Green Formwork System
Achievement of a sustainable formwork system could lead for more sustainable construction and enhance the construction industry sector to uphold
sustainability for future generations.
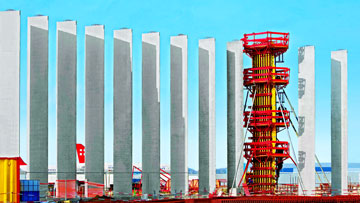
|
Sustainability indicators to formwork system can be divided into based on economical, social, and environmental aspects. |
The word of sustainability is defined by the capability to maintain sustainable development, sustainable construction, sustainable building and sustainable material which are strongly dependent on ecological, social or economical perspectives. Some of sustainability criteria that are applicable to resource development activities include increased recycling, minimal use of non-renewable resources, exploiting renewable resources at a rate less than their natural rate of ecologically safe regeneration such as timber, reducing waste-generation levels to well within the assimilative capacity of the environment, repetitive uses of material resources and ensuring maximum resource use efficiency in development processes. It is the goal of the sustainability to reduce the use of resources and work towards the ultimate goal for sustainable construction.
As the premier construction material across the world concrete is versatile and economical material available to the construction industry and its use can have many environmental effects. Meanwhile; the formwork system is a very important element in concreting works as it has significant role in the construction process. In constructing conventional reinforced concrete building, it will involve largest portion of formwork. It accounts for 35 to 60 percent of the cost of the concrete work. With the uses of sustainable formwork system, it will create sustainable development criteria that will help to reduce wastages in the construction by minimizing the usage of conventional materials.
Formwork is an essential part of concrete construction as it provides the mould in which an element is cast. Owing to the relatively high cost of formwork, it is a standard practice to maximise re-use. Formwork type will affect the potential for re-use. Metal forms made from steel, for example, may be used hundreds of times.
Traditional timber formwork is built on site out of timber and plywood or moisture-resistant particleboard. Although it is easy to produce, it comes with a set of drawbacks involving more time and a short lifespan. The formwork which is made of wood or timber may have to be replaced after a few uses. However, it is still used extensively where the labour costs are lower than the costs for procuring reusable formwork. As compared to traditional timber formwork, formwork systems are grouped under cast in-situ construction method. Moreover, the unskilled worker can be easily trained to construct building using the formwork system.
Formwork and Sustainability
Formwork system referred to the total system of support for freshly placed concrete including the mold or sheathing which contacts the concrete as well as supporting members, hardware, and necessary bracing. Achievement of a sustainable formwork system could lead for more sustainable construction and enhance the construction industry sector to uphold sustainability for future generations. Formwork system could be classified according to its purpose to mould concrete members such as slabs and beams, walls and columns. There are many types of formwork system according to its method of erection and the materials that have been used. Traditional formwork system which uses timber as the main material is the most common and widely used in building construction. This traditional formwork system involves disadvantages such as labour intensiveness, long cycle period and mass of wastes.
There are few sustainable formwork systems that are developed from various materials with the different method of installation with an intention to achieve sustainable construction. Sustainability indicators to formwork system can be divided into based on economical, social, and environmental aspects.
- Waste generation
- Energy & resource consumption
- Using renewable material
- Structural operation
- Formwork reusable
- Material efficiency
- produce healthy indoor environment
- material efficiency
New concrete formwork systems are recently developed from different materials with various methods of installation with intention to achieve sustainable construction. These sustainable formwork includes; Insulated Concrete Formwork, Plastic Formwork System, Aluminium Formwork System, and Tunnel System. Besides improving the speed the construction of buildings, repeatable, long-life uses and can lower the construction cost.
Insulated Concrete Formwork
Insulated Concrete Forms (ICFs) are formwork for concrete that stays in place as permanent building insulation for energy-efficient, cast-in-place, reinforced concrete walls, floors, and roofs. The forms are interlocking modular units that are dry-stacked (without mortar) and filled with concrete.
Concrete is pumped into the cavity to form the structural element of the walls. Usually reinforcing steel is added before concrete placement to give the resulting walls flexural strength, similar to bridges and high-rise buildings made of concrete.
ICFs are hollow 'blocks' or 'panels' made of expanded polystyrene insulation (EPS) or other insulating foam that builders stack to form the shape of the walls of a building (like Lego bricks) to create a cavity, or mould for the structural walls of a building. Concrete is then pumped into the cavity to form the structural element of the walls. Usually, reinforcing steel (rebar) is added before concrete placement to give the resulting walls flexural strength, as in bridges and high-rise buildings made of concrete. The forms stay in place as a permanent part of the wall assembly. Therefore, the structure is basically a sandwich consisting of a heavy, high-strength material (reinforced concrete) between two layers of a light, highly insulated material. This combination creates a wall with many desirable properties which are air tightness, strength, sound attenuation, insulation and mass.
This method has several advantages compared to traditional building materials, especially in residential and light commercial construction. The advantages of structures built with this method include concrete construction naturally has a high thermal mass, which is the ability of a material to store excess heat energy during the day. This heat energy is then released back into the building at night as it begins to cool. Apart of that, an ICF building is built to last where concrete is inherently durable, and when cast within the ICF system, it cures without suffering exposure to extreme temperature variances.
Plastic Formwork System
These interlocking and modular systems are used to build widely variable, but relatively simple, concrete structures. The panels are lightweight and very robust. They are especially suited for low-cost, mass housing schemes. The applications of plastic formwork do not require skilled labour, thus it will reduce the labour cost. The plastic formwork components that are required to assemble a building mould are joined to form wall configurations of any desired length and height which can be altered and expanded as well. The lightweight structure can easily be handled and transported.
Aluminium Formwork System
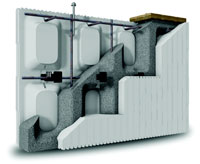 |
The Aluminium Formwork System for concreting is probably the most versatile modern construction system. Unlike other systems it is equally suited to both high and low-rise constructions. Specifically designed to allow the rapid construction of multiple unit projects at optimum productivity, the aluminium formwork can be used for a broad range of applications, |
from straightforward panels to more complicated structures involving bay windows, balcony and stairs.
System Column Formwork
The column formwork systems now available are normally modular in nature and allow quick assembly and erection on-site while minimising labour and crane time. They are available in steel, aluminium and even cardboard and have a variety of internal face surfaces depending on the concrete finish required. Innovations have led to adjustable, reusable column forms which can be clamped on-site to give different column sizes. The basic construction is achieved when the column forms are assembled and positioned over or enclosing the reinforcing bar cage. The forms are positively restrained and braced using props and concrete is poured.
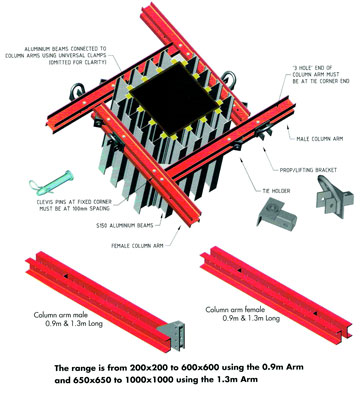 |
Innovations have led to adjustable, reusable column forms which can be clamped on-site to give different column sizes. The basic construction is achieved when the column forms are assembled and positioned over or enclosing the reinforcing bar cage. |
Once the concrete has hardened sufficiently the formwork is stripped and moved to the next position manually or by crane. Disposable forms may be left in place for an extended period to aid curing and strength gain of the concrete before removal.
- Sustainability Features
- The metal column forms are easy to clean and reuse with little waste generated compared to traditional formwork.
- The highly engineered nature of the metal formwork allows site teams to control operations in a better manner which in turn can lead to reduced concrete wastage.
- Disposable forms that are stripped and discarded after one use can often be recycled.
Lightweight Modular Systems
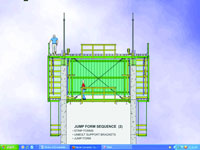 |
Innovation in formwork has led to small lightweight modular systems that provide versatile formwork solutions on-site. Use of aluminium, high tensile steel, fibre glass, special plastics, etc. for different components has enabled lightweight units to be developed which can be safely manhandled to achieve a practical formwork system. |
Lightweight formwork systems used for slab construction generally consist of a series of interconnected false work bays, independent props or system scaffolds and supporting pre-formed decking panels. These can include primary beams spanning between props and supporting a number of panels.
- Sustainability Features
- The formwork system is easy to clean and reuse with little waste generated compared to traditional formwork.
- The components can be moved quickly around the site.
- The individual system components such as props can be used for other purposes. This mobility and their modularity enable materials to be kept to a minimum on-site.
- Lightweight form systems can be very cost effective for certain types of structure.
- The highly engineered nature of the metal formwork allows site teams to control operations in a better manner which in turn can lead to reduced concrete wastage.
Vertical Panel System
Crane-lifted panel systems are commonly used on building sites to form vertical elements and usually consist of a steel frame with plywood, steel, plastic or composite facing material. The systems are normally modular in nature, assembly times and labour costs are considerably lower than traditional formwork methods with far fewer components required. They offer greater opportunities for reuse for different applications on site.
- Sustainability Features
- The forms are easy to clean and reuse repeatedly.
- Less waste is generated compared to traditional formwork.
Jump Form
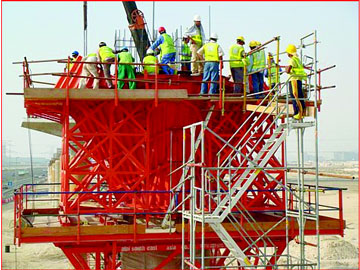
|
Traditional timber formwork is built on site out of timber and plywood or moisture-resistant particleboard. Although it is easy to produce, it comes with a set of drawbacks involving more time and a short lifespan. |
Generally, jump form systems comprise the formwork and working platforms for cleaning or fixing of the formwork, steel fixing and concreting. The formwork supports itself on the concrete cast earlier so does not rely on support or access from other parts of the building or permanent works. Jump form, here taken to include systems often described as climbing form, is suitable for construction of multi-storey vertical concrete elements in high-rise structures, such as shear walls, core walls, lift shafts, stair shafts and bridge pylons. These are constructed in a staged process. It is a highly productive system designed to increase speed and efficiency while minimising labour and crane time.
- Sustainability Features
- The formwork system is easy to clean and reuse with little formwork waste generated compared to traditional formwork.
- Climbing formwork systems offer simplicity, safety and cost effectiveness for certain high-rise building structures.
- The repetitive nature of the work, combined with the engineered nature of the formwork, allows fine tuning of the construction operations, which in turn leads to minimal concrete wastage.
- Many repeated uses of formwork are possible before maintenance or replacement is needed, the number of uses depending on the quality of the surface finish of concrete specified.
Tunnel Formwork System
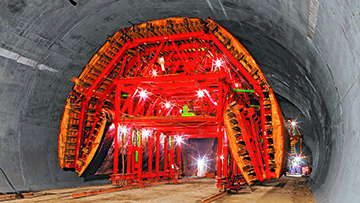
|
The environmental benefits of permanent formwork, which remains in place after concrete casting and can improve thermal insulation, should be considered as part of a concrete system. |
Tunnel Formwork System had been used in replacement of conventional timber formwork. Since then, the tunnel formwork technology has gained tremendous popularity and acceptance by many contractors, consultants and owners as the most suitable construction method to build apartments with large quantities and within limited time frame. It can also be used to cast double-storey’s terrace units and high end condominium.
This formwork system allows the contractor to cast walls and slabs in one operation on a daily cycle. It combines the speed, quality and accuracy of factory or off-site production with the flexibility and economy of in-situ construction and is recognised as a Modern Method of Construction (MMC). Its advantages over the traditional construction method include, low skill requirement, speedy construction, low maintenance, durable structure and less cost.
- Sustainability Features:
- The formwork system is easy to clean and reuse with little waste generated compared to traditional formwork.
- Tunnel form systems can be very cost effective for certain types of structure.
- The repetitive nature of the work, combined with the engineered formwork, allows site teams to finely tune their operations, which leads to minimal concrete wastage
Conclusion
Different formwork systems provide a wide range of concrete construction solutions that can be chosen to suit the needs of a particular development. Traditional formwork for concrete construction normally consisted of bespoke solutions requiring skilled craftsmen. This type of formwork often had poor safety features and gave slow rates of construction on-site and huge levels of waste – inefficient and unsustainable. In comparison, plywood may be cheap to buy, but can only be used as quality formwork a few times. However, all types of formwork can be recycled or used for secondary purposes. The environmental benefits of permanent formwork, which remains in place after concrete casting and can improve thermal insulation, should be considered as part of a concrete system.
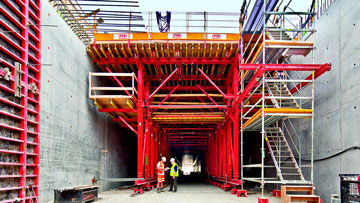 |
The type of timber and whether it is from a managed forest and sustainable resource are also important environmental considerations. Modern formwork systems are extremely efficient, and the impact of formwork on the environment is small compared with that of concrete.
Modern formwork systems, which are mostly modular, are designed for speed and efficiency. They are engineered to provide increased accuracy and minimize waste in construction and most have enhanced health and safety features built-in. The main systems in use are table form/flying form, system column formwork, horizontal and vertical panel systems, jump form, slip form and tunnel form. This guide sets out their key features – process efficiency, safety, sustainability and other considerations – in order to help construction professionals to take advantage of them to achieve modern, efficient concrete construction.
References:
http://www.concrete.org.uk/fingertips-nuggets.asp?cmd=display&id=199
http://www.efka.utm.my/thesis/IMAGES/3PSM/2010/JSB-P1/surianiaa060207d10ttt.pdf
http://kentechnology.no-ip.org/VCE/resources/PDF/Formwork/Formwork%20construction.pdf