An Epitome of Luxury and Perfection
Marina Bay Sands, Singapore
The Marina Bay Sands resort in Singapore is one of the most ambitiously built structures, highly focused on business class. It is to be the leading business, leisure and entertainment spot to spend quality of time with family and business sector wings. Marina Bay Sands is a $5 billion project, high-density, mixed-use integrated resort that brings together a 2,560-room hotel, convention centre, shopping and dining, theatres, museum and a casino across the water from Singapore's Central Business District. It was designed by Moshe Safdie, Boston-based internationally renowned architect. It anchors 929,000 sq mt (10 million square-foot) the Singapore waterfront; a gateway to Singapore and provides a dynamic setting for a vibrant public life.
Architecture and Design Significance
Moshe Safdie was invited to join the Las Vegas Sands Corporation in developing a competitive design proposal for Marina Bay for submission to the Government of Singapore. "Marina Bay Sands is really more than a building project, it is a microcosm of a city rooted in Singapore's culture, climate, and contemporary life," says architect Moshe Safdie. "Our challenge was to create a vital public place at the district-urban scale, in other words, to address the issue of mega scale and invent an urban landscape that would work at the human scale."
Located along the network of public paths also include two theatres with a combined 4,000 seats, a casino, a 9,000 square meter (96,000 square-foot) convention and exhibition centre and a hydraulically adjustable public event piazza of 5,000 square meters (54,000 square feet). Combining indoor and outdoor spaces and providing a platform for a wide array of activities, 21st-century cardo maximus or grand arcade also connects to the subway and other transportation. A series of layered gardens provide ample green space throughout Marina Bay Sands, extending the tropical garden landscape from Marina City Park towards the Bay front.
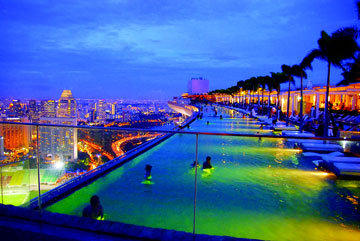 |
An engineering marvel 200 meters (656 feet) above the sea, the SkyPark spans from tower to tower and cantilevers 65 meters (213 feet) beyond. It accommodates a public observatory, gardens, a 151 meter-long (495 foot-long) swimming pool, restaurants and jogging paths and offers sweeping panoramic views; a formidable resource in a dense city like Singapore. Shielded from the winds and lavishly planted with hundreds of trees, the SkyPark celebrates the notion of the Garden City that has been the underpinning of Singapore's urban design strategy.
Moshe Safdie selected five international artists to create eight monumental public art installations for Marina Bay Sands (James Carpenter, Antony Gormley, Ned Kahn, Sol LeWitt, and Chongbin Zheng). The artists worked closely with Safdie to ensure that the site-specific commissions complement the architecture and energize the public spaces.
A Note on Architect
Moshe Safdie was born in Haifa, Israel, in 1938, Moshe Safdie moved to Canada with his family in 1953. He graduated from McGill University in 1961 with a degree in architecture. After apprenticing with Louis I. Kahn in Philadelphia, Safdie returned to Montreal to oversee the master plan for the 1967 World Exhibition. In 1964 he established his own firm to realize Habitat '67, an adaptation of his thesis at McGill, which was the central feature of the World's Fair and a groundbreaking design in the history of architecture. He also the founder of Safdie architects.
Other Supportive Wings
The artists worked closely with Safdie to ensure the site-specific commissions complement the architecture and energize the public spaces. The artists who created works for Marina Bay Sands are: Antony Gormley , Drift, Chongbin Zheng, Rising Forest, James Carpenter, Blue Reflection Facade with Light Entry Passage, Ned Kahn, Wind Arbor, Rain Oculus and Tipping Wall. Inspired by great ancient cities that were ordered around a vital public thoroughfare, Marina Bay Sands is organized around two principal axes that traverse the district and give it a sense of orientation placing emphasis on the pedestrian street as the focus of civic life.
All in all, the large art installations complement and integrate well with the architecture and the surrounding environment. Despite the few months of operation, Marina Bay Sands is a building project which has created its own microcosm of a city within the development. Marina Bay Sands seems to make a bold statement in Singapore's culture and contemporary life. Furthermore, it is surely an architectural and structural engineering achievement which sets the bar high as it brings pioneering techniques for the engineering sector. Each of these strategies presented a series of structural, mechanical, and construction logistics challenges of the highest order.
