Glazed Facade Systems
The choice of glass as an architectural material has grown steadily since its first application for windows. The emergence of glass for window application dates back to Roman period. As technology evolved, glass with its many impeccable properties gained popularity and became one of the most opted building materials. It forms an important component of a building skin.
Structural Glass Facades, commonly acronymed as SGF’s, integrate structure and cladding aspects and can be used in long span applications by providing increased transparency across the width and height. Increased demand for enhanced transparency has resulted in the development of improved tension-based façade systems by eliminating or minimising the bending and compressive components.
Glass as a material exhibit effectual resistance to water |
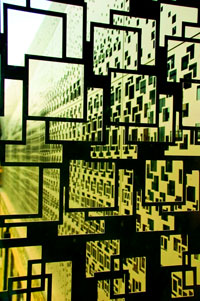 |
percolation, corrosion, salt water, carbonated water, strong acids, organic solvents, Ultra-violet radiation and hence has been widely accepted. Glass appearance is influenced by several factors, including tinting (colorants added to the glass batch), reflective and low - E coatings, and opacifiers (for spandrel glass).
The strength of a glass however depends on many factors, important are;
• Surface condition and edge quality
• Load duration
• Environmental condition, especially humidity
• Stress distribution on the surface
• Size of the stressed area
• Damage of glass surface – flaws and cracks
Architectural Glass
Architectural glass comes in three different strength categories.
Annealed Glass
Annealed glass is the most commonly used architectural glass. Because it is not heat-treated and therefore not subject to distortion typically produced during glass tempering, it has good surface flatness. On the downside, annealed glass breaks into sharp, dangerous shards.
Tempered Glass
Heat-strengthened and fully-tempered glass is heat-treated glass products, heated and quenched in such a way to create residual surface compression in the glass. The surface compression gives the glass generally higher resistance to breakage than annealed glass. Heat-strengthened glass has at least twice the strength and resistance to breakage from wind loads or thermal stresses as annealed glass. The necessary heat treatment generally results in some distortion compared to annealed glass. Like annealed glass, heat-strengthened glass can break into large shards. Fully-tempered glass provides at least four times the strength of annealed glass, which gives it superior resistance to glass breakage. Similar to heat-strengthened glass, the heat-treatment generally results in some distortion. If it breaks, fully-tempered glass breaks into many small fragments, which makes it suitable as safety glazing under certain conditions.
Laminated Glass
Laminated glass consists of two or more layers of glass adhered together with a plastic interlayer. Because it can prevent the fall-out of dangerous glass shards following fracture, it is often used as safety glazing and as overhead glazing in skylights. The plastic |
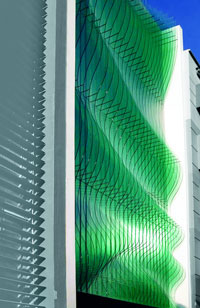
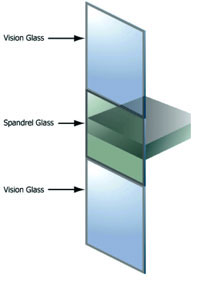
|
interlayer also provides protection from ultraviolet rays and attenuates vibration, which gives laminated glass good acoustical characteristics. Because laminated glass has good energy absorption characteristics, it is also a critical component of protective glazing, such as blast and bullet-resistant glazing assemblies.
Coated Glass
Coated glass is covered with reflective or low-emissivity (low-E) coatings. In addition to providing aesthetic appeal, the coatings improve the thermal performance of the glass by reflecting visible light and infrared radiation.
Tinted glass
Tinted glass contains minerals that color the glass uniformly through its thickness and promote absorption of visible light and infrared radiation.
Safety Glass
Fully-tempered or laminated glass is commonly used for safety glazing. Tempered glass limits the risk of injury by fracturing into small fragments. Laminated glass limits the risk of injury by retaining the fractured glass on the plastic interlayer and thereby limiting fall-out of glass fragments. Safety glazing must be identified with an indelible label on the glass indicating its conformance to federal safety standards published by the Consumer Products Safety Commission (CPSC). Wire glass typically does not meet CPSC requirements for safety glazing but is used for fire-rated glazing.
Insulating Glass (IG)
Insulating glass units consist of two or more layers of glass with a continuous spacer that encloses a sealed air space. The spacer typically contains a desiccant that dehydrates the sealed air space. The air space reduces heat gain and loss, as well as sound transmission, which gives the IG unit superior thermal performance and acoustical characteristics compared to single glazing. Most commercial windows, curtain walls, and skylights contain IG units. Most perimeter seals consist of a combination of non-curing (typically butyl) primary seal and cured (frequently silicone) secondary seal. The service life of an IG unit is typically determined by the quality of the hermetic sealants installed between the glass and the spacers, and the quality of the desiccant.
Spandrel Glass
Spandrel glass is the glass that conceals structural building components such as columns, floors, HVAC systems, electrical wiring, plumbing, etc. Spandrel glass is typically located between vision glasses on each floor of a building.
Curtain wall and structurally glazed designs often require the use of spandrel glass to achieve a designer’s vision of the finished project. Spandrel glass applications can be complementary or contrasting in colour when compared to the vision glass appearance. Spandrel glass must be heat-treated to avoid thermal stress breakage. Guardian has extensive experience with spandrel glass applications and can help architects and building owners achieve the desired appearance while reducing the risk of thermal stress breakage.
Spandrel glass can be monolithic, laminated, or insulating glass. The spandrel glass can be made opaque through the use of opacifiers (film/paint or ceramic frit) applied on an unexposed surface or through "shadow box" construction, i.e., providing an enclosed space behind clear spandrel glass. Shadow box |
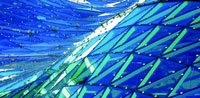
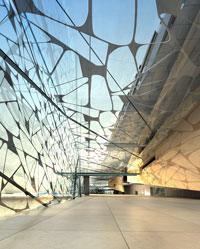
|
construction creates a perception of depth behind the spandrel glass that is sometimes desired.
Acoustics
Acoustic performance of exterior building envelope assemblies is expressed in terms of the Outdoor—Indoor Transmission Class (OITC) rating, which is a measure of the sound transmission loss during standard tests. High sound transmission loss, and therefore good sound insulation, is desirable in most applications. An integrated strategy to limit sound transmission through building walls requires review and testing of the entire wall system, since even small discontinuities in the wall assembly can negate the benefits of a well designed glazing system with a high OITC rating. In general, a higher fenestration OITC rating can be attained by incorporating laminated glass, and insulating glass assemblies (double or triple glazing) because the laminate damps vibration and the air space limits sound transmission. Additional mass in the form of thicker glass layer also helps sound absorption.
Structural Glass Glazing
Structural glass glazing is one of the most widely used and appreciated patterns of modern architectural designs and patterns. In this structural glass glazing, the building exteriors are made up and fitted with supreme quality glass sheets which not only makes it attractive, shining and reflecting but also provides them a quick to build facility and conventional way of completion of the building premises. These services of structural glass glazing works are provided by our company to its clients in each and every part of the country.
Curtain walling
Curtain wall is a term used to describe a building façade which does not carry any dead load from the building other than its own dead load. These loads are transferred to the main building structure through connections at floors or columns of the building. A curtain wall is designed to resist air and water infiltration, wind forces acting on the building, seismic forces (usually only those imposed by the inertia of the curtain wall), and its own dead load forces.
Curtain walls differ from storefront systems in that they are designed to span multiple floors, and take into consideration design requirements such as: thermal expansion and contraction; building sway and movement; water diversion; and thermal efficiency for cost-effective heating, cooling, and lighting in the |
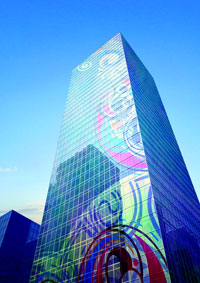 |
building.
A curtain wall is defined as thin, usually aluminum-framed wall, containing in-fills of glass, metal panels, or thin stone. The framing is attached to the building structure and does not carry the floor or roof loads of the building. The wind and gravity loads of the curtain wall are transferred to the building structure, typically at the floor line. Aluminum framed wall systems date back to the 1930's, and developed rapidly after World War II when the supply of aluminum became available for non-military use.
