GLOBAL TRENDS
Civil Engineering News
Construction Progress Monitoring
Monitoring progress on a construction project is critically important, the task can prove challenging and time consuming, particularly if it involves assessing input from multiple parties. In an effort to make construction progress monitoring more efficient, a software program has been developed that uses jobsite photographs, project schedules, and building information modeling (BIM) to rapidly assemble a three-dimensional (3-D) model of a project's components and visually depict the extent to which construction is meeting scheduling requirements. The approach, which is referred to as four-dimensional augmented reality, or D4AR, might also be suitable for such tasks as monitoring safety, visualizing a jobsite remotely, and documenting as-built conditions.
As a graduate student at the University of Illinois at Urbana-Champaign, Golparvar-Fard set out as part of his doctoral dissertation to try to make the process of monitoring construction progress more efficient. In 2006 he began attempting to superimpose 3-D BIM models on time-lapse photographs of construction sites as a way of revealing performance deviations. However, he realized that such an approach required photographs that depict project elements at closer range. As a result, with financial support from the National Science Foundation, he and his advisers decided to investigate the use of "existing collections of unordered photos" at a job-site, Golparvar-Fard says. The decision in part derived from the fact that digital cameras are ubiquitous at construction sites today and can readily supply large numbers of inexpensive, high-resolution photographs.
To convert photographs from a construction site into a format that could provide a coherent basis for performance assessment, Golparvar-Fard developed a modeling system that begins by automatically assembling unordered collections of digital photos into a 3-D model of the site. The D4AR modeling system is based on various algorithms related to computer vision, machine learning, and computer graphics, he says. Because the modeling system can automatically determine where on a construction site a photograph was taken, there is no need to use Global Positioning System (GPS) coordinates or wireless Internet access.
As new photos are added over time, the system creates additional models, comparing them with existing models of the same location at a construction site. In this way, the system generates four-dimensional models, that is, three dimensions plus time, Golparvar-Fard says. As a result, the D4AR system "captures the actual status of the project," he says.
For projects not designed with the use of BIM, users can manually assess how actual project performance compares with expected performance. However, for projects developed by means of BIM, the D4AR system can be programmed to carry out this assessment automatically. The D4AR model depicting the current project status based on the photographs is superimposed on the original model that was prepared by means of BIM. The system then automatically compares the two models and uses the colors of a traffic light to depict performance deviations. For example, project elements found to be ahead of schedule are shown as green, while elements determined to be behind schedule appear as red.
Among the benefits of the D4AR system is the ease with which it can be used, Golparvar-Fard says. The software requires no special training, he says, just the ability to take digital photographs. "The beauty of the system is that it is really easy to use," he says. "Everybody on a jobsite knows how to take photographs." Initially, Golparvar-Fard envisioned that the D4AR system would be used by contractors and project owners. "But eventually when we made this system that has the ability to generate models, even architects and engineers started approaching us," he notes. In addition to performance monitoring, the technology could be used for such tasks as managing site logistics, conducting site walkthroughs, and conducting checks related to quality assurance and quality control.
Seeking to commercialize the technology, Golparvar-Fard is collaborating with his former academic advisers: Feniosky Pena-Mora, Sc.D., P.E., M.ASCE, now the Edwin Howard Armstrong Professor of Civil Engineering and Engineering Mechanics and a professor of earth and environmental engineering and computer science at Columbia University, and Silvio Savarese, Ph.D., now an assistant professor of electrical and computer engineering at the University of Michigan. Golparvar-Fard is working with a handful of companies that are using the D4AR system. At present, the Turner Construction Company, of New York City, is conducting a pilot study of the system as part of its work in constructing the 800,000 sq ft mass transit complex in New York City known as the World Trade Center Transportation Hub. Golparvar-Fard, who previously worked for Turner Construction, says that the firm is using the D4AR system for such purposes as monitoring quality control and checking the installation of various systems.
Also under development is a "hybrid" version of the core D4AR technology, and it too is benefiting from financial support from the National Science Foundation, Golparvar-Fard says. Known as the Mobile Augmented Reality System (MARS), the hybrid approach matches photographs taken with a smartphone to the corresponding part of the project, enabling the user to conduct progress monitoring or assess quality. Like the core D4AR technology, the hybrid version automatically calculates the location and orientation of the objects in the photographs. To commercialize MARS, Golparvar-Fard and his research collaborators and partners on the venture Jules White, Ph.D., an assistant professor at Virginia Tech, and Hyo Joon Bae, a graduate student in the electrical and computer engineering department there formed a company called PAR Works, which is a subsidiary of the venture capital firm Allied Minds, Inc., of Boston.
