Formwork and Scaffold Safety
Bureau Built Constructions
1.0. FORMWORK SAFETY
Formwork functions purely as a temporary structure that holds the fluid concrete in the desired and designed position until it is able to support its own weight and the various loads imposed on it. It not only supports its own weight and that of the freshly placed concrete but also other construction live loads including materials, equipment, and workmen. Fresh concrete will accurately reflect the shape, texture and finish of the surface against which it is cast. The formwork is critical to the final appearance of the hardened surface. Any imperfection or inaccuracy in the formwork will be reflected when the formwork is stripped off.
Formwork is one of the important components due to its cost factor and plays a major role in deciding the construction methodology especially when it comes to high rise structures. Often designers devote considerable time in selecting the minimum amount of concrete and steel for a structure without devoting adequate attention to the impact of the formwork that must be constructed to form the concrete. For most structures, more time and cost are required to make, erect, and dismantle the formwork than the time and cost to place the concrete or reinforcing steel in position. For some structures, the cost of formwork exceeds the cost of the concrete and steel combined. Formwork has a significant impact on the cost, time, and quality of the completed project.
2.0. FORMWORK FAILURES
Formwork failures happen at the time of placing concrete or during the maturity of concrete. Generally, some unexpected event causes one member to give away, then others become overloaded or misaligned and the whole formwork structure collapses. The failure of formwork is always embarrassing, unsafe and expensive. Some of the main causes are listed below.
- Improper or inadequate shoring
- Inadequate bracing of members
- Lack of control of rate of concrete placement
- Improper vibration or consolidation of concrete
- Improper or inadequate connections
- Improper or inadequate bearing details
- Premature stripping of formwork
- Improper or lack of, design of formwork
- Inadequate strength of form material
- Failure to follow codes and standards
- Modifications of vendor-supplied equipment.
- Negligence of workers or supervisors
- Unstable or improper base
2.1 Prevention of Formwork Failures
There are many risks in the process of erecting and dismantling of forming systems. Every precaution should be taken to ensure a safe working environment. Below is a partial list of rules that can be used to reduce the potential of formwork failures.
- Prepare a formwork plan that includes detailed drawings and written specifications for fabricating, erecting, and dismantling of the formwork. Such a schedule should be prepared by a competent person.
- Follow all state, local, and federal codes, ordinances, and regulations pertaining to formwork, shoring, and scaffolding.
- Post guidelines for shoring and scaffolding in a conspicuous place and ensure that all persons who erect, dismantle, or use shoring are aware of them.
- Follow all instructions, procedures, and recommendations from manufacturers of formwork components used in the formwork.
- Survey the jobsite for hazards, such as loose earth fills, ditches, debris, overhead wires, and unguarded openings.
- Ensure adequate fall protection for workers during erection of formwork, pouring of concrete, and dismantling of formwork.
- Inspect all shoring and scaffolding before using it, to ensure it is in proper working condition and to ensure workers are using the equipment properly.
- Make a thorough check of the formwork system after it is erected and immediately before a pour, in particular connections between formwork components.
- Never take chances. If in doubt regarding the safety, contact a safety officer and management. It is best to prevent an accident.
2.2 Scaffold Safety
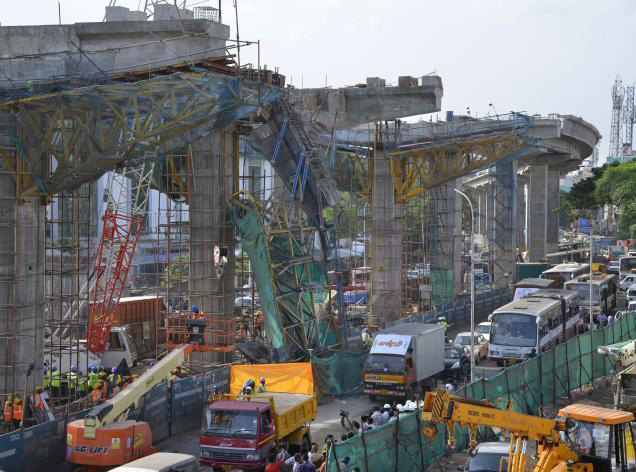
Scaffolds are temporary, elevated platforms with supporting structures that are used to support workers and their materials at construction sites. As defective scaffolds put workers at great risk, these structures should be inspected before each work shift, as well as after any event that may have caused damage.
