INCREASING THE DURABILITY OF REINFORCED CONCRETE STRUCTURES
Abstract
Durability of concrete is defined as the capability of the concrete by means of which a structure is built to endure various circumstances including non-friendly environments.
Keywords
Durability, Portland cement, Blended cement, Corrosion, Protective coatings
Introduction
If a high rise building, a long flyover or an underground tunnel, all made of reinforced concrete can sustain their structural stability and architectural renderings for a long period, for example, for more than two hundred years, they can be declared as sound and durable structures.
Structures can be classified in two groups.
- Structures whose longevity has no limit
Bridges can be designed for loads which can be predicted for life time. The underground construction of large dams and other marine structures whose reconstruction and modification are not only difficult but cumbersome could also be in this group.
- Structures whose life time can be predetermined for 30 to 40 years or more
Industrial and coastal structures which are prone to adverse environmental damage may be included in this group.
Selection of building materials
Cement and steel are the main items among all the building materials to build a durable reinforced concrete structure. The type of cement, fine aggregates (sand) and coarse aggregates and admixtures have great influence on the density of concrete and so on durability. A compatible grade of steel should be chosen as reinforcement for a particular grade of concrete. The reinforcement bar is a vital item for a reinforced concrete structure to sustain the imposed load for its life time. Steel is found to be an appropriate material for reinforcement bar due to its high flexural strength besides other characteristics such as elasticity, ductility, malleability and cost. The only disadvantage is that it cannot resist corrosion. Thermo-Mechanically Treated (TMT) bars have been developed as per latest technology. These are the high strength reinforcement bars whose corrosion resistance is very high. Besides, TMT bars have better weldabilty than the normal steel bars without any loss of strength.
Cement for the concrete
The durability of a concrete structure is ensured by the resistance to deterioration of concrete and the corrosion of steel reinforcement. Such resistance is specially needed for the industrial, marine and coastal structures where the external environment surrounding the concrete structure is highly corrosive. It is a serious concern to the builders that the continued corrosive attack on reinforcement bars from external environment causes serious structural damage, affecting the safety of the structure resulting in a catastrophic failure.
Constituents of ordinary Portland cement(approximate)
- lime 64%
- silica 23%
- alumina 5%
- iron oxide 1-3%
- magnesia 0.1-3%
- others(sulphur trioxide, potash) 1%
When water is mixed to the cement, hydration starts with the liberation of calcium hydroxide. The acidity or alkaline character of a liquid can be ascertained from its pH value which is logarithm exponent with respect to base 10. Considering drinking water having pH 7, a liquid of pH less than 7 is acidic. The hardened concrete formed through a continuous process of hydration, behaves as alkaline when the pH level of the pore moisture exceeds 11.5 or so due to the presence of calcium hydroxide. In such a state, steel reinforcement can be regarded as protected against corrosion by the formation of a passivating iron oxide film (Fe2O3) around the steel surface. The protective film results in complete inhibition of corrosion formation through the following reaction:
The protective film of iron oxide maintains the passive state of the reinforcement bar as long as pH of hardened concrete does not fall below 11.5. The damage of this protected film commences once the pH value is reduced by the intrusion of mineral salt into the concrete or by the effect of leaching or carbonation action or through the permeation of chloride or other contaminants into the hardened concrete. Due to such reduction of pH value, passivity of the steel surface against corrosion is lost. So appropriate measures need to be taken to prevent or at least to minimise to the extent possible the attack of chloride or carbonation or the ingress of salt and other contaminants into the concrete.
Blended cement
This cement is preferred than other cement to give a long life to concrete structures due to the reasons to be described later. Blended cement reacts with water in primary and secondary ways:
Primary Reaction
2C3S + 6H2O -> C3S2H + 3Ca(OH)2
2C2S + 4H2O -> C3S2H3 + Ca(OH)2
Secondary Reaction
Pozzolana + 3Ca(OH)2 -> C3S2H3
In case of Ordinary Portland Cement only the primary reaction takes place which liberates calcium hydroxide or lime. Since the liberated lime is weak against the attack of chemicals such as sulphates, it leads to expansion of concrete followed by cracks and so durability is reduced. But a pozzolanic material goes in for a secondary reaction combining with lime resulting in formation of denser gel structure of concrete of higher ultimate strength resulting in longer durability.