Silver Coat Facade
Arup's facade team covered the entire development, ranging over several zones with multiple types of facade. It subsequently provided engineered design intent drawings and performance specifications for a design. The facades were grouped into main broad packages; the hotel towers, the podium structures, the ArtScience Museum and the Crystal Pavilions. Common issues Architectural intent Safdie Architects had a clear vision for the form and appearance of MBS and the facades were a critical aspect of the vision. To enable the views, high light transmission was needed with avoidance of tinted glass so as to give good colour rendition. It resulted in less area for insulation which coupled with the use of clear glass and implies the consumption of greater amounts of energy. There was also consideration to be met about night-time views in these areas, especially concerning the rooms at the Sands Hotel.
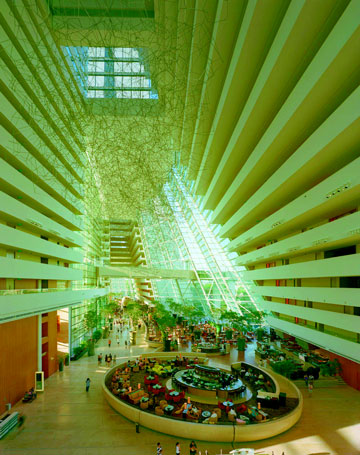 |
Energy performance Singapore has strict requirements on the amount of solar and ambient energy flowing into a building. Hotel glass curtain walls and glass fin design. The west-facing orientation of the hotel towers created an issue of thermal comfort during afternoons. Safdie Architects' design incorporated vertical glass fins to express the building shape and complex curvature of the towers with preference for frameless glass with exposed edges.
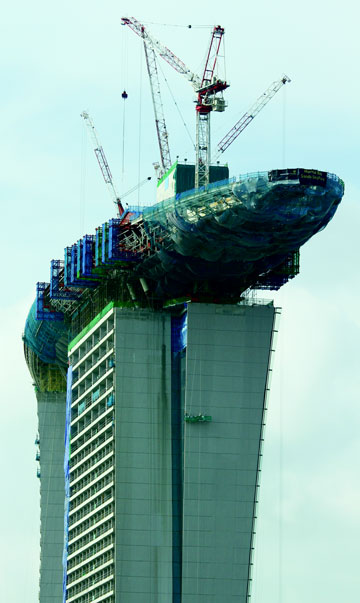 |
Secondly, highly transparent glass was specified. The area was given priority for the use of low iron glass that increased visible light transmission even though it meant a lower thermal insulation performance. To compensate, the double-glazing used in other areas of the podium has less transparency and better thermal performance. In developing such a highly transparent structure the first objective was to use the largest spacing between supports: glass sheets 2.6m high x 3.7m wide with supports only along the horizontal edges. Small transoms were used to take the load to the major steel vertical elements at the ends of the glass panels.
Podium
Design of the podium roofs have highly complex geometries; the fundamental elements of their form and shape being based on Euclidean geometry, such as how arcs are derived from toroidal surfaces. The architect cleverly pushed and pulled these seemingly independent geometries together into an overall form that appears to be vastly more complex than the sum of its original components. The concept of using developable geometry was very important to the design team not only for enhancing understanding of the structure but also to help its constructability. Supporting the greatest surface area of each of the three roof structures is a spine truss, curved in elevation and in plan.
A Major Challenge to the Structural and Architectural team
Working together was that the entire concept (including its presentation) occurred within four months. This was the result of the client LVS decided to turn to Safdie Architects only four months before the submission deadline. Since it can be seen that the concept as presented and selected by the Singapore government was almost identical with what was built four years later, the initial concept held up to the test of later development. Indeed it was the Arup team's work with our team in Bostonwith the support of Aedas, the client's design and construction team, over four months that became reality four years later.
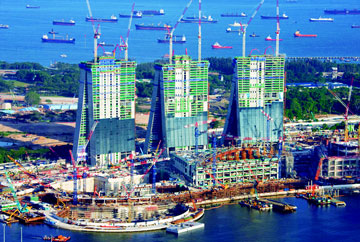 |
Given the four-year schedule for design and construction, formidable organisational moves occurred. The team expanded exponentially to embrace Aedas and Arup offices across the globe including those in the region, as well as engineering teams in the other disciplines and all the specialist consultants including landscape, lighting, etc. Indeed, two comprehensive teams of stateside (USA) consultantsand their counterpart Singapore consultants were formed aswork slowly shifted from Boston to Singapore. The hallmark for the process was the workshops that occurred every three weeks, where architecture and engineering teams, specialist consultants, and client representatives from Las Vegas and Asia gathered in Boston for two to three days at a time to evolve the design and make the required decisions.
As this progressed, sub-teams were formed to deal with each component: the Spine which included the retail, the MICE convention centre, the casino, the theatres, the ArtScience Museum, the Crystal Pavilions, and the hotel. Each presented a complex project of its own, involving hundreds of millions of dollars' worth of construction.
