Floor Covering Basics and Options
Special Issue - eMagazine
Myriad options for flooring materials are available from synthetic to natural and manufactured to manmade. Many types of floorings have been developed in the recent past with advanced technologies to achieve a specific utility result with enhanced properties to suit the purpose and the location of their use including easier cleaning and maintenance. Each flooring material is endowed with its own unique qualities, functions, benefits and disadvantages, and it is appropriate to verify these properties and parameters before making a decision. The life cycle cost (LCC) of a flooring system also plays a vital role while determining the choice of flooring to be adopted. Factors such as durability, strength, hardness, resistance to the abuse, porosity, co-efficient of friction, reflectability, water absorption, have to be looked into carefully while assessing the required flooring system in addition to the ease of installation and subsequent maintenance.
Floor coverings can be broadly classified into four categories as Resilient, Non Resilient, Soft and Specialty Floor coverings based on their inherent flexibility properties. Non Resilient Floors- such as Concrete, Terrazzo, Ceramic, Vitrified, Hard Wood, Terracotta, Glass, Bricks, Stone etc, Resilient floors- such as Vinyl, Rubber, Bamboo, Asphalt, linoleum, Cork, Laminate etc, Soft floorings- such as Carpets, Specialty Floorings- such as decorative floors, coloured concrete, artificial stones, composite floors, hollow floors, etc are being extensively used in the construction sector giving rise to continuous innovation and design options.
Floor coverings can also be classified based on the location of their application in residential spaces, commercial spaces and industrial spaces with a sub classification addressing their application with interior or exterior spaces. This article deals with some of the commonly used floor coverings. However, there are no specific guidelines in respect of selecting a flooring material for a particular type of building as the building in its entirety comprises of many utility spaces. In general following steps are to be considered while arriving at a decision.
- Understand the purpose for which the building is created
- Understand space utilisation
- Estimate the traffic flow
- Assess the floor abuse
- Assess the environmental impact
- Assess factors such as durability, strength, hardness, absorption etc.
- Consider LCC-Life Cycle Cost
- Consider ease of installation and maintenance
- Consider aesthetic appeal
- Consider initial cost
- Consider the subgrade
- Consider availability and
- Conclude
Natural Stone Flooring
Natural stones are generally classified according to their mineral content and the process of their formation. Stones used in the building industry are characterized by durability and hardness, strength, amenability to dressing, appearance, weight, fineness of grain, requisite strength to withstand the imposed strain and compactness and porosity and absorption. They should also exhibit specific qualities such as capacity to withstand the ravages of time and weather. In its quintessence, three types of stones are commonly used.
Stones from Igneous Rocks
Igneous stones are formed due to the solidification of magma and then mineral gases and liquids penetrate the stone and create new crystalline formations and various colours. Of all igneous rocks, Granite is the most commonly used material. Granite varies greatly in colour depending on the range of the minerals present and the location of the quarry. When the mica in granite is white, it is known as muscovite, when it is dark it is biolite. In certain types of granite, hornblende is an important ingredient and it may be even more abundant than the micas. Due to its chemistry, granite is a much harder stone. It doesn't scratch as easily and rarely needs heavy-duty grinding.
Stones from Sedimentary Rocks
Sedimentary stones are layered rocks, formed through the accumulation and solidification of sediments, which may originally be made up of minerals, rock debris, or animal or vegetable matter. These stones come from such organic elements as glaciers, rivers, wind, oceans and plants. Tiny sedimentary pieces break off from these elements and accumulate to form rock beds. They are bonded through millions of years of heat and pressure and include limestone, sandstone and travertine.
Stones from Metamorphic Rocks
Metamorphic stones are formed from a pre-existing rock, subjecting themselves through heat, pressure, the effect of superheated fluids, or any combination of these forces. The change can be a development of crystalline formation, a texture change or even a colour change. While changing their forms from one type of rock to another, the original minerals of the stone re-crystallize, small crystals merge to form larger crystals with no changes in the mineral chemistry, fine-grained calcite in limestone re crystallizes to a coarse-grained calcite crystal structure in marble; or there may by a transformation into a different set of metamorphic minerals. This re-crystallization for example transforms the Shale into a colourful Slate or a Limestone becomes a multi coloured calcareous Marble and the grainy Sandstone alters into a highly crystallized sparkling siliceous Quartzite.