Another application currently under development would use the D4AR technology to assess the stability of a structure in the wake of a disaster. To this end, a robotic platform would be used to take photographs of building elements after an earthquake or other disaster. The photos would then be used to generate models that could be used to detect the presence, size, and other characteristics of cracks, Golparvar-Fard says. Another application, this one involving the use of a thermal camera, would rapidly create 3-D spatiothermal models of a building. The models would capture the actual energy performance of the building and compare the findings with the building's expected performance, which would be modeled using computational fluid dynamics. The program would thus be able to assess the cost associated with energy loss, Golparvar-Fard says, and help building owners decide whether to retrofit their buildings in an effort to save energy. -JAY LANDERS
3D printing gains design traction
-by Korky Koroluk
The degree of acceptance of 3D printing has been astonishing. The concept has been around for a couple of decades and was called additive manufacturing or fast prototyping, depending on the use that was made of it.
Architects are finding that a printed model of a proposed building is useful to show clients during the design stage. Changes can be made to suit the client; a revised model is printed and shown to the client.
There are 3D printing firms that are already making a specialty of such service.
All sorts of things can be used as the "ink," in 3D printing. It can be various metals, cement-based mortar, plastic, even construction waste ground up and mixed with cement. Then the print head moves around the site, extruding "ink" in a pattern that has been loaded into the computer that drives the process. It follows; then, that mud can also be used, and an Italian 3D printing firm named WASP has developed an easily transportable printer that can quickly create basic houses from mud and natural fibres that are usually already available in the impoverished areas where such basic housing is needed. It's just a high-tech way of building houses from adobe bricks.
The Chinese have done several demonstration projects using the 3D process, including one in which they printed 10 buildings in a day. That's where they used construction waste in the process.
The Shanghai-based firm WinSun Decoration Design Engineering has printed and shown off a five-storey apartment. They are calling it the "world's tallest 3D-printed building." Right next door they printed a building that looks much like an old Georgian mansion with a floor area of 1,100 square metres. Printing 10 buildings in one day involved pre-printing walls that were then lifted into position. The roofs, however, are conventional. Apparently the 3D process hasn't advanced far enough yet to do roofs.
But looking at photos of those buildings under construction made me think that precasters ought to be interested in 3D printing.
Things like walls, floor panels and stairs lend themselves to precasting, especially since the 3D process allows cavities and spaces to be left for wiring and plumbing. Other things are possible too, like architectural detailing that would be too complex to build using any other technology. That gives architects a wider range of options to show their clients. As for 3D printed housing, one headline I saw told me that "You may soon be living in a 3D-printed apartment."
Still, as 3D technology becomes more firmly entrenched in the main stream, people are not only perfecting the technology but finding new ways to make it useful.
To Read more: http://journalofcommerce.com
'Green' liquid asphalt cement
-by Korky Koroluk
Researchers looking for alternatives to products made from fossil fuels have been interested in algae for some time. Some of the tiny plants contain a lot of natural oil. That's why science has made significant progress in using them to manufacture "biodiesel" as a sustainable alternative to conventional diesel.
A group of researchers in France have come up with a way to use algae in the manufacture of "green" asphalt, since it's made without using petroleum.
Microalgae is useful for making more than biodiesel. French researchers have recently demonstrated the viability of what they're calling bioasphalt. They've published the results of their work in the April issue of the journal ACS Sustainable Chemistry & Engineering.
Microalgae are single-celled plants that range in size from a few micrometres to a few hundreds micrometres, depending on their species. They have no roots, stems or leaves, but they are capable of performing photosynthesis and are thus important for life on earth.
Scientists tell us there are somewhere between 200,000 and 800,000 species, only about 35,000 of which have been scientifically described. Researchers in France have used them to make compounds of use to the cosmetics industry, and it is the residue from that process that they use to create a black, viscous material that closely resembles the asphalt derived from oil petroleum.
The chemical composition of bioasphalt is completely different from its oil-based counterpart. But it can be used to coat mineral aggregates, instead of coating them with what road builders call liquid asphalt cement, or bitumen.
Researchers have already found that aggregates treated with bioasphalt are capable of supporting mechanical loads. Now they're testing its behaviour over time, as well as studying costs in an attempt to evaluate its potential for large-scale production. But algae-based asphalts are not the only bioasphalts being studied.
In the Netherlands, research is being done in the use of lignin, a natural adhesive material, in another form of synthetic asphalt. Lignin gives structure to all kinds of plants and trees. It is, for example, an important part of straw.
People have long guessed that both algae and straw could be important as we make the transformation to a low-carbon economy, and several governments and companies have shown interest in these two scientific projects.
Dutch researchers are busy testing their lignin-based bioasphalt, and expect to be able to improve functional properties of their asphalt, including its rolling resistance, and making road running surfaces quieter.
As part of that, they hope to have a section of road and/or a parking area paved with their lignin bioasphalt this year, so they can enlarge their testing program.