Further considerable challenges had to be overcome, eg excavating six levels into the water table in what was highly unstable landfill and retaining the water and soil pressure while foundation and basement levels were constructed. Construction sequences and in particular, temporary supports for the construction of the hotel towers and their atria, the ArtScience Museum and the long-span spaces in the podium, proved to be as challenging as the final design was set in place.
Singpore's Government Authority
Singapore's Urban Redevelopment Authority conceived the Bay frontage as a segment of the continuum of promenades that surround the Bay and extend up the Singapore River. The landfill that provided the site for Marina Bay was itself intended to create an enclosed bay, helping to complete the loop and, through the construction of a dam, convert the Bay into a freshwater reservoir.
Seen from incoming cruise liners, a single tower would also have blocked the view of the city, so we decided to split the hotel into three towers, with the emphasis on achieving a delicate and dynamic scale for them Since each tower comprises two paralleled stretches of rooms straddling a corridor, we decided to give individual identity to each of the half slabs, slipping them in section so as to read independently of each other, and spreading them at the base to form a continuous series of atria. As the site tapered, the spread at the base varied from tower to tower.
Unified language and co-operation The major task, however, was to develop an architectural-engineering language for the project that would unify the parts, a system of detailing, cladding, and connectivity that would allow each individual element its uniqueness while at the same time making it cohesive as the whole. Working with the Arup façade team, developing for example the cladding systems for the podium and for cladding the SkyPark belly, each and every part required a unique solution while at the same time being part of the family of details.
Basement retaining walls and foundations for 3 high rise hotels
The integrated resort being built on Singapore's Marina Bay waterfront by Las Vegas Sands forms an integral part of the city state's development plan for the Marina Bay area. The hotel structures, over 50 storeys high, will dominate the Marina Bay skyline. Each structure is different with sloping sides splayed in two directions. The three are linked at roof level by a 'sky garden' over 300m long that will offer spectacular views of the vibrant downtown of the city.
Singapore were already on site to carry out the advanced works contract to clear an old seawall mole buried in the reclamation. The contract was also formed the cellular retaining walls for Towers One and Two where the abandoned mole encroached on the footprint of the hotels, known as the doughnut and peanut these were integrated into the final structure as the basement retaining walls.
The contract for the hotel foundations allowed for the construction of the remaining basement retaining walls between towers one and two and for tower three. The foundations for the three towers were essentially barrette piling although there were a number of bored piles for the lighter loaded elements of the structures.
Apart from the buried mole the site offered additional geological challenges due to the nature of the reclamation built over very soft marine clays. The retaining walls and the foundations were required to penetrate into the hard underlying old alluvium with many of the foundations reaching nearly 80m depth. The client had set an ambitious programme for the construction of the whole integrated resort and with the three towers being the most complex structures with foundations to match a tight programme was given to complete the works and handover each tower progressively to the follow on substructure contractor.
At the height of the activities on site Bachy Soletanche were operating up to 15 excavating rigs; 3 hydrofraise, 6 KS hydraulic grabs and 6 KL cable grabs all working 24hrs/day and 6 days/week. The logistics to keep the amount of equipment to work efficiently meant to be a strong management team, with a mix of local, regional and European staff. With up to 1,200 m3 of concrete being poured per day, at a time when concrete supply across Singapore was extremely stretched, the management of the site logistics was critical to ensure the success of the project.
Plan of retaining walls and foundations for the three hotel structures gave the tight programme; the bored piling and the jet grouting were executed concurrently with the diaphragm walls and barrettes adding to the already complex logistical challenge. Despite the geological and physical constraints to the works, Bachy Soletanche was able to complete each section of the works on schedule handing each tower over to the follow on contractor to commence the bulk excavation, pile cap and basement structure ahead of the iconic superstructure.
Tekla Digital Software
In working with the distinctive architecture of the complex, Arup relied heavily on Tekla as part of its work process. In almost all the structures that Arup was involved in, 3D modelling data was imported into Tekla so as to produce documents that could be used by the steel fabricators. In this way, Tekla was an invaluable tool during the design process.
For much of the Marina Bay Sands project, Tekla was used in this fashion, as a way to translate data from different BIM sources and into a format that steel fabricators could use to fabricate parts quickly. However, there is one major exception. For the roof of the Sands Expo And Convention Centre, Arup decided to go further and to use Tekla during the design phase as well.
The convention centre had its own set of challenges. The roof consists of waved, long-span steel roof forms and under it would hold Singapore's largest meetings, incentives, conventions and exhibitions space.
It was all by Hull Support Too!