Surface Texture
Depending on the process of finish and the tools used different surface textures can be obtained. Commonly used surface textures are described hereunder;
Natural finish:
The surface comes with a very natural look. The natural surface texture is achieved by quarrying along its line of cleavage to reveal the natural grain & texture. These surfaces are normally not uniform but greatly depend on the crystal formation. This type of finish is predominantly used outdoors where it is appreciated for its non-slip quality. It is often used with slate and with some kinds of sandstone.
Honed finish:
It is produced by grinding a surface with high grit material to a uniform specification using mechanical grinders without producing a reflective surface. Honed stone colours are not as exciting as polished stones. This surface is smooth, but often very porous.
Polished finish:
Polished surface texture is a reflection of polished crystals that bring out the brilliant colours and grains of natural stones. The shine on stone surface comes from polishing cakes, soaps and powders used during fabrication and not from any coating. Polishing is the most frequently applied finish that adds brilliance with mirror effect to the stone surface.
Flamed finish:
It is a rough surface that is developed due to the bursting of crystals when the stone is heated. This surface gives an irregular textured finish. The flamed finish is frequently used on floor tiles and vertical applications. Colour and particulate or vein patterns vary from block to block. The major uses includes - chemistry and fire resistant work surfaces, fireplace facings & inner hearths, etc. where heat is an issue.
Acid Wash finish:
Liquid acidic rinsing process is applied to the surface of the stone. This will moderately etch the stone according to the acid percentages in the rinse and the type of stone; typically a mixture of muriatic acid and water is used as rinsing agent. This is done to take the shine off of polished stones down to a honed finish. It also sometimes makes the stone slip resistant. Acid washing tends to enhance the colour and character and can be used for interior and exteriors depending on the stone and the type of acid washing.
Sand Blasted:
Producing a finish similar to cleft, sand blasting involves blasting of surface using fine graded sand at high pressure. It is characterized by a textured surface with a matte gloss. Sandblasted stone can be use anywhere. It is highly slip resistant and very durable making it ideal in wet areas such as pool decks, steps and common areas.
Saw cut finish:
The saw cut finish has acquired its name owing to the saw cuts that are made on the surface of stone. When the stones are broken free of the cut layer they are shaped to uniform size. Saw Cut finish offers complimentary accents to other types of stone work. It is generally used for walls, gate entries, patios, landscape design applications etc.
Bush Hammered:
A pounding action that develops a textured surface. The top surface is pneumatically tooled to produce a pitted or grooved surface finish.
Antique finish:
Chiselled, sandblasted then acid washed. This finish is an old world reclaimed stone look. The stone resembles stone reclaimed from ancient sites.
Chisel finish:
The finish is obtained by dressing a stone with a set of chiselling tools depending on the level of finish desired. The surface of a stone finished in this way resembles pointed work, but it is not so regular. Working stone with a tooth chisel is one of the methods of stone dressing that requires extreme skill.
Common Materials
Natural stone finishes are used for facades, floor coverings, wall cladding and variety of other interior and exterior applications depending upon the interior design to enhance the aesthetics, to meet the required functional and utility parameters. Most commonly used natural stones are listed below. Table 1 shows Physical properties of commonly used natural stones.
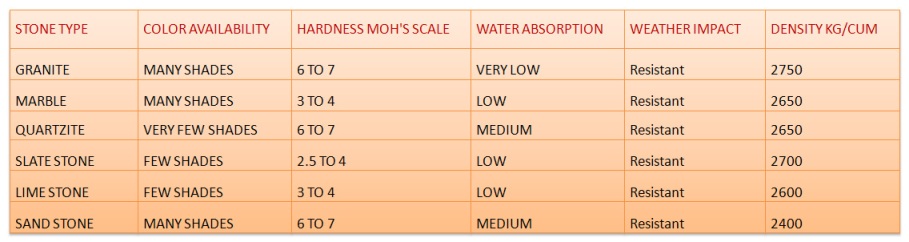
Granite
the hardest building stone, and occupy a prominent place among dimensional stones. Due to its hardness, resistance to weathering, capability to take mirror polish, vibrant colours and textural patterns, granite slabs and granite tiles are extremely popular. The principal characteristics of granite also include high load bearing capacity, crushing strength, abrasive strength, amenability to cutting and shaping without secondary flaws, ability to yield thin and large slabs and - above all - durability. Due to highly dense grain, it is impervious to stain. Polished granite slabs and granite tiles have achieved a special status as building stones globally.
Marble
the most accepted stone formed from limestone with heat and pressure over years in the earth's crust due to re-crystallization. Impurities present in the limestone during the re-crystallization period affect the mineral composition of the marble which is formed. The minerals that result from impurities give marble a wide variety of colours. The purest calcite marble is white in colour. Marble containing hematite is reddish in colour. Marble that has limonite is yellow, and marble with serpentine is green in colour. Marble stones make a perfect choice for architecture and sculpture apart from being used extensively for both interior and exterior flooring and cladding applications.
Limestone
is the calcareous sedimentary rock composed of calcite (CaCO3). The rock which contains more than 95% of calcium carbonate is known as high-calcium limestone. Re-crystallised limestone takes good polish and is usually used as decorative and building stone. A part of calcium when replaced by magnesium, it is known as magnesium lime stone or dolomite limestone. Natural limestone is generally used in flooring, wall cladding, vanity tops and to pave the floors of large commercial complexes, hospitals, airports, shopping malls, railway stations, parks etc.
Quartzite
The parent rock for quartzite is quartz-rich sandstone. As sandstone becomes deeply buried, rising temperature will fuse the quartz grains together forming the extremely hard and weather-resistant rock quartzite. Like marble, quartzite comes in many colours, but when pure it is light-coloured. Quartzite tends to have a sugary appearance, and when broken the fractures cut through the sand grains, not around them as with a sandstone. Quartzite stones are extremely hard and weather resistant stones. The natural quartzite stones make a perfect choice for wall-cladding, roofing, flooring and all other types of interior & exterior applications. Having granolithic texture, these Indian natural quartzite stones are fireproof and non-slippery in nature.
Sandstone
Sandstone is a sedimentary rock group which is mostly made up of tiny grains of quartz. These natural sandstones are used for interior as well as exterior decoration including flooring, paving, wall cladding, etc. The weather resistant natural sandstones are extremely hard and tough material.
Slate stone
are metamorphic-argillaceous rocks, and are normally fine to medium grained, moderately hard & compact, less homogeneous with varying textures & shades. It has an ability to split into thin layers along the plane of cleavages due to flattened & elongated minerals along the plane of cleavage. Slate stones render a graceful, natural finish to any building and are more cost-effective than other wall and floor coverings. All natural slate stones are fireproof and slip-resistant.
Absorption Rating
The absorption rating refers to how porous a given material is. The more absorbent it is, the more susceptible it will be to stains, as well as cracking damage in freezing conditions. In general, Sandstone is the most porous natural stone material, Travertine, Limestone, and Slate have medium absorbency, and Granite is relatively waterproof. Polished materials also absorb less water than honed surfaces. There are four levels of absorption that a floor covering can have;
- Non-vitreous: This is the highest absorption level. In most cases non-vitreous material should not be used in any damp environment.
- Semi-vitreous: While these are less absorbent, the more liquid they are exposed to, the more maintenance they will require.
- Vitreous: This is the standard absorption level for floor coverings and these materials are generally considered appropriate for most low to mid traffic indoor and outdoor applications.
- Impervious: These materials are resistant to the absorption of liquids and thus will be easier to maintain. They are often used in high traffic commercial applications
Indoor versus Outdoor Rating
Some natural stone flooring materials are more suited to outdoor applications than others. Many of the factors above will determine whether a material should be used in an open air environment. Non-vitreous materials will be subject to staining through dirt and acid rain, as well as cracking when absorbed materials freeze and expand. Stones which have a low coefficient of friction will also pose a slipping hazard during rain and snow storms.
