MODREN TRENDS in FORMWORK TECHNOLOGY
The Indian Construction Industry is growing at a very rapid rate and it is estimated that the current concrete production is about 300 million cum per annum is going to be doubled in the very near future. In the recent years, concrete technology has grown leaps and bounds. Advancement in concrete technology has resulted in many innovations and emerging trends which have occurred as a result of two major driving forces namely- Speed of Construction and Durability. New Concrete variations like High Strength / High performance Concrete, Self Compacting Concrete, Fibre Reinforced concrete, Polymer Modified Concrete, High Volume Flyash Concrete, Reactive Powder Concrete, concrete with super-plasticisers have changed the very perception of design and at the same time have posed new challenges in the arena of Formwork System.
It is estimated that the Formwork market in India commands the share of approximately INR 15 billion and out of this only about 20% is shared by the modern formwork systems leaving about 80% as untapped market. The Formwork industry including Scaffolding industry in India is still in its embryonic stage. With the impetus provided by the Government to the Infrastructure development, the growth and hence the growth possibility is enormous. The way RMC has made its dent in the construction industry, standardized formwork system will be accepted by the construction industry.
Current Scenario
As structures grow taller and floor plates bigger, end users are looking for formwork systems that are cost effective, light, reusable, safe, easy to assemble and dismantle, durable and flexible. There are quite a few formwork companies in India who are confident of providing the total integrated formwork design system for a specific project with fully engineered and compatible components. Some of the leading players in the market today are Doka, Peri, MFE (Mivan), Meva, Waco, BSL Scaffolding, Uday, Paschal and Pranav.
Classification
Formwork system can be classified as under depending upon the material used while manufacturing. Advantages and disadvantages of different forms are already discussed in the main feature article.
- Aluminium Forms
- Plastic Forms
- Fibre Forms
- Fabric Forms
- Timber Forms
- Steel Forms
- Form Liners
- Com Shells
- Inflated Forms
Form Types
Depending upon the function and use, Forms are generally classified as;
- Foundation Forms
- Column and Beam Forms
- Slab and Beam Forms
- Wall Forms
- Fly Forms
- Gang Forms
- Slip Forms
- Climbing Forms
- Jump Forms
- Cantilever Forms
- Single Sided Forms
- Tunnel Forms
- Bridge Deck forms
- Shaft Lining Forms
- Arch Forms
- Suspended Slab forms
- Insulating Concrete Forms
- Architectural Forms
Insulating Concrete Forms
For years, Insulating Concrete Forms (ICF) were used almost strictly for residential construction, but not anymore: the method is rapidly gaining popularity in commercial construction. Today approximately one-third of ICF structures are non-residential, according to the Insulating Concrete Form Association.
For design and construction, it’s hard to find an easier system than ICFs: hollow foam blocks or panels are stacked into the shape of the walls of a building. The forms are filled with steel-reinforced concrete to form a solid structure, sandwiching a heavy, high-strength material between two layers of light, high-insulation foam. The resulting walls are air-tight, strong, quiet, highly insulated, pest and fire resistant, and durable in the face of even the harshest weather.
The forms can be installed quickly and easily using common construction tools and equipment. The industry’s wide variety of manufacturers, shapes, and sizes makes it easy to custom design smaller commercial structures. ICFs are commonly used for industrial buildings, hotels, business parks, government facilities, schools, churches, shopping centers, and warehouses.
The high R-value of the insulation, the thermal mass of the concrete, and the system’s ability to moderate temperature swings all combine to make structures with ICFs ideal for climates with large temperature variations…but ICFs can increase energy efficiency (and cut operating costs) in any region. Structures with ICFs are strong and durable—even in seismic zones, structures with ICFs can offer protection during earthquake activity. ICF systems are accepted by all the major model codes in the U.S., and by the R-2000 program in Canada.
Wall Forms
With the explosive growth in high-rise residential construction, the Load-Bearing Wall (LBW) system is gaining recognition. The walls and slab are poured simultaneously when using the innovative tunnel form construction method. Since the forms are stripped in 24 hours, the daily cycle meets the demand of fast-track construction for repetitive cell layouts, synonymous with many hotel and condominium projects. The benefits of using aluminium forms are superior to the old method of plywood forming for formed cast-in-place concrete. Apart from the dimensional stability of the forms, the overall quality of the pour seems much better with tighter tolerances.
This system of formwork facilitates casting of all walls, floor slabs, columns, beams, stairs, balconies, together with joinery openings in a single operation. The resulting structure is monolithic, strong, and accurate and with high quality finished surface. It tremendously improves the time cycle and very cost effective when used with repetitions.
This system is made of extruded aluminium sections, welded to an aluminium sheet and hence very light with an excellent stiffness to weight ratio, yielding minimal deflections under concrete loading. Panels are manufactured in standard sizes with non-standard elements produced to the required size and shape to suit the project requirements. The panels are made from a high strength aluminium alloy, with the face or contact surface of the panel, from 4mm thick plate, which is welded to a framework of specially designed extruded sections, to form a robust component. Manufacturers claim that this system can have approximately 250 repetitions.
Com-shells
A Comshell roof is a steel-concrete composite shell roof formed by pouring concrete on a thin stiffened steel base shell which serves as both the permanent formwork and the tensile steel reinforcement. The steel base shell is constructed by bolting together modular steel units in the form of an open-topped box consisting of a flat or slightly curved base plate surrounded by edge plates. The edge plates may have lip stiffeners for enhanced local buckling resistance.
Architectural Forms
Architectural concrete differs from structural concrete in that sense the appearance or color of the exposed surfaces of the forms may be more important than the strength of the members. The properties of fresh concrete are such that it may be cast or molded to produce any shape that forms can be made. A variety of colors may also be obtained by adding a color admixture to the concrete mix or by adding a surface coating after the concrete has hardened.
The surfaces may be extremely smooth or they may be quite rough, depending on the desired effects. The appearances of large and possibly drab areas can be improved greatly by the use of recessed or raised panels, rustications, ornaments, and other designs. Metal molds can produce concrete having extremely smooth surfaces. A variety of surface patterns can be obtained using form liners that are placed on the inside of plywood sheathing. A large variety of shapes is available from companies that supply formwork accessories.
Because the quality of the finished concrete is limited by the quality of the forms, it is necessary to exercise care in selecting the materials for the forms. Also, high-quality craftsmanship is required in building and stripping the forms of architectural concrete if the desired effects are to be achieved with a satisfactory degree of perfection.
Formliners
Sheets of rigid form liners are attached to the formwork or casting bed prior to placing the concrete. Screws or nails are recommended for mounting form liners. Following placement and normal curing time, the formwork and liner are stripped, leaving a textured concrete surface.
The sheets generally are 4 ft wide and 10 ft long with square edges to allow the placement of adjacent sheets for large areas of concrete. The hard, void-free surface will not absorb moisture or cause discoloration. Sheets of rigid form liners are lightweight and easily stripped.
Rustication or reveal strips are recommended at the liner joints that do not blend with the pattern. A properly sized rustication will complement the pattern and enhance the overall appearance of the structure. For uniformity of color and texture, the concrete should be secured from a single supplier so that all of the ingredients will come from the same source.
Drophead Formwork
Peri, one of the biggest formwork manufacturers offers a unique ‘Uno Monolithic Housing Formwork’ which is used for monolithic construction method. The Uno formwork is predominantly used for residential housing development and similar, whereby large numbers of residential units with identical dimensions are extended horizontally and vertically.
Figure 1: Flying table forms for the acelerated construction of the tower slabs- Image source:
http://www.structuremag.org/article.aspx?articleID=836
The company says all Uno elements, girders and stopend plates are made of aluminium and weigh a maximum 23 kg/m². This means problem-free forming can be done manually. It is very easy to assemble. A hammer is sufficient when working with Uno.
Thanks to the new mechanism, the wall formwork elements can easily be dismantled even with slab formwork elements still installed. After dismantling the Spacer Clamps, the wall element is simply unscrewed from the wall/slab transition area. The transition to the horizontal formwork is flexibly designed so that striking can be easily carried out in this area as well.
Figure 2: Original Page: http://www.hi-lite-systems.com/concrete-shoring/aluminum-fly-forms/aluminum-fly-form-details
The design of the slab formwork as drophead formwork allows early striking to take place – usually after only one day. For setting of stopends and box-outs, Uno Stopend Plates are available, which are adapted to the wall thicknesses in 1 cm increments. In addition, the integrated toothed rack of the shuttering strip absorbs the concrete load and thus replaces the formwork tie.
Flying Forms
Figure 3: Hi-Lite Flyform system
Flying Deck Form or the Table Form consists of various structural components, such as trusses, stringers, joists, and decking layer. The unit is rigidly assembled to be used and reused in moulding the concrete slabs of a building. The forms may be used to support concrete beams, girders, slabs, and other parts of a structure.
Once the casting of the slab and the consequent curing period is over, the flying form is lowered without dismantling the parts of the system and moved outwards horizontally and shifted to the new location to cast the next level slab. The term is derived from the process of moving (flying) the form outward, away from the building, as it is moved upward to the next floor level in the structure. In case of a high-rise building where the formwork system is designed using these table forms, cost of construction will come down substantiall
Inflated Forms
Inflated forms are generally used where the accessibility is difficult and the time available for erecting the structure is very short. Though this method is quite old, innovations have made it possible to gain popularity. There are several methods of construction using inflatable forms but in general, it comprises of inflating the fabric form and then applying the shotcrete along with nominal reinforcement followed by curing. Shotcrete can be applied either from the outside or from inside. After the desired curing period these inflatable forms are either left in place as a part of structure or deflated and taken out. These forms can also be used in the construction of thin-shell concrete dome structures.
Innovations in the field have resulted in the advent of new inflatable forms popularly known as Concrete Canvas. Concrete Canvas (CC), is a flexible, cement impregnated fabric that hardens when hydrated to form a thin, durable, water proof and fire resistant concrete layer. CC allows concrete construction without the need for plant or mixing equipment. Simply position the Canvas and just add water.
Concrete Canvas (CC)
CC consists of a 3-dimensional fibre matrix containing a specially formulated dry concrete mix. A PVC backing on one surface of the Canvas ensures the material is completely water proof. The material can be hydrated either by spraying or by being fully immersed in water. Once set, the fibres reinforce the concrete, preventing crack propagation and providing a safe plastic failure mode. CC is available in 3 thicknesses: CC5, CC8 and CC13, which are 5, 8 and 13mm thick respectively.
CC is a low mass, low carbon technology which uses up to 95% less material than conventional concrete for many applications. It has minimal impact on the local ecology due to its limited alkaline reserve and very low wash rate. The impact on the environment is further decreased by reducing the need for plant equipment.
Figure- Concrete Canvas for slope protection.
Concrete Canvas Shelters (CCS)
Extension of Concrete Canvas technology resulted in Concrete Canvas Shelters which are are rapidly deployable hardened shelters that require only water and air for construction. The key to CCS is the use of inflation to create a surface that is optimised for compressive loading. This allows thin walled concrete structures to be formed which are both robust and lightweight. A 25sqm CCS can be deployed by 2 people in less than 1 hour and is ready to use in only 24 hours.
Concrete Canvas (CC) is fire-safe, does not contribute to the surface spread of flames, and has a low level of smoke development and minimal hazardous gas emissions. Each shelter is lined with a flame retardant fiber reinforced polyethylene inner with a B1 (DIN 4102-01 05/98) fire rating. CCS can be fitted with a ventilation system along with security door. CCS provides all the benefits of a permanent structure without the associated cost and time delays.
Fabric Forms
A new construction method replacing rigid formwork panels with a flexible textile membrane that deflects under the dead weight of wet concrete provides numerous advantages and opportunities for architecture, engineering, and construction technology in both advanced and basic building economies. Inexpensive formwork fabrics provide the options of sacrificial or reusable formworks in both precast and cast-in-place applications. Methods have been developed for fabric-cast foundations, walls, columns, capitals, slabs, and beams.
Permeable membranes allow air bubbles and excess mix water to bleed out, producing a flawless, cement-rich finish and a stronger and more durable concrete. Structurally efficient variable section members are easily formed, reducing dead weight and material expenses.
Fabric forming applications include Foundations, columns, walls, thin shell structures, concrete trusses, vaults, thin-shell funicular compression vaults- nearly anywhere a rigid formwork is used.
Some of the main advantages are;
- Economical, Extremely light weight compared to conventional form.
- High level of refinement in the surface finish and texture of cast concrete.
- Production of stronger and less permeable concrete surfaces.
- Possibility of casting complex structural elements of any size and shape.
Slipform
Slipform is an ever moving form at such a speed that the concrete when exposed has already achieved enough strength to support pressure from concrete above as well as to withstand lateral pressure. The major advantages of this system are mainly speed and economy. It also results in a monolithic structure. In many cases, the cost of materials and building of the Slipform is about the same as for fixed forms. The economy comes from shorter construction time. The Slipform process requires a more experienced crew at all levels – forms should be designed and built by individuals experienced in the field.
Figure: Work in progress-on deck view
Slipform construction is normally used for vertical structures such as bridge piers. In Vertical Slipform, the system usually moves by an integrated system of jacks riding on smooth steel rods or Jack rods which subsequently get embedded in the hardened concrete. Horizontal Slipform generally moves on a rail system.
Factors to be taken into account when considering Slipforming as a system of formwork:
- Construction time is greatly reduced, though the initial setting-up of the formwork is usually a lengthy process.
- Working in shifts becomes inevitable, increasing the labour costs, but the greater degree of mechanisation and control allows higher productivity.
- Back-up plant must be held on site in cases of breakdown.
- The concrete surface will exhibit slide marks and may need surface finishing.
- Formwork must be properly designed and must include adequate bracing and a jack layout which will accommodate variations in frictional loading which may occur due to irregularities in plan shape, and openings being formed.
- The dead load of the form, the frictional load, weight of materials, personnel, and equipment and working platforms must be accounted for during the design of the jacks.
New trends
The Paschal Group, one of the leading formwork players have come out with an innovative modular slab formwork branded as - E-Deck. The frame of the new elements is made from profiled steel and, with a height of 7.5 cm provides very good grid compatibility and flexible application options, for transportation as well as for installation. The facing of the formwork consists of a 9-layer, 12 mm thick sheet of birch plywood, so that the weight of the individual elements is a maximum 20 kilograms and can be used with no problem without a crane. The E-Deck has the advantage that damage to the frame can be repaired, which is not possible on comparable aluminium products.
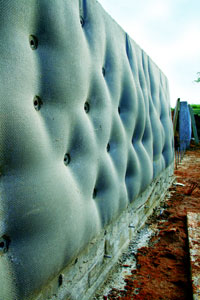 |
Framed Formwork Frami xlife from DOKA is a new complete system, which also comprises high-performance safety and workplace accessories. The Frami Xlife panels are lightweight and easy to handle, so they can be erected very quickly by hand. Frami Xlife lets you form extremely quickly and economically, without the use of a crane. On sites with a crane, it is also possible to lift several panels at a time, in a gang-form. The ingenious modular design (with six different widths and three different heights of panel) makes for optimum adaptability to all job site conditions.
Acknowledgements and References:
1.’Formwork for concrete structures’ by Robert Puerifoy and Garold Oberlender
2. Valuable inputs from SA Reddi, Deputy Managing director, Gammons.
3. Concrete Plant International Issue 3 (June/July) 2010
4. Concrete Canvas company ltd UK
5. Construction of Concrete Shells Using Inflated Forms-Reported
by Joint ACI-ASCE Committee 334
6. Hi-Lite Systems, Canada
7. www.paschalinternational.com