Tremendous structural and construction challenges followed, not the least of which involved extensive wind testing and modelling. Originally, the hull-shaped belly of the park was designed as a pure toroid, but the form was streamlined to allow for efficient cladding: 9,000 silver-painted, metal-composite panels enclose the mega trusses that bridge the three towers at the 55th story. Offices for hotel operations and mechanical rooms housing water tanks for the swimming pools are also contained within the hull.
The hull was built off-site in 14 separate steel segments. Each was trucked to the site, lifted into place using hydraulic strand jacks, and assembled on top of the towers. The two largest sections were a pair of 262-foot-long, 1,400-ton box girders that formed the 213-foot cantilever. At a lifting speed of 46 feet per hour, it took more than 16 hours to lift the girders and slide them into place.
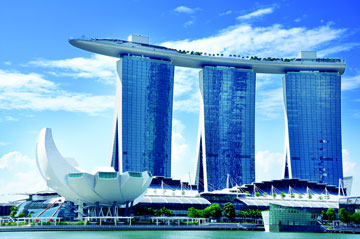 |
Marina Bay Sands exhibits the same ingenuity and fearlessness that defined Safdie's controversial Habitat 67 residential complex for the 1967 International and Universal Exposition in Montreal. The principles that drove that design more than 40 years ago remain the principles driving his work today: ethical standards, which require addressing the realities of urban density, demographics and scale while preserving the genius place confronted by globalization. On the other hand, what most distinguishes the Marina Bay Sands as Moshe Safdie design is his unflinching eagerness to push beyond perceived limits of construction to accomplish feats of derring-do.
Conclusion
Challenges Using its knowledge and determination to strive for excellence in particular to built such as the 120m diameter cofferdams for substructure works, the 66.5m long cantilever steel structure, the unique geometry of the ArtScience Museum, the glazing for the Crystal Pavilions and the long-span roof trusses for the podium structures. It exemplified what can be achieved in situations that need engineering judgment beyond what is distinctly covered by code.
In responding, the team adopted new and innovative technologies that pushed the boundaries of current software and systems, pulling together as a design team of global skills from four continents to communicate effectively and deliver outcomes to meet the client's needs and turn the design concept into reality. The local community benefits from the district cooling plant by avoiding the need for chiller plants and cooling towers on buildings. This in turn optimises the use of water and other natural resources for generating energy too.
Fact Sheet:
- Over 7,000 tons of steel were pre-assembled at ground level into 14 individual pieces commonly used in bridge construction and each lift required 24 hours. It is among the highest strand jacking operations ever undertaken on a building anywhere in the world.
- The Sands SkyPark, which offers a Public Observation Deck, lush gardens, an infinity pool and 3 Restaurants/clubs, is on the 57th floor, 200-metres above ground.
- The 12,400 square metres Sands SkyPark is longer than the Eiffel Tower is tall and large enough to park four-and-a-half A380 jumbo jets.
- The Sands SkyPark is home to the world's largest elevated swimming pool (150 metres long), which holds 376,000 gallons of water that's almost one and half million litres!
- The Sands SkyPark is home to 250 trees and 650 plants.
- The Marina Bay Sands Crystal Pavilions are the largest commercial floating structures to be built in the heart of Singapore.
- The initial construction work on the cofferdams began in September 2009. The installation ofthe steel and glass structure above water levels began in April 2010.
- The Southern Crystal Pavilion foundation is at its deepest at approximately 62-metres from the surface of the water while the Northern Crystal Pavilion is about 48-metres below the surface of Marina Bay.
- Approximately 650-tonnes of structural and architectural steel were used in the construction of each pavilion.
- 671 double glazed glass panel units were installed in the Northern Crystal Pavilion, while 532 panels were used in the Southern Crystal Pavilion. These glass panels were specially manufactured to suit the non-standard geometry of the pavilion facades.
- The highest point of the glass roof of each crystal pavilion is at least 17-metres or nearly 6-stories above the water surface.
- The tunnels connecting the Southern and Northern pavilions to the main Marina Bay Sands building are over 30-metres long.
- 5,200 tonnes of steel were used to construct the ArtScience Museum.
- 12,500 square metres of Glass Fiber Reinforced polymer (GFRP), a material more commonly used in boats and surf boards, was used for the overall cladding of the ArtScience Museum.
- The cladding process took abseilers 4 months to complete.
- The ArtScience Museum has 10 "fingers" of varying height and width, known as radial trusses.
- Longest Truss extends towards the sky at 45 metres.
- Shortest Truss extends towards the sky at 23 metres.
Box:
- James Carpenter, Blue Reflection Facade with Light Entry Passage
- Antony Gormley, Drift
- Ned Kahn, Wind Arbor, Rain Oculus and The Tipping Wall
- Sol LeWitt, Wall Drawing
- Chongbin Zheng, Rising Forest
References: