Admixtures for Concrete
(Excerpts from ACI Bulletin E4-12)
Admixture can be defined as a material other than water, aggregates, cementitious materials, and fiber reinforcement, used as an ingredient of a cementitious mixture to modify its freshly mixed, setting, or hardened properties and that is added to the batch before or during its mixing. Admixtures interact with the hydrating cementitious system by physical and chemical actions, modifying one or more of the properties of concrete in the fresh or hardened states. According to ACI 212.3R-10, "Report on Chemical Admixtures for Concrete," an admixture or combination of admixtures may be the only feasible way to achieve the desired performance from a concrete mixture in some cases. There are many kinds of chemical admixtures that can function in a variety of ways to modify the chemical and physical properties of concrete. This bulletin provides information on the types of chemical admixtures and how they affect the properties of concrete, mortar, and grout.
General Definitions
- Aggregate-Reactive - Aggregate containing substances capable of reacting chemically with the products of solution or hydration of the Portland cement in concrete or mortar under ordinary conditions of exposure, resulting in some cases in harmful expansion, cracking, or staining.
- Air-Entrained - Microscopic air bubbles intentionally incorporated in a cementitious paste during mixing, usually by use of a surface-active agent; typically between 0.0004 and 0.04 in. (10 and 1000 mm) in diameter and spherical or nearly so.
- Air-Entrapped - Air voids in concrete that are not purposely entrained and that are larger, mainly irregular in shape, and less useful than those of entrained air; and 1 mm or larger in size.
- Air content - the volume of air voids in cement paste, mortar, or concrete, exclusive of pore space in aggregate particles, usually expressed as a percentage of total volume of the paste, mortar, or concrete.
- Alkali - Salts of alkali metals, principally sodium and potassium; specifically sodium and potassium occurring in constituents of concrete and mortar, usually expressed in chemical analysis as the oxides Na2O and K2O.
- Alkali-aggregate reaction - Chemical reaction in either mortar or concrete between alkalis (sodium and potassium) from Portland cement or other sources and certain constituents of some aggregates; under certain conditions, deleterious expansion of concrete or mortar may result.
- Alkali-silica reaction - A generally deleterious dissolution and swelling of siliceous aggregates in the presence of pore solutions comprised of alkali hydroxides; the reaction products may cause abnormal expansion and cracking of concrete.
- Calcium chloride - A crystalline solid, CaCl2; in various technical grades, used as a drying agent, as an accelerator for fresh concrete, a deicing chemical, and for other purposes.
- Cement, Portland - A hydraulic cement produced by pulverizing clinker formed by heating a mixture, usually of limestone and clay, to 1400 to 1600°C (2550 to 2900°F). Calcium sulphate is usually ground with the clinker to control set.
- Cementitious - having cementing properties.
- Sulphate attack - either a chemical or physical reaction or both between sulphates usually in soil or groundwater and concrete or mortar; the chemical reaction is primarily with calcium Aluminate hydrates in the cement-paste matrix, often causing deterioration.
- Sulphate resistance - Ability of concrete or mortar to withstand sulphate attack.
An Overview
Chemical admixtures are available in liquid and Powder form. Liquid admixtures are dispensed through mechanical dispensers as the concrete is batched, but can be introduced to the concrete by other means, such as hand dosing or truck mounted dispensers. Powders are usually introduced in pre-packaged units that contain a prescribed amount. Most times the units consist of bags that can be opened and the contents added while mixing, or bags that are made to disintegrate and disperse their contents while mixing. Generally, admixtures in powdered form are introduced to the concrete after batching.
Classification
Admixtures are classified based on the function they perform:
- Increase workability without increasing water content.