Liquid AC has been an excellent product, used by road builders and in the production of roofing felt, and for sealing flat or low-slope roofs. But it is obtained from the distillation of crude oil, a process that releases a lot of carbon dioxide, a greenhouse gas. If we're to make the transition to a low-carbon economy, we'll need to have access to not only biofuels, but bioasphalts as well. The work of these teams in France and Holland will be closely watched.
To Read more: http://journalofcommerce.com
Advancements in self-consolidating concrete
by Robert Quattrociocchi
Self-consolidating concrete (SCC) is a revolutionary building material that is widely regarded as one of the most significant technological advancements in the concrete industry in years. Its inherent fresh properties and ability to flow under its own weight opens the door to countless opportunities that would not be possible with conventional concrete.
In spite of this, there has been a significant lag between the development of the technology and full scale acceptance and use. While there is always a period of adjustment prior to the adoption of any new innovation, the cast-in-place concrete construction industry as a whole has traditionally been slower than most to embrace new methodologies. For example, a large percentage of precast concrete is manufactured today using SCC technology.
An increasing number of specifiers and contractors alike are starting to see the real benefits offered by SCC, but there is still a reticence to fully accept this technology by a large segment of the cast-in-place industry. The main reasons for this are the consistency of the product, cost of the material, and concerns with formwork pressure.
SCC can best be described as "…highly flowable, non-segregating concrete that can spread into place, fill the formwork, and encapsulate the reinforcement without any mechanical consolidation" (ACI 237-07 Self-Consolidating Concrete). Its origin dates back to the late 1980s in Japan in response to a lack of labour skilled in the proper techniques of concrete consolidation.
SCC is essentially an extension of traditional concrete technology, offering similar or improved engineering properties while providing enhanced plastic performance. In order to achieve its fresh performance characteristics (including filling ability, passing ability and stability) and flow-ability, a much larger cementitious component (Portland cement and supplementary cementing materials) is required to generate increased paste content. In addition, the water to cementitious materials ratio (w/cm) of these mixtures tends to be low, necessitating a greater dosage of polycarboxylate-based high range water reducing admixtures (HRWRA) to achieve fluidity or workability. In some instances, inert mineral fillers, such as limestone powder, and viscosity modifying admixtures (VMA) are used to increase the stability of the mix or resistance to segregation.
It is important to first understand that SCC is not a 'one size fits all' proposition. SCC mixture constituents and proportions will vary from one mix to another depending on the project requirements, type of application and placement technique. There is a range of plastic performance levels that exist with SCC so it is therefore essential to determine the appropriate targets for the project and design accordingly. For example, SCC used for a relatively open pour with minimal reinforcement can be designed with flow-ability on the lower end of the spectrum. Conversely, if placing concrete in a complex shape with intricate formwork, then flow-ability becomes critical to the design to ensure complete filling. Communicating the project requirements and logistics of placement to the ready-mixed producer well in advance is crucial to developing and proportioning the mix appropriately.
The true value of SCC is relative to what practices or methods are currently being used. Therefore, this would vary from project to project. However, the following is a general list of the benefits that can be realized when using SCC:
- Ease of placement and consolidation into heavily congested or tight formwork
- Improved surface finish, specifically for architectural elements
- Reduction of remedial patching work
- Cost savings due to reduction in labour crew needed to place and consolidate concrete
- Reduction in noise levels due to elimination of mechanical vibration
- Improved safety as a result of reduced labour, equipment and noise levels during concreting operations
- Speed of construction, as SCC can be placed at higher rates than conventional concrete.
It should be noted that there is an increasing trend in the design community to push the envelope by incorporating features into structures that have intricate shapes and complex geometry. In many cases, the construction of these elements would not be achievable using conventional concrete and traditional placement techniques. The true benefit in these cases is that the available technology allows the designer the freedom to create and innovate.
One of the main obstacles to more widespread use and acceptance of this technology across the industry is the producer's ability to consistently provide high quality SCC. This concrete is a very different animal to tame, as it is highly sensitive to material variations and requires an increased level of quality control. A slight increase in aggregate moisture content, for example, can transform a robust SCC mix into one with less stability that is prone to segregation. A higher level of understanding in regards to material selection and proportioning is needed than for conventional concrete. Thus, a greater commitment is required from the producer to increase resources in areas such as quality control, training, mixture development, equipment and batching/delivery logistics.
The higher per unit volume cost of SCC compared to conventional concrete is often cited as an argument against its use. While the cost of SCC will vary from market to market, it is generally significantly more than conventional concrete due to the increased material component (cementitious and admixtures) and level of attention required. However, when compared to other high-performance mixtures, such as high strength concrete, the gap closes significantly. In these cases it is important to consider the total in-place cost and not solely that of the concrete. It often becomes difficult to justify the use of SCC in lower compressive strength applications due to the significant cost premium. One approach to dealing with this is to replace a portion of the cementitious component with inert mineral fillers, a practice widely used in Europe. This acts to effectively reduce the upfront cost of the SCC while not sacrificing the paste content.
The design codes and standards currently dictate that, due to the fluidity of these mixtures, formwork used in SCC applications must be designed to withstand full hydrostatic pressure. This approach leads to increased formwork costs and creates another roadblock to more widespread use of the product. Presently, there are a number of research groups around the world investigating the effects of SCC on formwork pressure. Early indications are that the current design requirements are over-conservative, good news for proponents of this technology.
To Read more: https://www.reminetwork.com
In the Heart of the Mountain
A record-breaking train tunnel could provide a badly needed shortcut through the Swiss Alps
The sky is still black over the Swiss Alps as we climb aboard a train one morning in late March and head inside the mountains. In an instant, the sharp alpine air thickens to a torpid heat reaching nearly 40°C. The temperature rise is a function of geology, not meteorology we are deep inside solid rock, in the 57-km-long Gotthard Base Tunnel. More than 1,800 m of mountain is piled above our heads. "This is extremely high-pressure rock and the water pressure is also very high," says Renzo Simoni, a Swiss civil engineer and CEO of AlpTransit Gotthard AG, the company that is overseeing one of the world's most ambitious engineering projects, as he guides us along a dark tunnel track. "Working in these conditions is very, very hard."
Indeed building the Gotthard Base Tunnel has taken decades of backbreaking toil by more than 2,600 people, at a cost of more than $10 billion. But after 23 years of work, the result is spectacular. When it finally opens in June next year, the tunnel will be the longest in the world, longer than the Seikan Tunnel in northern Japan and the Channel Tunnel connecting England and France.
But it's not just length that sets Gotthard apart. Unlike those two, which partly travel under water, the Swiss tunnel required drilling through exceedingly hard granite and quartz, under the Gotthard massif in the Alps. Thanks to the 800-m-deep shafts needed to pump in air and drop millions of tons of cement for the tunnel walls and floors, the Gotthard Base Tunnel will not only be the world's longest but will also have what Simoni believes is the world's most powerful ventilation system. In order to bore a total of 152 km of tunnels, shafts and passages (there are twin, parallel rail tunnels, one for each direction), the workers cut through 13 million cu m of rock, the volume of nearly nine Empire State Buildings.
An Engineering Dream
All this would have been essentially impossible until the recent development of high-precision boring machines capable of digging a tunnel this long. With shafts nearly a kilometer long, engineers needed satellites to map out the entire route; an error of even a few millimeters would mean redoing entire parts of the tunnel. For environmental reasons, the concrete for the tunnel walls came from the rock the workers excavated, rather than from riverbeds, as is often the case with tunnel building. That meant developing entirely new plastic compounds to seal the walls against possible leaks. "This is completely different," Simoni said. "This had never been done before."
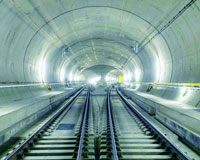 |
But while the technology to build an epic Alps tunnel is new, the dream isn't. In 1947 the Swiss engineer Carl Eduard Gruner fancifully suggested tunneling through the Alps between the northern city of Basel to Chiasso on Switzerland's southern border with Italy a distance of some 285 km because the cars snaking bumper to bumper over the twisting mountain passes were threatening to turn the bucolic slopes into an endless traffic jam. Nearly seven decades after Gruner first floated his idea, the traffic in the
|
Swiss Alps is as much a problem as ever. The original Gotthard rail tunnel, about an hour's drive south of Zurich, is still used, but it was built in the horse-and-buggy era in 1882, is only 15 km long and is too steep and twisting for long modern freight trains to use.
As the container ships that carry international cargo have grown bigger, the container-truck traffic that bears that freight from port to final destination has become heavier. About 1.2 million container trucks barrel through the Swiss Alps every year, leaving politicians and regular citizens wondering whether clouds of diesel fumes might one day choke their country's iconic landscape. "The Alps are extremely important to the image of Switzerland," says Manuel Herrmann, head of transport policy at Alpine Initiatives, an organization set up in 1989 to push the government to restrict truck traffic across the mountains. Herrmann claims the air pollution and noise in the Swiss Alps' five valleys is now comparable to cities like Paris. That's more than an environmental danger it's a cultural threat to a country whose traditions are rooted in the ideal of clean mountain living. The tunnel opening in Erstfeld is close to the mountain village where William Tell shot an apple off his son's head with a crossbow, or so the famous legend goes. "You think of Switzerland, you think of the mountains," says Herrmann.
To Read More: http://time.com