Advantages of blended cement
- It improves the impermeability of concrete.
- It offers resistance to attack by chemical agents containing sulphates as in groundwater, soils, coastal and marine environments.
- It reduces the heat of hydration and so can be effectively used in mass concreting works, for example, concreting in dams, barrages and deep foundations.
Choice of aggregates for the concrete
Fine and coarse aggregates and admixtures have great influence on the density of concrete. Since density is an important yard stick for durability, these materials are to be selected judiciously. Contamination in aggregates may aggravate the electrochemical action on the concrete resulting in the corrosion of steel reinforcements.
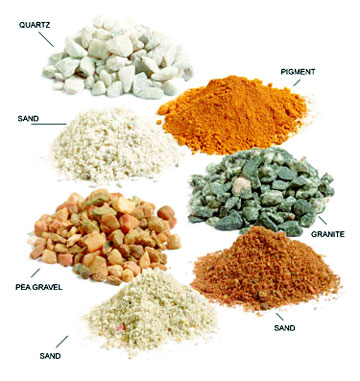 |
Aggregates for the Concrete |
Factors influencing corrosion
When the concrete structures are either constantly in dry condition or are constantly saturated with water, corrosion of reinforcement bars hardly occur. When there is variation of moisture in concrete, corrosion develops at a rate whose value depend on physical and chemical factors.
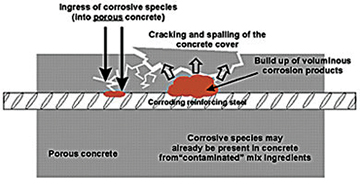 |
Factors influencing corrosion |
Physical factors
Considering the selection of building materials as one of the physical factors, other aspects influencing the development of corrosion rate are the following:
Thickness of permeability of the protective concrete cover.
Concrete is the primary barrier to safeguard reinforcement bar against corrosion. Attempts should be made to make the concrete more dense and sound by eliminating pores and voids by proper vibration and compression so as to improve the impermeability. The increase in barrier thickness is also necessary to lengthen the diffusion path of aggressive gases or electrolytes to reach the reinforcement area. The electrolytes are the result of electro-chemical potential which is an index of the resistance to transition of electrical charge from steel into the pore moisture of the concrete.
Proportion of mix
The concrete having a high water / cement ratio may not be an ideal for high density concrete. So far durability is concerned, water /cement ratio is to be kept low in the tune of 0.32 or so with the cone of slump not exceeding 0.25 mm. This will minimise the porosity to a great extent. Aggregate / cement ratio is to be maintained constant by increasing the volume of coarse aggregate at the cost of the fine aggregate. This is necessary to improve the workability with minimum voids.
Vibration and Compaction
Poor compaction leads to large voids particularly adjacent to reinforcements through which moisture and salt can be deposited. Monitoring is needed as to whether there are mistakes in batching, mixing and consistency during the process of compaction to obtain a durable concrete. The heap of concrete deposited in one part of the formwork breaks after vibrator is applied. The mortar tends to flow away between the coarse aggregate at the bottom leaving the upper layer stony and honey-combed the effect can be eliminated to a great extent if sufficient number of vibrators are used to bring about uniform compaction throughout the volume under the process of compaction.
Curing
Permeability of hardened concrete can be considerably reduced by increasing the period of hydration of cement by moist curing. All cracks, whether transverse or longitudinal, increase the risk of corrosion of reinforcement.
Chemical factors
Chloride attack
Chloride may be present in the composition of binder, aggregates and the mixing water. It is also present in the additives and the accelerating agents. When the amount of chloride in the liquid state exceeds the critical value, the pH value is reduced resulting in the loss of alkaline character of concrete promoting de-passivation of steel leading to corrosion.
Carbonation of concrete
Carbonationis the result of chemical reaction of alkali constituents of concrete with carbon dioxide leading to formation of carbonates. Carbon dioxide presents in the atmosphere under natural conditions at 0.03% by volume diffuses by penetration through the surface of the concrete into the pore structure filled with air transformed partly into carbonic acid. The rate of carbonation increases with the increase of temperature. The increase of carbonation depth over time is determined by the porous structure of concrete, especially the proportion of capillary pores and the ability to combine with carbon dioxide i.e. mainly by the amount of calcium hydroxide entering the system. The passivating effect of concrete remains stable so long the surface of steel reinforcement is covered by alkaline concrete. When the alkaline level falls due to carbonation process, de-passivation character of steel develops and corrosion starts.
Protective coatings to control corrosion
Coating the reinforcement bar is an effective method of decreasing the corrosion of steel. Both metallic and nonmetallic coatings can be used. But before selecting the same, it has to be seen as to whether it can resist the alkali and chloride, whether it can sustain the bondingbetween concrete and steel, whether it has good abrasion resistance, whether it has good bend ability, whether it has good impact resistance, whether it is easy to apply and whether is economical.
Non-metallic coatings
Cement concrete coverings of new structures represent a part of the two or more stage of construction process. The coating may be applied before the main concrete is hardened or a few days later. In the second case, a binding layer is needed in between. Though the first option accounts for economy of time and resources but the second option ensures a protective layer for durable concrete.
Inhibited cement slurry coating
This is a passivating cum barrier type of cement slurry coating, which is applied on degusted and phosphate steel bar surface. A top sealing coat over the slurry coating can be applied for sealing the pores and making the coating harder and less permeable.
Silicate coating
Inorganic alkali silicate coating is applied for reinforcement bar protection. This consist of mixtures of inorganic alkali silicate and other linking compounds deposited in a sand-blasted bar.
Zone-coating
In recent times, zone-coatinghas gained importance for protecting corrosion. Hot dip galvanising process is the second most widely used method for protecting corrosion of steel reinforcement.
Conclusion
Reinforced concrete structures are beyond repair when they have deteriorated due to corrosion of steel reinforcements. Qualified engineers entrusted for a concrete project should impart their theoretical and practical knowledge so as to highlight and rectify the mistakes done by the construction personnel at different stages of construction right from detailing and laying of reinforcements, method of batching and mixing concrete, placing, vibrating, compacting and finally curing the hardened concrete. If all these are ensured, building pore-free, void-free and honey-comb free durable and sound sustainable concrete structures would be possible.
Authors
Dr. Amartya Kumar Bhattacharya
BCE (Hons.) ( Jadavpur ), MTech ( Civil ) ( IIT Kharagpur ), PhD ( Civil ) ( IIT Kharagpur ), Cert.MTERM ( AIT Bangkok ), CEng(I), FIE, FACCE(I), FISH, FIWRS, FIPHE, FIAH, FAE, MIGS, MIGS - Kolkata Chapter, MIGS - Chennai Chapter, MISTE, MAHI, MISCA, MIAHS, MISTAM, MNSFMFP, MIIBE, MICI, MIEES, MITP, MISRS, MISRMTT, MAGGS, MMBSI
Chairman, MultiSpectra Consultants, 23, Biplabi Ambika Chakraborty Sarani, Kolkata - 700029, West Bengal, INDIA. E-mail : dramartyakumar@gmail.com
Akshat Chandanam, Akshay Thakur, Rahul Meena
Undergraduates, Department of Civil Engineering, Indian Institute of Technology Kharagpur - 721302, West Bengal, INDIA.
E-mail : akshatchandanan@gmail.com, akshay.thakur@outlook.com, merahul68@gmail.com