- Decrease the water content at the same workability;
- Retard or accelerate initial time of setting;
- Reduce or prevent shrinkage or create slight expansion;
- Modify the rate or capacity for bleeding;
- Reduce segregation;
- Improve pumpability;
- Reduce rate of slump loss;
- Retard or reduce heat evolution during early hardening;
- Accelerate the rate of strength development at early ages;
- Increase strength (compressive, tensile, or flexural);
- Increase durability or resistance to severe conditions of exposure, including application of deicing salts and other chemicals;
- Decrease permeability of concrete;
- Control expansion caused by the reaction of alkalis with reactive aggregate constituents;
- Increase bond of concrete to steel reinforcement;
- Increase bond between existing and new concrete;
- Improve impact and abrasion resistance;
- Inhibit corrosion of embedded metal;
- Produce colored concrete or mortar; and
- Aid in achieving sustainability requirements.
Effectiveness and Compatibility
|
The effectiveness of any admixture will vary depending on its concentration in the concrete and the effect of the various other constituents of the concrete mixture. Each class of admixture is defined by its primary function. It may have one or more secondary functions, however, and its use may affect, positively or negatively, concrete properties other than those desired. Therefore, adequate testing should be performed to determine the effects of an admixture on the plastic properties of concrete such as slump, rate of slump loss (that is the relationship between slump and time), air content, and setting time. In addition, testing should be performed to determine the effect of the admixture on the hardened properties of concrete that may be of interest, for example, strength development, drying shrinkage, modulus of elasticity, or permeability. The final decision as to the use of any admixture and the brand, class, or type, depends on its ability to meet or enhance specific concrete performance needs.
Many improvements can be achieved by proper selection and application of specific admixtures. The selection process should focus on the functional qualities required by structural demands, architectural requirements, and contractor needs. Whatever the approach, be it a single water-reducing admixture or a combination approach, the use of admixtures can be beneficial. Admixtures provide additional means of controlling the quality of concrete by modifying some of its properties, however, they cannot correct for poor-quality materials, improper proportioning of the concrete, and inappropriate placement procedures.
Multiple Admixtures
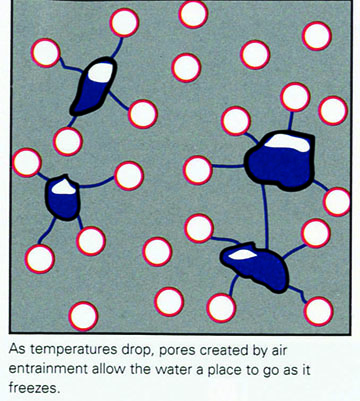 |
It is quite common for a concrete mixture to contain more than one admixture. In the simplest cases, such as paving or residential applications, a concrete mixture may be dosed with only a water-reducing admixture and an air-entraining admixture. High-performance concrete mixtures may be dosed with as many as five admixtures, depending on the specific application. Therefore, it is imperative that the admixtures that are used in a given concrete mixture are compatible to prevent undesired effects such as rapid slump loss, air-entrainment difficulties, severe set retardation, or improper strength development. A typical rule of thumb is for all admixtures to be added separately to a concrete mixture and not pre-blended before introduction into the mixture. In addition, admixture manufacturers typically provide information on potential incompatibility with other admixture chemistries on product data sheets. However, it should be noted that incompatibility issues in concrete mixtures are typically due to undesired chemical interactions, physical interactions, or both between chemical admixtures and other mixture ingredients, in particular, the cementitious materials system.