Curtain wall systems range from manufacturer's standard catalog systems to specialized custom walls. Custom walls become cost competitive with standard systems as the wall area increases. This section incorporates comments about standard and custom systems. It is recommended that consultants be hired with an expertise in custom curtain wall design for projects that incorporate these systems.
Curtain Wall Classification
Curtain walls can be classified by their method of fabrication and installation into the following general categories:
Stick Systems
Unitized Systems.
In the stick system, the curtain wall frame (mullions) and glass or opaque panels are installed and connected together piece by piece.
In the unitized system, the curtain wall is composed of large units that are assembled and glazed in the factory, shipped to the site and erected on the building. Vertical and horizontal mullions of the modules mate together with the adjoining modules. Modules are generally constructed one story tall and one module wide but may incorporate multiple modules. Typical units are five to six feet wide.
Both the unitized and stick-built systems are designed to be either interior or exterior glazed systems. In exterior glazed systems, glass and opaque panels are installed from the exterior of the curtain wall. Exterior glazed systems require swing stage or scaffolding access to the exterior of the curtain wall for repair or replacement. Some curtain wall systems can be glazed from either the interior or exterior. Typical opaque panels include opacified spandrel glass, metal panels, thin stone, and other materials, such as terra cotta or FRP (fiber-reinforced plastic). The curtain wall often comprises one part of a building's wall system. Careful integration with adjacent elements such as other wall claddings, roofs, and base of wall details is required for a successful installation.
Support of Curtain Walls
Curtain wall systems must transfer back to floor structure or intermediate framing both their own dead load plus any live loads, which consist primarily of positive and negative wind loads but might also include a snow load applied to large horizontal areas, seismic loads, maintenance loads and others. Unfortunately, the curtain wall will likely demonstrate movement caused by thermal changes and wind significantly different than movement of the building structure. Therefore the connections to anchor the |
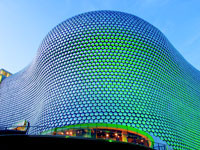 |
curtain wall must be designed to allow differential movement while resisting the loads applied.
Stick System
In stick-framed aluminium curtain wall, vertical mullions commonly run past two floors, with a combined gravity/lateral anchor at one floor and a lateral anchor only at the other. The splice between the vertical mullions will also be designed to allow vertical movement while providing lateral resistance. In large areas of stick framed curtain wall, a split vertical mullion will be introduced periodically to allow thermal movement. Note that this movement slightly distorts the anchors at the vertical mullions. Individual units of glass must accommodate the movement of the surrounding aluminum frame by sliding along glazing gaskets, distorting the gaskets or a combination of both. The movement of the glass within the frame and the movement forced in the anchors tend to induce additional stresses into a stick framed system.
Unitized curtain wall systems accommodate the differential movement between the structure and the thermal movement of the frame at the joints between each curtain wall unit. Because these units are frequently custom designed, the amount of movement to be accommodated can be carefully engineered into the system. Anchoring of unitized curtain wall typically consists of a proprietary assembly with three-way dimensional adjustability. The anchors occur at each pair of vertical mullions along the edge of slab or spandrel beam. Frequently, unitized systems span from a horizontal stack joint located at approximately desk height up to the anchor at the floor line above and then cantilevering past the floor to the next horizontal stack joint. The stack joint is designed to resist lateral loads while the two floor anchors resist gravity and lateral loads. One of the two floor anchors will allow movement in plane with the unitized system.
Unitized System
Unitized systems are typically custom designed. There is a wide range of systems on the market from manufacturers that provides varying levels of reliability. Unitized systems range in performance ability from industry standard to high performance walls. It is thus recommended that projects specifying unitized curtain wall systems incorporate a team member who has a breadth of experience in designing and working with unitized systems.
Unitized systems are typically pressure equalized rain screen systems. The units should be completely assembled in a factory and shipped to the site for installation on the building. The units are placed on the floors, bundled in crates, using the tower crane and lowered into place using a smaller crane or hoist owned by the glazing contractor. The mullion dimensions tend to be slightly larger than a stick system due to their open section as compared to the tube shape of a standard stick curtain wall section. The advantages of the unitized system derive from the more reliable seals achievable from factory construction and the reduced cost of labor in the factory versus that of high rise field labor. Units can be assembled in a factory while the structural frame of the building is being constructed. Where stick systems require multiple steps to erect and seal the wall, unitized walls arrive on the site completely assembled allowing the floors to be closed in more quickly. Unitized systems also require less space on site for layout thus providing an advantage for urban sites with space limitations.
Installation of a unitised curtain walling system (Image courtesy of Arup Facades)
Unitized systems generally rely on rain screen design principles and gaskets and/or the interlock of mating frames for moisture protection at joints between adjacent modules. The interlocking vertical mullions will typically have two interlocking legs. One leg will be in the plane just behind the glazing pocket and the other at the interior face of the mullions. The interlocking leg in the plane of the glazing pocket will be sealed by gaskets and is the primary line of defense against water and air infiltration. More robust systems will also include a gasket at the interior interlock. Systems whose connecting legs lock also compromise the ability of the system to accommodate movement. Some unitized designs are sensitive to small irregularities in the spacing of adjacent modules; for example, if the module joints are slightly out of tolerance, gaskets may not be properly compressed and moisture protection may suffer. Robust designs include multiple lines of defense, realistic tolerances and adjustability for erection of modules.
The four-way intersection refers to the location where four adjacent units meet. This is where field labor must seal between adjacent units to achieve a weather tight wall. The interlocking legs of the horizontal mullions are the most critical interface of a unitized system. Water that infiltrates the interlocking vertical mullions drains to the interlocking horizontals that must collect and divert this water to the exterior. The top horizontal mullion of a unit incorporates upstanding vertical legs that mate with cavities in the bottom horizontal of the unit above. These upstanding legs have gaskets that seal against the walls of the bottom horizontal. Some designs provide one upstanding leg that provides one line of defense against air and water infiltration. More robust systems will provide two upstanding legs with gaskets on both legs. A splice plate or silicone flashing that is installed at the top of the two adjacent units as they are erected on the building is typically required.
The vertical mullions of unitized systems typically anchor to the slab edge as they pass by. The stack joint is the horizontal joint where units from adjoining floors meet. Placing the stack joint at the sill of the vision glass (typically 30" above the floor) will minimize the dimension of the vertical mullions. This positioning utilizes the back span of the mullion above the anchoring point at the slab to counteract the deflection of the mullion below the slab.
Also placing the stack joint above the floor provides a more convenient location for field workers to achieve the critical seal at the four-way intersection. While two story spans are feasible, the weight of the unit is doubled which may require increased structural capacity to accommodate the increased load. Wind load bracing should be incorporated at the single span height to avoid increasing the vertical mullion dimension to accommodate the increased span. Steel can be added to a unitized system to increase its spanning capability. However, unlike a stick system which has an integral hollow shape, the split mullions must be allowed to move independently to accommodate the building movement thus complicating the introduction of steel. Large units may also increase transportation costs from the factory to the site and erection costs of placing the |
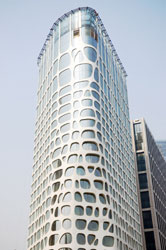 |
units on the building. Thermally broken unitized systems are available, utilizing similar technology as that used in stick curtain wall systems.
Modern Facade Systems
Dynamic Facade
Dynamic building envelopes include advanced window technologies, innovative fenestration systems and automated shading control, all of which characterize the new “intelligent” buildings generation (together with efficient HVAC control systems). Although a great idea, the design and implementation of such systems is a quite complex task. Driven by technological advances in transparent building facades and the general motivation for high quality green buildings, façade design alternatives have shifted to utilizing dynamic fenestration and shading systems for optimal control of daylight and solar gains.
Many design solutions rely on intelligent, dynamic façades to reach net zero energy goals. Dynamic or automated façade systems enable the reduction of lighting and HVAC end uses by leveraging the synergies of solar and daylight control on a real time basis. These systems can also deliver increased comfort, view, and amenity to occupants. Dynamic windows (switchable electrochromic windows, automated shades or blinds, operable windows) rely on sensors and control smarts to achieve high performance. Integrated façade solutions are networked with the HVAC and lighting control systems.
Solar Shading facades
Solar motion dynamic facades are almost like a living part of the building and respond to the elements (wind, rain, sun, snow) providing optimal comfort. Independent energy modelling on a 10-storey building in Dallas with Solar motion intelligent shading showed a 21.1% reduction in the annual cooling energy demand (MWhrs) was achieved, translating into savings of $137,160 per annum on the building modelled.From an architectural standpoint, one of the things we like best about solarmotion technology is the design options for shading systems. Typically you’d see these systems as aluminum airfoils mounted to the building envelope. Solar motion’s blade options, including Red Cedar wood, aluminum airfoils, laminated glass, a variety of perforated aluminum blades, clear acrylic, and even LED options mean your shading system could take the same form as your building, or stand out as a prominent feature. As buildings all over the world |
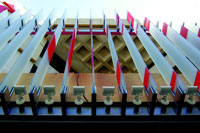
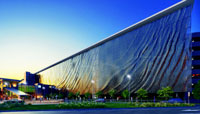
|
are responsible for a majority of the greenhouse gases emitted today, one of the easiest ways to reduce a building’s energy usage post-construction is to take these adaptive and dynamic factors into consideration during pre-design.
Media Facades
Image: The tessellated pattern of plastic bodies that make up the facade of the ILUMA building in Singapore are superimposed by fluorescent lamps, producing a large display screen that resembles Las Vegas in the 1970′s.
Media Facade is often associated with over-dimensional screens and animated, illuminated advertising. The facade in addition to its proposed function, acts as a huge advertising interface. Architectural façades are becoming the focus of new media communication. Large scale imaging video using LED media solutions accentuate the appearance and functionality of contemporary architectural sites in any urban landscape, by daytime and night.
Microalgae Façade
The tiny green algae will play a huge role in determining the future potential of this technology, which aims to provide shade and a renewable fuel source for the experimental apartment.
The microalgae used in the facades are cultivated in flat panel glass bioreactors measuring 2,5m x 0,7m. In total, 129 bioreactors have been installed on the south west and south east faces of the four-storey residential building. The heart of the system is the fully automated energy management centre where solar thermal heat and algae are harvested in a closed loop to be stored and then fermented to generate hot water.
The BIQ house was built as part of this year’s International Building Exhibition (IBA) in Hamburg. With 200m² of integrated photo-bioreactors, this innovative passive-energy house generates microalgae biomass and heat as renewable energy resources. At the same time, the system integrates additional functionalities such as dynamic shading, thermal insulation and noise abatement, highlighting the full potential of this technology.
Known as "SolarLeaf", this innovative façade system is the result of three years of research and development by Colt International based on a bio-reactor concept developed by SSC Ltd and design work led by the international design consultant and engineering firm, Arup. Funding support came from the German Government’s “ZukunftBau” research initiative.
“We’ve done the research. We’ve got the units in place. Now as we add the microalgae we will see for the first time how the bioreactor façade operates in a real life situation. It is a test for the technology, but it also represents a huge step forward. If we can demonstrate that microalgae biofaçades can become a viable new source of sustainable energy production, we can transform the urban environment, as well as providing architects with a new source of inspiration.” —Jan Wurm, Arup’s Europe Research Leader.
Double facade system
Double façade systems comprise an internal glazed façade which provides the thermal and air tightness functions and an external glazed facade separated by a zone that provides a thermal buffer and also incorporates devices such as solar shading. These systems are often used where the double facade extends outside the building line at the lower levels and often provides a canopy at street level. The space between the double facades can also be accessed for maintenance. The benefit of double facades is mainly on south facing walls where solar gain is highest. The space between the double facades can be ventilated in hot conditions or can be enclosed in colder conditions.
Facade Engineering
Facade Engineering is a new field with abundant opportunities. With emerging trends and innovations in façade systems, new generation materials, choosing the right kind of façade system becomes extremely complicated. Façade Engineers or Façade consultants provide services in selecting a suitable system focusing on the following parameters.
Performance led design.
Risk control.
Economics.
Concept to completion.
Quality inspection.
Verifying performance.
Cladding performance.
Troubleshooting.
References
1. Ventilated Facades- www.academia.edu
2. Facades and Interfaces- www.steelconstruction.info
3. Low energy facades- www.lowenergyfacades.lbl.gov
4. Microalgae facade- www.arup.com
5. Modern Facades- www.toxel.com , www.archdaily.com , www.archrecord.construction.com
6. WBDG-National Institute of Building Sciences.