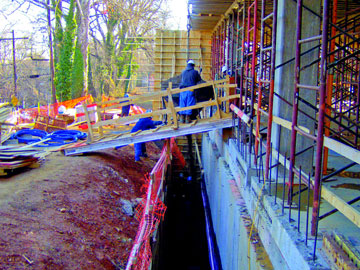 |
The constituents in the mixture can separate at high levels of flowability and this situation is similar to segregation experienced with some high-slump concrete mixtures. With proper mixture proportioning and materials, a high degree of flowability can be attained without segregation. For highly flowable CLSM without segregation, adequate fines are required to provide suitable cohesiveness. Fly ash generally accounts for these fines, although silty or other non-cohesive fines up to 20% of total aggregate have been used. The use of plastic fines, such as clay, should be avoided because they can produce deleterious results, such as increased shrinkage. In flowable mixtures, satisfactory performance of CLSM has been obtained with Class F fly ash contents as high as 415 kg/cum in combination with cement, sand, and water. Some CLSM mixtures have been designed without sand or gravel, using only fly ash as filler material. These mixtures require much higher water content, but produce no noticeable segregation.
Pumpability
For any pumpable concrete, voids must be adequately filled with solid particles to provide adequate cohesiveness for transport through the pump line under pressure without segregation. Inadequate void filling results in mixtures that can segregate in the pump and cause line blockage. Also, it is important to maintain a continuous flow through the pump line. Interrupted flow can cause segregation, which also could restrict flow and could result in line blockage. Presence of Fly ash can enhance the pumpability aspect by providing adequate void filling character to the CLSM.
Density
It is observed that the dry density of CLSM is much less than the wet density due to the loss of water from the mix. Wet density of normal CLSM in place is in the range of 1840 to 2320 kg/cum, which is greater than most compacted materials. A CLSM mixture with only fly ash, cement, and water has a density between 1440 to 1600 kg/cum. Ponded ash or basin ash CLSM mixture densities are typically in the range of 1360 to 1760 kg/cum. Dry density of CLSM can be expected to be substantially less than that of the wet density due to water loss.
Mixes
CLSM mixes should be designed for the particular flowing characteristics required as well as the compressive strength necessary. As indicated previously aggregates are chosen more for their compatibility with the CLSM’s flowing characteristics than their contribution to strength. A wide range of fine aggregates including sands, gravels and quarry waste material can be used to produce satisfactory CLSM mixes. It is not necessary for aggregate to comply with AS 2758.1–1985. Aggregates should, however, be free of reactive or expansive materials. Coarse aggregates are not normally included in CLSM.
Where fly ash is used to improve flowability it should be noted that early strengths will be reduced. A maximum 28-day strength of 0.5 MPa is suggested where future hand excavation is likely and 1.5–2 MPa for mechanical excavation. Slumps that will suit most applications of CLSM are around 200 mm. Suggested criteria for CLSM mixes are given in Table 1.
Mixing and Placing
CLSM is best batched and mixed using equipment normally used to mix concrete. It is generally placed direct from agitator trucks but can be placed using chutes, skips or pumps. Where the material is to be pumped, higher cementitious contents may be required. This in turn will result in increased strength which may be undesirable if backfill material is likely to be excavated at a later date.
Mixing and placing procedures- Usually CLSM is batched and mixed at a central mixing plant in accordance with ASTM C 94 procedures for concrete, then delivered to the jobsite by ready mix truck. For small jobs, however, a mobile mixer can be used. It delivers dry CLSM materials to the jobsite for onsite mixing with water right before placement.
To place CLSM, use a chute, conveyor, bucket, or pump depending on the type of void to be filled and its accessibility. Because CLSM flows and self-levels, it’s possible to discharge the material from one spot to fill restricted-access areas. When filling large, open trenches, moving the discharge point helps spread the material. To contain CLSM when filling open-ended structures such as tunnels, block the ends of the structure with sandbags or dirt dams.
For most applications, CLSM can be placed continuously. Sometimes, though, it’s necessary to place the material in lifts. When back filling in retaining walls, placing CLSM in lifts prevents lateral pressures from exceeding the loading capacities of the wall. Allow each lift to harden before placing the next lift. For pipe bedding, placing CLSM in lifts prevents floating the pipe. Sometimes sandbags or other weights are used to ballast the pipe until CLSM sets.
Standing water in a trench does not have to be pumped out before filling the trench with CLSM. CLSM will displace the water and force it out. Any loose debris or rubble in the trench can remain too. CLSM will encapsulate it. When placing CLSM in open trenches in cold weather, heat it using the same methods for heating ready mixed concrete to prevent the material from freezing before it hardens. The top layer may freeze but it can be scraped off later.
CLSM needs no compacting and little or no spreading or finishing. When using it as fill for pavement section replacement, smooth the fill surface with a square shovel if the surface is below pavement grade. If placing the fill up to pavement grade for use as a temporary driving surface, finish it with a wood float. Because of its high water content, CLSM will bleed. This bleed water is usually not a problem and can be allowed to run off or evaporate.
Advantages of CLSM
When used as a backfill material, unit cost of CLSM is more than most soil or granular backfill materials. Some of the advantages of CLSM are listed below.
- Easy Production—using locally available materials, ready mix suppliers can easily manufacture CLSM to meet most project specifications.
- Easy to deliver—Ready mix trucks can deliver specified quantities of CLSM to the jobsite whenever the material is needed.
- Easy to place—Depending on the type and location of void to be filled, CLSM can be placed by chute, conveyor, pump, or bucket. Because CLSM is self-leveling, it needs little or no spreading or compacting. This speeds construction and reduces labor requirements.
- Versatile—CLSM mix designs can be adjusted to meet specific fill requirements. Sometimes CLSM can also be used as a lightweight, insulating fill.
- Strong and durable—Load carrying capacities of CLSM typically are higher than those of compacted soil or granular fill. CLSM also is less permeable, thus more resistant to erosion. For use as a permanent structural fill, CLSM can be designed to achieve 28-day compressive strengths as high as 1200 psi.
- Can be excavated—CLSM having compressive strengths of 50 to 100 psi is easily excavated with conventional digging equipment yet is strong enough for most backfilling needs.
- Requires less inspection—during placement, soil backfill must be tested after each lift for sufficient compaction. CLSM self-compacts consistently and doesn’t need this extensive field testing.
- Allows fast return to traffic—because CLSM can be placed quickly and can support traffic loads within several hours, it minimizes downtime for pavement repairs.
- No Settlement—CLSM does not form voids during placement and won’t settle or rut under loading. This advantage is especially significant if the backfill is to be covered by a pavement patch. Soil or granular fill, if not consolidated properly, may settle after a pavement patch is placed and form cracks or dips into the road.
- Reduces excavating costs—CLSM allows narrower trenches because it eliminates having to widen trenches to accommodate compaction equipment.
- Improves worker safety—Workers can place CLSM in a trench without entering the trench, reducing their exposure to possible earth collapses.
- Allows all-weather construction—CLSM will displace any standing water left in a trench from rain or melting snow, reducing the need for dewatering pumps. To place CLSM in cold weather, heat the material using the same method for heating ready mixed concrete.
- Reduces equipment needs—unlike soil or granular backfill, CLSM can be placed without loaders, rollers, or tampers.
- Requires no storage—because ready mix trucks deliver CLSM to the jobsite in the quantities needed, storing fill material onsite is unnecessary. Also, there is no leftover fill to haul away.
- Makes use of a waste by-product—Fly ash is a by-product produced by power plants that burn coal to generate electricity. CLSM containing fly ash benefits the environment by making use of this industrial waste material.
Reference:
- Data Sheet on Cement Concrete and Aggregates Australia
- Paper on- Controlled low strength material by Anne Smith
- Controlled Low-Strength Materials-ACI 229R-99