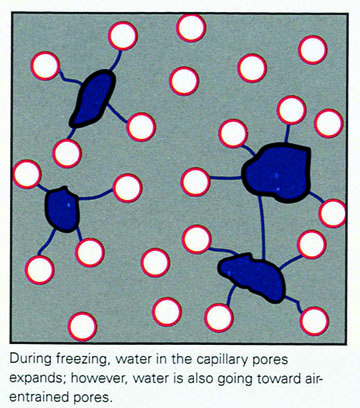 |
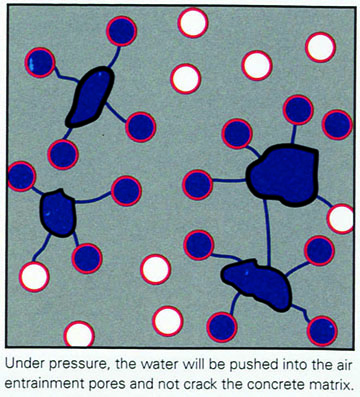 |
Air-Entraining Admixtures
One of the most significant innovations in concrete technology was made during the 1930s. It was noted that certain concrete pavements were more able to withstand the detrimental effects of freezing and thawing cycles than others. These cycles, and the damage caused, were a major inhibitor to durability of concrete pavements and other exterior applications. Investigation showed that the more durable pavements were slightly less dense, and that the cement used had been obtained from mills using beef tallow as a grinding aid in the manufacturing of cement. The beef tallow acted as an air-entraining agent, which improved the durability of the pavements. Later, after rigorous investigation, air-entrained concrete was specified in climates where freezing-and thawing resistance was needed.
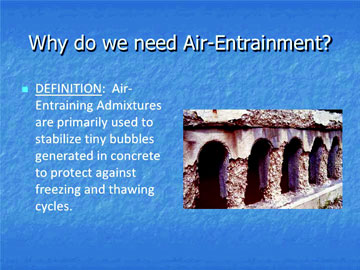 |
Air-entraining admixtures (AEA) are primarily used to stabilize tiny air bubbles in concrete that protect against damage from repeated freezing-and-thawing cycles. Until the mid-1990s, the most commonly used air-entraining admixture for concrete was a neutralized wood resin. Newer formulations may instead be formulated from synthetic detergents such as the salts of organic acids and sulfonated hydrocarbons. These modern formulations offer enhanced performance such as improved stability compared to early formulations. Today, most State Department of Transportation (DOT) specifications have limits that require the use of an air-entraining admixture in pavements.
Principal Mechanism
The space occupied by the mixing water in fresh concrete rarely becomes completely filled with cementitious hydration products after the concrete has hardened. The remaining spaces are capillary pores. Under saturated conditions, these cavities are filled with water. If this water freezes, the resulting expansion of water to ice (approximately 9%) creates internal pressure in a confined space. This stress exceeds the tensile strength of concrete. The result in non air-entrained concrete is cracking, scaling, and spalling.
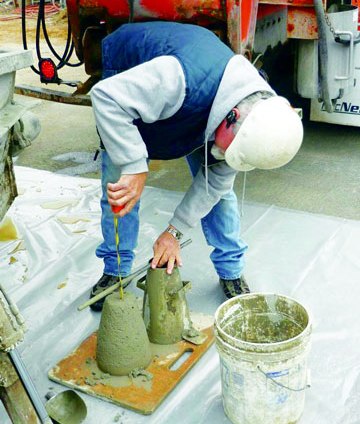 |
Entrained air voids make the capillaries discontinuous. As a result of the mixing action, air-entraining admixtures stabilize air bubbles in the cement paste that become a component of the hardened concrete. The resultant air-void system consists of uniformly dispersed spherical voids, usually between 10 and 1000 mm in diameter. Because the air voids are generally larger than the capillaries, they form tiny reservoirs that act as safety valves during ice expansion, accommodating the increased volume and preventing the build-up of internal pressure. Air entrainment in concrete is expressed as a percent of the overall concrete volume.
Entrained air should not be confused with entrapped air. Entrapped air is due to normal mixing and results in large, non-uniform air bubbles that do not have the correct size and spacing required to prevent damage in concrete caused by freezing water. Proper air entrainment or air void structures require the use of an admixture, either added to the plastic concrete or blended with the cement during manufacturing.
Use of air-entraining admixtures
Air-entraining admixtures should be required to conform to ASTM C260, "Standard Specification for Air-Entraining Admixtures for Concrete." Dosage rates of air-entraining admixtures generally range from 15 to 130 mL per 100 kg (1/4 to 2 fl oz per 100 lb) of cementitious material. Higher dosages are sometimes required depending on the materials and mixture proportions. For example, concrete containing fly ash or other pozzolans often requires higher doses of air-entraining admixture to achieve the same air content compared to a similar concrete using only Portland cement. Trial mixtures should be performed to ensure compatibility between air-entraining admixtures and other concrete components, including other chemical admixtures.
Water-Reducing and Setting Time
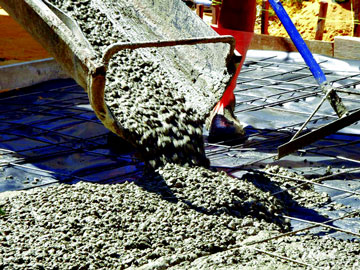 |
In general, these chemicals act as dispersants for Portland cement particles. By separating and spreading out the cement particles, internal friction is reduced, and slump and workability of the concrete is increased. Alternatively, the same workability can be achieved using less water, which lowers the water cementitious material ratio (w/cm) for given cement content. Lowering w/cm is a key method for improving durability. These admixtures also provide the ability to control the time of setting to meet changing jobsite and climatic conditions. The strength improvement resulting from water-reducing admixtures is primarily a result of reducing the w/cm and increasing cement efficiency. For a given air content, concrete strength is inversely proportional to the w/cm and, therefore, the reduction in water needed to achieve the desired slump and workability when a water-reducing agent is used will result in an increase in strength. The increase in strength using a water-reducing admixture often exceeds the strength from simply reducing the water content. This is due to the admixture's dispersing effect on cement that results in increased hydration efficiency.
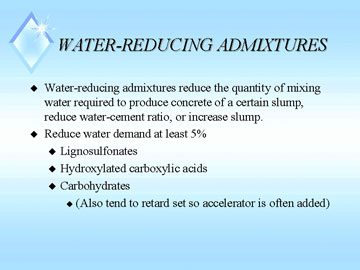 |
Water-reducing admixtures are based on a variety of materials; the most common of which are:
- Lignosulfonic acids and their salts;
- Hydroxylated polymers;
- Hydroxylated carboxylic acids and their salts;
- Sulfonated melamine or naphthalene formaldehyde condensates; and
- Polyether-polycarboxylates.
Each material can have different properties when used as an admixture. In particular, the amount of water reduction and the degree of set retardation can vary considerably. Some materials will entrain air, and other may affect bleeding and finishing properties. A commercial formulation may include accelerating agents or defoamers to counteract these side effects. As a result, it can be difficult to predict an admixture's performance based on its primary ingredient, even if this information is made available. ASTM C494 "Standard Specification for Chemical Admixtures for Concrete," classifies admixtures into categories based on performance:
• Type A Water-reducing admixtures;
• Type B Retarding admixtures;
• Type C Accelerating admixtures;
• Type D Water-reducing and retarding admixture;
• Type E Water-reducing and accelerating admixtures;
• Type F Water-reducing, high-range, admixtures;
• Type G Water-reducing, high-range, and retarding admixtures; and
• Type S Specific performance admixtures.
Admixtures types A through F covered by ASTM C494 are designed to serve a specific purpose. ASTM C494 outlines the performance requirements for an admixture to qualify for each category. Depending on the category, required properties may include the degree of water reduction, minimum or maximum variations in setting time, compressive strength, and the length change of hardened specimens. Some admixtures will meet the requirements of several categories, such as Type A and Type D. In such cases, the admixture will meet Type A requirements at low doses, and will meet Type D requirements at higher doses due to additional set retardation caused by higher dosages of those particular admixtures.
The Type S category can apply to any specialty admixture that does not fit into the other more common categories. The Type S category does not attempt to address the primary purpose of specialty admixtures, but instead provides guidelines for their effects on properties such as setting time and compressive strength to help users avoid unexpected variations in performance. Upon request, a manufacturer is required to provide data to substantiate the specific benefits of the Type S admixture.
ASTM C494 does not cover all possible concrete requirements, and additional properties will need to be tested depending on the application. Proper use of admixtures should begin by gathering available information and comparing the different types and brands that are available. Consideration must be given to information such as uniformity, dispensing, long-term performance, and available service. These are points that cannot be assessed by concrete tests but could determine successful admixture use.
The admixture manufacturer should be able to provide information covering typical dosage rates, times of setting, and strength gain for local materials and conditions. The evaluation of admixtures should be made with specific job materials (including other chemical admixtures under consideration) under anticipated ambient conditions. Laboratory tests conducted on concrete with water-reducing admixtures should indicate the effect on pertinent properties for the construction project, including: water requirement, air content, slump, rate of slump loss, bleeding, time of setting, compressive strength, flexural strength, and resistance to cycles of freezing and thawing. Following the laboratory tests, field test should be conducted to determine how the admixtures will perform in actual field conditions, considering all relevant factors such as placement equipment, weather and delivery distances.
Type-A; Water-Reducing Admixtures
Dosage rates of water-reducing admixtures depend on the type and amount of active ingredients in the admixture. The dosage is based on the cementitious materials content of the concrete mixture and is expressed as milliliters per hundred kilograms (fluid ounces per hundred pounds) of cementitious materials. Typically, the dosage rates of Type A water-reducing admixtures range from 130 to 390 mL per 100 kg (2 to 6 fl oz per 100 lb) of cementitious materials. Higher dosages may result in excessive retardation of the concrete setting time. Manufacturers recommended dosage rates should be followed and trial batches with local materials should be performed to determine the dosage rate for a given concrete mixture. In some occasions, dosages higher or lower than the manufacturer's recommendations may be used, but testing is necessary to ensure the resulting concrete meets the requirements of the project.
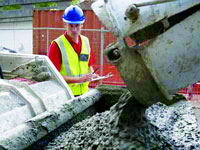 |
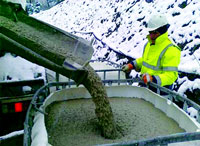 |
The primary ingredients of water-reducing admixtures are organic, which tend to retard the time of setting of the concrete. This retardation may be offset by small additions of chloride or non chloride accelerating admixtures at the batch plant. Typically, Type A admixtures already contain some accelerating admixtures that offset this natural retardation. Care should be taken to ensure that addition of chloride does not exceed the ACI 318 limits for maximum chloride-ion content in reinforced or prestressed concrete.
Type B, Retarding, And Type D, Water Reducing and Retarding Admixtures
Conventional retarding admixtures - two types of admixtures are used for the same basic purpose: to offset unwanted effects of high temperature, such as acceleration of set and reduction of 28-day compressive strength, and to keep concrete workable during the entire placing and consolidation period.
The benefits derived from retarding formulations include the following:
- Permits greater flexibility in extending the time of set and the prevention of cold joints;
- Facilitates finishing in hot weather; and
- Permits full form deflection before initial set of concrete.
As with Type A admixtures, their dosage rates are based on the amount of cementitious materials in the concrete mixture. While both Type B and Type D may provide some water-reduction, Type D is more effective in achieving this goal. The amount of retardation depends upon many factors including: admixture concentration, dosage rate, concrete proportions, and ambient and concrete temperatures.
The setting and strength development characteristics of concrete are not adversely affected by the use of stabilized wash water.
Different sources and types of cement or different lots of cements from the same source may require different amounts of the admixture to obtain the desired results because of variations in chemical composition, fineness, or both. The time at which the retarding admixture is introduced into the concrete may affect the results. Allowing the cement to become totally wet and delaying admixture addition until all other materials are batched and mixed may result in increased retardation and greater slump increase.
Increased retardation may also be obtained with a higher dosage of the retarding admixture. When high dosages of retarding admixture are used, however, rapid stiffening can occur with some sources of cement, resulting in severe slump loss and difficulties in concrete placement, consolidation, and finishing.
Extended-set admixtures - Advances in admixture technology have resulted in the development of highly potent retarding admixtures called extended-set admixtures or hydration-controlling admixtures. These admixtures are capable of stopping the hydration of cementitious systems, thereby providing a means to control the hydration and setting characteristics of concrete.