Oxidation
Natural stone materials are formed beneath the earth over millions of years, and often contain a variety of disparate elements. Sometimes iron is present in these materials, which can manifest as bright red and amber hues in the surface of the stone. The problem in an outdoor environment is that, those traces of iron can oxidize, a process more commonly known as rusting. This can cause the entire tile to degenerate over time.
Coefficient of Friction
This measures how slippery various materials are. The higher the coefficient, the more traction a tile will have. This number is especially important in moist environments such as bathrooms and kitchens, as well as high traffic commercial areas. The Americans with Disabilities Act requires that flooring material have a minimum of a 0.6 dryness coefficient.
Industrial Flooring
There are different types of industrial flooring available today in the market and it requires in depth understanding of the behavioural patterns of the sub-grades and the expected abuse the final surface is going to be subjected to. Industrial flooring plays a crucial role in enhancing the productivity, safety and security which has gradually over a period of time changed from the traditional cement flooring to the modern dust-free monolithic floors. Safety, high wear resistance, abrasion resistance, impact absorption, easy installation, cost efficiency, easy cleaning and maintenance are the main aspects to be considered when opting for industrial flooring.
Factors to be considered in choice of industrial flooring
Choosing the right industrial flooring could be a challenging and daunting task. One should take into consideration a few factors like durability, installation, cost involved and resistance to rough and harsh conditions. Further it should also add to the aesthetic appeal. Robustness and low maintenance cost are also to be considered before installing industrial flooring. The solution implemented should last a life time and should satisfy all the industrial needs and statutory requirements. By installing superior quality corrosion resistant, anti skid, fire resistant and heavy duty industrial flooring you can be assured of maximising your production.
Types of industrial flooring
- Coated flooring: A wide range of epoxy, polymer and polyurethane coatings are available. These are all hard wearing and provide attractive dust free surfaces. Any requirement, such as specific chemical resistance, non-taint products for the food industry, corporate colour schemes and various grades of anti-slip aggregate can be customised wherever required. This is an excellent surface protection for industries as they deliver the toughest performance and are chemically resistant. These flooring options can be easily and quickly installed in a short space of time and permits floor are to be used quickly. As they are available in a wide array of colours it enhances the overall look of the working environment.
- Rubber flooring: This flooring is long lasting, durable, stain resistant, water resistant, high impact resistant and very comfortable underfoot. It is also very easy to clean and maintain. Rubber flooring is the 'coolest' architectural product, not just in terms of current trends but also in terms of thermal quality. Cool in summer and far warmer in winter than ceramic tiles, natural stone and concrete.
- Vinyl flooring: These types of industrial flooring are highly durable and stain and tear resistant. They are available in plethora of shades in tile and roll form.
- Resin flooring: They are extremely tough and durable as the strength of the resin prevents damage from impact and increases the capacity of the floor to bear weight. As they are slip resistant it ensures maximum safety.
- Metal Flooring: This is another hard flooring material to experience the shock of the new. Aluminium or galvanized steel sheets are normally used and comes textured with relief pattern to make a non-slip surface. They are usually glued or screwed in place on a level sub-floor. Appropriate sound proofing is also needed as it can be noisy.
- Concrete Flooring: This is hard, brutal, raw and defiant. Yet, this material has the ability to look soft and matt as suede. As a setting for strong modern furnishing in chrome and leather, concrete has unbeatable character. It can be treated in a variety of ways to alter its texture and color. Patterns can be created by scoring or by embedding stones in the floor while it is still wet, and the final floor sealed and polished. To add color but reserve the soft-looking texture, pigments can be added to the basic mix; alternatively, it can be painted with special floor paint. For the sleekest and most sophisticated, cover with acrylic or epoxy resin toppings. The finish is exceptionally glossy and looks almost liquid. Tough polyurethane finish varnish will render the floor even shinier as well as protect the surface from scratches and scuffs.
Commercial and residential Spaces
Spaces in this context include buildings such as dwelling units, apartments, schools, offices, malls, trade centers, public buildings etc. When it comes to choosing flooring for commercial buildings, there are often a variety of factors to consider, from the cost of various materials to how suited they are to specific settings and applications. Because of the higher traffic levels with commercial structures, it is also important to determine the product's durability and strength, as well as the required maintenance procedures. In residential spaces importance is given to the elegance and appeal due to lower traffic level.
Under this category we have options varying from traditional coloured cement flooring to the most intrinsically manufactured 3d tiles. While some prefer seamless, joint less flooring, some opt for regular flooring with spacers. Some of the most commonly used floor coverings are ceramic, vitrified, terracotta, natural stones like tandoor blue, cement flooring with colouring oxides, hard wood, wood laminates, bamboo, variety of cement tiles, china mosaic, terrazzo, stamped or stencilled concrete, carpets, etc. Only a few are discussed here.
Vitrified Tiles and Ceramic Tiles
Ceramic tiles are made from natural clay that is mixed with water and moulded. Manufacturers apply a glaze to the tile to protect it from ingress of water and scratches, and then fire the clay in a kiln to achieve the hardening. Ceramic tiles come in overabundance of colours and sizes. Glazing is a must always for protection.
Vitrified Tiles have far superior properties compared to natural stones because being a manufactured product their quality is controlled. Vitrified tiles posses much better mechanical strength, scratch resistance, resistance to acids, alkalis and chemicals, resistance to staining etc compared to natural stone flooring.
Vitrified tiles are very similar to ceramic tiles, but are made with slightly different elements. The clay is mixed with quartz and feldspar before it is heated in the kiln. These extra ingredients melt, creating a glass element inside the tile. This glass component makes the vitrified files very hard and resistant to any type of absorption. Vitrified tiles, unlike ceramic tiles, are rarely glazed. Instead, a dye is mixed in with the clay before it is fired. This dye makes the clay a uniform colour, so even if the vitrified tile is scratched, the colour will stay the same. Instead of being glazed, vitrified tiles are either polished or unpolished.
Polished tiles have a bright sheen, while unpolished versions are rougher and have a more natural look. Vitrified tile starts out as a wet blend of 40 percent mineral clay and 60 percent silica and feldspar. This mix is moulded into tile shape, and then baked in a furnace called a kiln at 2,190 degrees Fahrenheit. This high-temperature baking process turns the mineral mixture into a perfectly flat, rock hard, nonporous, durable, porcelain-like tile. The vitrification process produces tiles of uniform size and thickness, ready to install.
Timber Flooring
Timber flooring is very popular due to its aesthetics and character. Each tree is different with its own unique texture and grain pattern. Timber floorings are eco friendly, durable, flexible and easy to maintain and add elegance to the space. Timber flooring can be categorised as;
- Solid wood flooring- Solid wood flooring is milled from a single piece of timber that is kiln or air dried before sawing. Depending on the desired look of the floor, the timber can be cut in three ways: flat-sawn, quarter-sawn, and rift-sawn. The timber is cut to the desired dimensions and either packed unfinished for a site-finished installation or finished at the factory. The moisture content at time of manufacturing is carefully controlled to ensure the product doesn't warp during transport and storage.
- Engineered wood flooring - composed of two or more layers of wood in the form of a plank. The top layer is the wood that is visible when the flooring is installed and is adhered to the core. The increased stability of engineered wood is achieved by running each layer at a 90° angle to the layer above. This stability makes it a universal product that can be installed over all types of subfloors above, below or on grade. Engineered wood is the most common type of wood flooring used globally. Engineered wood flooring has other benefits beyond dimensional stability and universal use. Patented installation systems allow for faster installation and easy replacement of boards. Engineered wood also allows for a floating installation where the planks are not adhered to the subfloor or to each other, further increasing ease of repair and reducing installation time.
- Laminate Flooring- Laminate flooring has an imprint of timber impregnated on a board giving it the look of a timber floor. It is a much cheaper option to a real timber floor and more durable. Laminate consists of 4 to 6 layers which are heat pressed together in one large sheet, then cut into various sizes. Laminate boards have a specific joining system to ensure a structurally stable floor. Laminate flooring comes pre-finished so there is no need for sanding and coating.
- Bamboo Flooring- Bamboo has gained a reputation as an eco-friendly, highly renewable source of material. Compared to wood it grows and attains maturity much faster. Moso Bamboo is the primary species used for the manufacturing of flooring and plywood. Moso bamboo can grow up to 47 inches in 24 hours and 78½ feet high in 40 to 50 days. It takes about 3–5 years for bamboo to reach full maturity. Traditional hard woods can take 20–120 years to mature. Fresh & mature bamboo clums are split and flattened lengthwise into strips of equal dimensions. These are processed & kiln dried before being pressed against each other and glued under high pressure to form boards (raw planks). Strand woven boards are manufactured to achieve greater strength and stability. The bamboo clum is crushed lengthwise and the strands are pressed & glued at extreme high pressure to produce boards (raw planks). The raw planks are then milled to form tongue & groove on the edges.
- Cork Flooring- Cork flooring is a great solution for low-maintenance, beautiful to look at, easy to care for, and soft and warm to touch. Cork flooring is durable enough to handle all kinds of traffic and insulates against sound, noise and temperature change. An extremely durable flooring material, cork flooring has outstanding moisture and heat resistance and resists cracking. Cork flooring is known for its resilience and always retains its shape and elasticity. Cork flooring easily blends with other décor and furniture. It is available in a wide range of patterns. Each batch of cork flooring demonstrates unique patterns, making your floor the only cork flooring of its type.Cork flooring is manufactured from cork, a natural product. Cork made from the bark of cork oak tree with a minimum maturity period of 25 years. The older the tree is the better quality of cork it can produce, as the bark becomes smoother every time it re-grows after the harvest. Cork flooring is manufactured as tiles or planks in various thicknesses. The baking process increases cork's durability for other uses, including cork flooring. After being cut to standardized dimensions, it is then sorted by colour, and sealed with polyurethane, or wax. There is practically no waste from the harvesting of the raw material to the manufacture of flooring.
Vacuum Dewatered Flooring
A design mix with a medium workability is placed in forms, levelled and vibrated using screed vibrators. Vacuum to the concrete surface is then applied through porous mats connected to a vacuum pump. These mats are placed on a fine filter spread or pad which prevents cement particles getting removed during the process. The vacuum is then created by a vacuum pump at the rate of 0.08 Mpa. This vacuum reduces the water content by about 20% in general. The reduction is greater nearer to the mat and it is usual to assume the suction to be fully effective over a depth of 100 to 150 mm. The removal of water this way results in the settlement of concrete by about 3% of the depth over which suction acts.
It is important to know that no suction of water actually takes place during the vacuum dewatering process. Due to fall in the atmospheric pressure communicated to the fresh concrete matrix during the vacuum process, compaction of concrete due to atmospheric pressure takes place. Thus, the actual quantum of water that is removed would be equal to the contraction in the total volume of concrete. The final water/Cement ratio thus is reduced before the concrete sets yielding a concrete with higher density, higher strength, lower permeability and higher resistance to abrasion.
Coloured Concrete
Concrete flooring can also be finished using different colour pigments and patterns. These pigments are available in powder, liquid & in granular forms. There are many patented patterns and colours available in the market. Generally these are classified under stamped concrete and stencilled concrete depending upon the method used to produce the imprints. The coloured concrete in today’s context is produced using different techniques such as dry–shake toppings, chemical stains, dyes, tints, colour coatings or by exposing the coloured aggregates, etc.
Table 2 shows comparison between different types of floor coverings.
Conclusion
As per the industry analysis, India is poised to be number one in the world market by 2015 in terms of production and consumption of tiles. India is next to China and Brazil, in third position, in the tile segment and Asia consumes approximately 65% of the total production in the world. The Indian tile Industry despite an overall slowdown of the economy continues to grow at a decent rate of 20 per cent annually due to the emerging demands in housing and infrastructure segments.
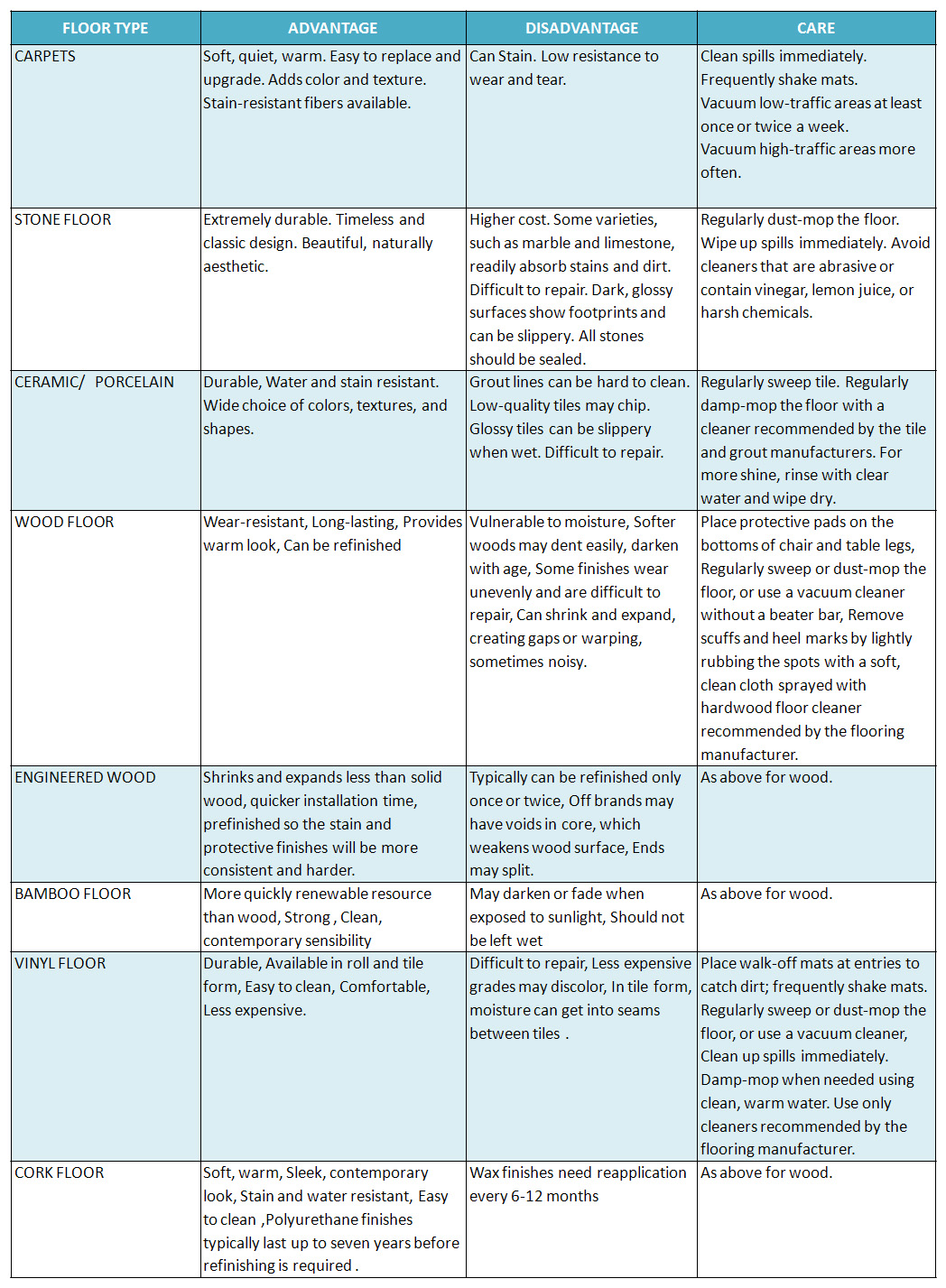
Table 2- comparison of different floor types