The scaffold should be capable of supporting its own weight and at least four times the maximum intended load to be applied or transmitted to the scaffold and components. Suspension ropes should be capable of supporting six times the maximum intended load. Guardrails should be able to withstand at least 200 pounds of force on the top rail and 100 pounds on the mid rail. On complex systems, the services of an engineer may be needed to determine the loads at particular points.
Accidents involving scaffolding mainly involve people falling, incorrect operating procedures, environmental conditions and falling materials caused by equipment failure. The causes of scaffolding accidents include failures at attachment points, parts failure, inadequate fall protection, improper construction or work rules, and changing environmental conditions (high winds, temperature extremes or the presence of toxic gases). Additionally, overloading of scaffolding is a frequent cause of major scaffold failure.
3.0. GENERAL REQUIREMENTS
- Scaffold components must be able to support at least four times their maximum intended load.
- The scaffolding platform should be fully planked, with no more than a 1-inch gap between planks or planks and uprights.
- The gap between the last plank and the uprights should be less than 9½ inches.
- All platforms should be at least 18 inches wide.
- Guardrail systems or personal fall-arrest systems should be employed where needed.
- The scaffold (minus the guardrail) should be 14 inches or less from the work face, or 18 inches for plastering and lathing.
- Planks should not extend past the ends of the scaffold frames more than 12 inches.
- Casters must be locked before work begins.
- Platform surfaces should be secured and cleated.
- The platform should be free from clutter and any tripping hazards.
- Scaffolding, material and workers must remain at least 10 feet away from power lines.
- The top and bottom plank surfaces should be visible and free from opaque finishes.
- Abutted planks must rest on separate support surfaces.
- Scaffolding components made by different manufacturers must fit together without force.
- A defective scaffold must be removed from service.
3.1 Scaffold Requirements
- The height-to-base width ratio should be less than 4:1. Scaffolds that do not meet this requirement must be secured using ties such that the following are true:
- The inner and outer legs are supported;
- Vertical ties repeat every 20 feet or less for scaffolds that are 3 feet or less in width;
- Vertical ties repeat every 26 feet or less for scaffolds that are greater than 3 feet in width; and
- Scaffolds with a height-to-base ratio of greater than 4:1 are restrained from tipping by guying, tying or bracing.
- All scaffold frames and uprights should use base plates, and mud sills are required if it is set on dirt.
- Footings should be level, sound and rigid. No settling should have occurred.
- Unstable objects, such as blocks, bricks and buckets, should not be used as work platforms or to support scaffolds.
- Scaffolds should be erected on adequate and firm footings that can support four times the intended load without settling.
- Riggers should be secured and installed correctly.
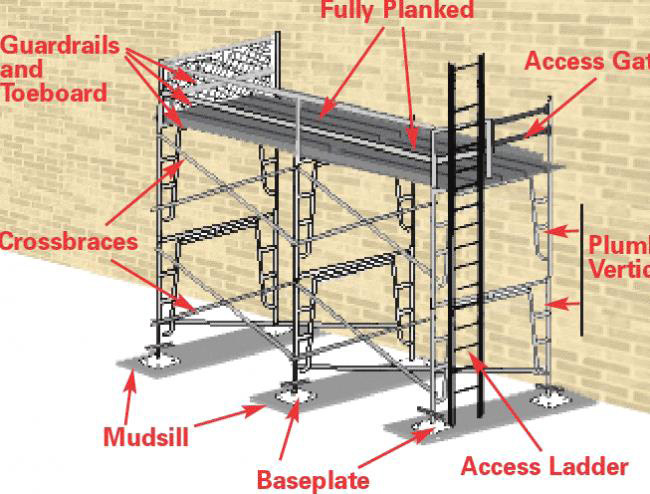
3.2. Scaffold Access
- No more than a 2-foot step up or down or a 14-inch step across should be required to get on or off the platform.
- The first rung of the ladder should not be more than 2 feet above the ground.
- Hook-on and attachable ladders should be of a type designed for use with the scaffold.
- Add-on ladders must have a rung length of at least 11½ inches.
- Built-in ladders that are part of the scaffold frames must have a rung length of at least 8 inches.
- Wooden planks must be free of cracks and splits greater than 1/4-inch.
- Metal components must be free of bends, cracks, holes, rust, welding splatter, pits, broken welds, and non-compatible parts.
- Ladder rungs must line up vertically for the entire height of the scaffold.
- Cross-braces are prohibited for use as a point of access, or for climbing up or down.
- Ladders should be positioned so as to not tip the scaffold.
- Hook-on and attachable ladders must have rung lengths of at least 11½ inches.
- Hook-on and attachable ladders must have uniformly spaced rungs, with a maximum spacing between rungs of 16¾ inches.
- Stairway-type ladders must have slip-resistant treads on all steps and landings.
- Ramps and walkways 6 inches or more above lower levels must have guardrails.
- Ramps and walkways must be inclined with a slope less than 20º above the horizontal.
- Integral, pre-fabricated scaffold access frames should be constructed for use as ladder rungs, and have rung lengths of at least 8 inches.
- Safe access must be provided for all scaffold platforms that are more than 2 feet above or below the point of access.
- Rest platforms must be installed every 35 vertical feet.
3.3 Use
- A scaffold and its components must not be loaded beyond their capacity.
- The use of shore or lean-to scaffolds is prohibited.
- Any damaged component must be removed, repaired or replaced.
- Occupied scaffolds must not be moved, unless the scaffold is designed for movement by a professional engineer or is a mobile scaffold.
- The scaffold should not be used in slippery conditions, such as when snow or ice is present, except to remove such hazards.
- Tag lines should be used to control loads being hoisted onto or near scaffolding.
- Tools, material and debris should be removed from the scaffold to prevent accumulation and trip hazards.
- No makeshift devices, such as boxes or barrels, may be used to increase the working-level height.
- No ladders may be placed on the top of the scaffold deck, except under certain large-area scaffolds.
- Provisions need to be made to prevent the platform from deflecting more than 1/60-inch.
3.4. Fall Protection
- Some form of personal fall protection is required on all scaffolds higher than 10 feet.
- Fall-arrest systems must be used in high-wind or storm conditions.
- Guardrails must be free of sharp edges.
- Mesh or screens, if equipped, must extend from the top of the guardrail or platform.
- Steel or plastic bands may not be used as railings.
- Requirements regarding falling objects are:
- Employees on a scaffold must be protected by toe boards, debris nets or a canopy.
- The area below must be protected by barricades, canopies or toe boards on scaffolds higher than 10 feet.
- Toe boards must be able to withstand 50 pounds of force and be 3½ inches wide.
4.0. CONCLUSION
A competent person to oversee the scaffold selection, erection, use, movement, alteration, dismantling, maintenance and inspection becomes an important parameter. Further, training of workers who work on high scaffolds is also to be ensured in order to achieve zero accident status. In addition, the project engineer and the supervisor should be knowledgeable about the type of scaffolding to be used and about the proper selection, care and use of fall protection equipment (perimeter protection, fall protection/work positioning belts and full harnesses, lanyards, lifelines, rope grabs, shock absorbers, etc.)
Reference:
1] Scaffold Inspection by Nick Gromicko