Extended-set admixtures are used in three primary applications: stabilization of concrete wash water, stabilization of returned plastic concrete, and stabilization of freshly batched concrete for long hauls. The use of extended-set admixtures in stabilization of concrete wash water eliminates the dumping of water that is used to wash out a ready-mixed concrete truck drum while keeping the fins and inner drum clean. The process is relatively simple and involves the addition of low dosages of the extended-set admixture to the wash water to control the hydration of concrete stuck to the fins and inside the drum. The stabilized wash water may be included in the mixing water for fresh concrete that is batched the next day or after a weekend. The setting and strength development characteristics of concrete are not adversely affected by the use of stabilized wash water.
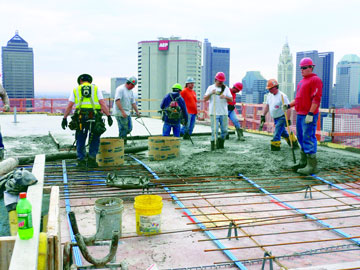 |
Although calcium chloride is the most effective and economical accelerator for concrete, it's potential to cause corrosion of reinforcing steel limits its use.
The use of extended-set admixtures to stabilize returned unhardened concrete has made it possible to reuse such concrete during the same production day or the next day in lieu of disposal. The dosage of extended-set admixture required depends on several factors that include the ambient and concrete temperatures, the ingredients used in the manufacture of the concrete, and the age of the concrete. Stabilized concrete is reused by batching fresh concrete on top of the stabilized concrete. In overnight applications, an accelerating admixture may be used to reinitiate the hydration process before adding fresh concrete. Increasingly, extended-set admixtures are being used for long hauls and to maintain slump and concrete temperature during transit, especially in warm weather. For this application, the extended-set admixture is added during or immediately after batching, and the required dosage is established based on the amount of retardation desired.
Type C, Accelerating, and Type E, Water Reducing and Accelerating Admixtures
Accelerating admixtures are added to concrete to decrease both the initial and final time of set and accelerate the early strength development. The earlier setting time and increased early strength gain of concrete brought about by an accelerating admixture will result in a number of benefits, including reduced bleeding, earlier finishing, improved protection against early exposure to freezing and thawing, earlier use of structure, and reduction of protection time to achieve a given quality. Accelerating admixtures do not normally act as anti-freeze agents; therefore, protection of the concrete at early ages is required when freezing temperatures are expected.
Although calcium chloride is the most effective and economical accelerator for concrete, it's potential to cause corrosion of reinforcing steel limits its use. ACI Committee 318 limits the water-soluble chloride-ion content based on the intended use of the concrete and many government agencies prohibit its use.
The following guidelines should be considered before using calcium chloride or chloride-bearing admixture:
- It should not be used in prestressed concrete because of its potential for causing corrosion;
- The presence of chloride ion has been associated with corrosion of galvanized steel such as when this material is used as permanent forms for roof decks;
- Where sulfate-resisting concrete is required, calcium chloride should not be used;
- Calcium chloride should be avoided in reinforced concrete in a moist condition. In non-reinforced concrete, the level of calcium chloride used should not exceed 2% by weight of cementitious material;
- Calcium chloride should be dissolved in a portion of mixing water before batching because un dissolved lumps may later disfigure concrete surfaces;
- Calcium chloride precipitates most air-entraining agents so it must be dispensed separately into the mixture; and
- Field experience and laboratory tests have demonstrated that the use of uncoated aluminum conduit in reinforced concrete containing 1% or more of calcium chloride may lead to sufficient corrosion of the aluminum to collapse the conduit or crack the concrete.
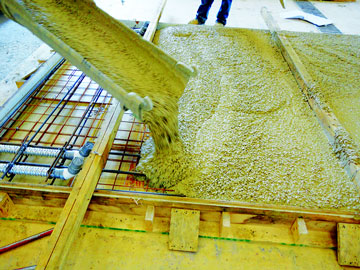 |
Non-chloride accelerating admixtures are available that provide the benefits of an accelerating admixture without the increased risk of corrosion from chloride. Formulations based on salts of formates, nitrates, nitrites, and thiocyanates are available from admixture manufacturers. These nonchloride accelerators are effective for set acceleration and strength development: however, the degree of effectiveness of some of these admixtures is dependent on the ambient temperature and concrete temperature at the time of placement.
Admixtures for Self-Consolidating Concrete
Self-consolidating concrete (SCC) describes a specialized, high-slump concrete mixture able to flow and consolidate under its own weight with little or no vibration and without segregation or excessive bleeding. SCC is useful for placing concrete through heavily congested reinforcement and for building structures that require very smooth formed surfaces. The properties of SCC are made possible through a combination of admixture selection and an increase in the fines content compared to normal slump concrete. SCC mixtures usually contain a polyether-polycarboxylate HRWR admixture to provide the required slump and flow. Higher levels of fines are used to increase cohesiveness and prevent segregation and bleeding in the highly plasticized concrete, although alternatively a viscosity modifying admixture (VMA) can be used to increase stability (see Section 5.4). SCC may contain other categories of admixtures, depending on the application.
Admixtures for Slump and Workability Retention
Admixtures that provide slump and workability retention without affecting the initial time of set of concrete or early-age strength development, as is the case with retarding admixtures are available in the industry. On their own, these workability-retaining admixtures have minimal effect on water reduction and can be used in combination with normal, mid-range, or high-range, water-reducing admixtures to provide desired levels of workability retention in concrete mixtures, in particular, high-slump concretes or SCC mixtures. Workability-retaining admixtures should meet the Type S requirements in ASTM C 494.
Corrosion-Inhibiting Admixtures
Reinforcing steel corrosion is a major concern with regard to the durability of reinforced concrete structures. Each year, numerous bridges, parking garages, and other concrete structures undergo extensive repair and rehabilitation to restore their structural integrity as a result of corrosion
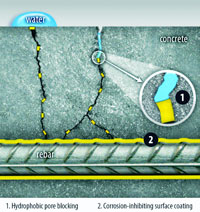 |
damage.
The high alkalinity of new concrete protects reinforcement from corrosion due to the formation of a corrosion resistant passive layer at the surface of the steel. However, this passive layer can be destabilized in concrete contaminated by chlorides, which allows corrosion to begin if there is sufficient moisture and oxygen present at the surface of the steel. Chlorides can be introduced into concrete from deicing salts that are used in winter months to melt snow or ice, from seawater, or from the concrete mixture ingredients.
|
There are several ways of combating chloride-induced corrosion, one of which is the use of corrosion-inhibiting admixtures. These admixtures are added to concrete during batching and they protect embedded reinforcement by delaying the onset of corrosion and also by reducing the rate of corrosion after initiation. There are several commercially available inhibitors on the market. Active ingredients include inorganic materials such as calcium nitrite, and organic materials such as amines and esters. Calcium nitrite resists corrosion by stabilizing the passive layer in the presence of chloride ions. However, the dose of calcium nitrite must be sufficient for the level of chloride contamination. Organic inhibitors function by forming a protective film at the surface of the steel to help resist moisture and chemical attack. As with all admixtures, the manufacturer's recommendations should be followed with regard to dosage.
Although corrosion inhibiting admixtures can help resist corrosion, these admixtures are intended to compliment, rather than replace, proper mixture proportioning and good concrete practices. For example, corrosion resistance can also be increased by reducing the permeability of the concrete through the use of low w/cm (possibly with the aid of a HRWR admixture,) or with a permeability reducing admixture. Some available corrosion inhibitors will accelerate the time of set in concrete and therefore retarding admixtures may be necessary to improve working time. Adjustments to batch water are usually necessary, depending |
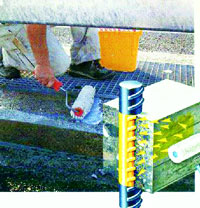 |
on the dosage, to ensure that maximum water content for the mixture is not exceeded.
Manufacturer's recommendations should be followed with regard to dosage & suitability of shrinkage-reducing admixtures for use in freezing-and thawing environments.
Shrinkage-Reducing Admixtures
The loss of moisture from concrete as it dries results in a volume contraction called drying shrinkage. Drying shrinkage tends to be undesirable when it leads to cracking due to either internal or external restraint, curling of floor slabs, and excessive loss of prestress in prestressed concrete applications. The magnitude of drying shrinkage can be reduced by minimizing the unit water content of a concrete mixture, using good-quality aggregates, and using the largest coarse aggregate size and content consistent with the particular application. In addition, admixtures have been introduced to help further reduce drying shrinkage. These are based on organic materials such as propylene glycol or related compounds that reduce the surface tension of water in the capillary pores of concrete, thereby reducing the tension forces within the concrete matrix that lead to drying shrinkage. This mode of action should not be confused with shrinkage-compensating materials such as expansive, or Type K, cements. Manufacturer's recommendations should be followed with regard to dosage and suitability of shrinkage-reducing admixtures for use in freezing-and thawing environments.
Admixtures for Underwater Concrete
Increasingly, concrete structures are being designed with permeabilityreducing admixtures (PRAs) to resist water penetration, in which the protection becomes an integral part of the concrete itself rather than just a surface barrier.
Placing concrete underwater can be particularly challenging because of the potential for washout of the cement and fines from the mixture, which can reduce the strength and integrity of the in-place concrete. Although placement techniques, such as tremies, have been used successfully to place concrete underwater, there are situations where enhanced cohesiveness of the concrete mixture is required, necessitating the use of an anti washout or viscosity modifying admixture (VMA). Some of these admixtures are formulated from either cellulose ether or whelan gum, and they work simply by binding excess water in the concrete mixture, thereby increasing the cohesiveness and viscosity of the concrete. The overall benefit is a reduction in washout of cement and fines, resistance to dilution with water as the mixture is placed, and preservation of the integrity of the in-place concrete. Another use of VMAs is to prevent segregation in high-slump concrete, SCC, or mixtures deficient in fines. Proper placement techniques shouldbe followed even with concrete treated with a VMA or anti washout admixture.
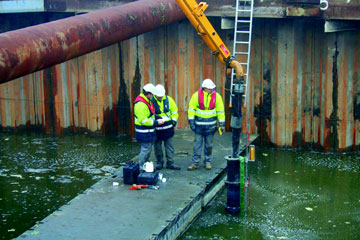 |
Permeability-Reducing Admixtures
The penetration of water and water-borne chemicals is the root cause of most of the destructive mechanisms that damage concrete. Additionally, the penetration of water through concrete can compromise interior living spaces, contaminate potable water reservoirs, or allow contaminated water to escape into the environment. Water can enter concrete though the network of pores and capillaries that forms during cement hydration, or through cracks and other voids in the concrete. Therefore, almost all concrete structures require protection from water. Common methods of protection include the application of surface applied sealers and membranes that act as a physical barrier between the concrete and the source of water. Increasingly, concrete structures are being designed with permeability-reducing admixtures (PRAs) to resist water penetration, in which the protection becomes an integral part of the concrete itself rather than just a surface barrier.
Conclusion
Chemical admixtures have become a very useful and integral component of modern concrete practices. Admixtures are not a panacea for every ill the concrete producer, architect, engineer, owner, or contractor faces when dealing with the many variables of concrete, but they do offer significant improvements in both the plastic and hardened state to all concrete. Continued research and development will provide additional reliability, economy, and performance for creating sustainable concrete.
Acknowledgement: The above article is compiled from 'Chemical Admixtures for Concrete', ACI Education Bulletin E4-12, published by ACI. To read in detail, please refer the original bulletin.