World's First 'Glow-in-the-Dark' Road
Recently, prolific Dutch designer Daan Roosegaarde and civil engineering firm Heijmans nabbed headlines by installing the world's first glow-in-the-dark road in the Netherlands. The futuristic road is lined with paint treated with photo-luminizing powder that charges in the sunlight and emits a green glow for up to 10 hours at night. The light-absorbing luminescent road paint was developed as part of Roosegaarde's award-winning "Smart Highway" concept, which seeks to make our roads more interactive, environmentally friendly, and safe, particularly in rural areas that lack street lighting.
Although the pilot program was praised by users for its cool and energy-efficient Tron-like design, engineers ran into an early hiccup shortly after its unveiling. The glow-in-the-dark paint turned out to be sensitive to moisture caused by rainfall, which severely compromised the light output emitted by the markings. Undeterred, Heijmans says that the issue is but a temporary and expected stumbling block for the pilot program. The firm plans to use the insights gained from the month-long trial to introduce an update to Glowing Lines 2.0, which is expected to roll out this summer.
While the "Smart Highway" team irons out the kinks for the photo-luminescent roadways, Roosegaarde is pushing the boundaries of glow-in-the-dark technology in yet another invention that could replace street lights: auto luminescent trees. Working together with Bioglow, an American biotechnology firm that developed the world's first light producing plants earlier this year, Roosegaarde and collaborator Alexander Krichevsky envision streets lit up by Avatar-style glowing trees. Taking cues from biomimicry, the light-emitting plants are created by splicing in DNA from luminescent marine bacteria. Krichevsky has also started a project separate from Roosegaarde that uses a light coating of "biological paint" rather than genetically modified material to make trees glow in the dark.
It is unclear how soon glow-in-the-dark technology will supplement or even replace electricity-guzzling light sources, but recent scientific breakthroughs have firmly moved these innovative ideas from the realm of science fiction to reality. This great "first" might very well be the next stage in eco-living: just like the LED bulb, we predict that it's only a matter of time before these cleaner and more sustainable forms of lighting become an affordable staple in our future world.
Great innovations in technology have had enormous impact on people's lives, and changed the entire world forever. From the first electric light to the first phone call, and even the first email, innovation has moved us into a future that previous generations couldn't have imagined. How have these historic firsts influenced your own life? How do you feel about this new glow-in-the-dark technology?
Read more: World's First Glow-in-the-Dark Road Promises a Brighter, More Energy-Efficient Future Glow in the Dark Technology Daan Roosegaard – Inhabitat - Sustainable Design Innovation, Eco Architecture, Green Building.
Delve Into Two Theories Related to Cracks and Rebar Corrosion
by Kim Basham, PhD PE FACI
Concrete cracks for various reasons including plastic concrete shrinkage and settlement, thermal contraction, drying shrinkage and loading of the structure. Because the tensile strength of concrete is only about 10 percent of the compressive strength, even small tensile stresses associated with shrinkage and loads can crack concrete. Regardless of the cause, cracks in new structures typically raise concerns about an increased risk of rebar corrosion and premature concrete damage, especially if the structure is exposed to moisture.
Historically, there have been two theories related to cracks and steel reinforcement corrosion:
Theory 1 - Cracks significantly reduce the service life of structures by permitting access of carbon dioxide, chlorides, water and oxygen to the reinforcing steel that accelerate the onset of reinforcement corrosion.
Theory 2 – While cracks may accelerate the onset of corrosion, it is localized and confined to the bar area intersected by the crack.
Over the years, researchers have debated theories one and two using both laboratory and field test data (Ref 1). An abundance of published information appears to support both theories. However, A.W. Beeby, Dr. Chanakya Arya, and Professor Laurence Wood essentially ended the debate by concluding both theories are correct (Ref. 2 and 3). Briefly, these researchers (and others) concluded the following:
- Crack width has little influence on corrosion.
- Major factors controlling corrosion are concrete quality (e.g., cementitious materials content and water to cementitious materials ratio - w/cm ratio) and concrete cover.
- Corrosion potential is strongly influenced by the orientation of the crack relative to the reinforcement (i.e., coincident versus intersecting). Theory one applies to cracks that coincide with the reinforcement and Theory two applies to cracks that intersect the reinforcement.
Reinforcement Corrosion
Corrosion of steel reinforcement in concrete is due to an electrochemical process as illustrated in Figure 1. There are four essential parts to an electrochemical corrosion cell:
- Anodic site where ferrous ions (Fe++) pass into solution and due to a secondary reaction with oxygen and water form rust (or the expansive product of steel corrosion).
- Conductor (steel reinforcement) that provides a conduit for excess electrons (e-) to move to the cathodic site.
- Cathode where electrons are consumed in the presence of oxygen and moisture.
- Electrolyte or wet concrete that provides a conduit for hydroxyl ions (OH-) to flow to the anodic site.
Steel reinforcing bars embedded in concrete do not corrode because the high alkaline conditions in concrete (pH > 13) produce a passive oxide film on the surface of the steel. The passive oxide film prevents corrosion. However, carbonation and/or chlorides in solution can destroy the passive oxide film. Carbonation and loss of passivity can occur when atmospheric carbon dioxide penetrates into the concrete and in the presence of moisture reacts with the calcium hydroxide to produce calcium carbonate. Calcium hydroxide is a cement hydration product that helps create the high alkaline condition in concrete. Due to the formation of calcium carbonate around the steel, the alkalinity (pH) of the concrete falls from above 13 to less than nine. Subsequently, the low alkalinity destroys the passive oxide film.
Carbonation is a very slow process in good quality concrete. Therefore, the risk of depassivation of steel reinforcing and onset of corrosion depends on the permeability of the concrete, concrete cover and exposure conditions (i.e., moisture). Of course, cracks can open a direct pathway for carbon dioxide to reach the steel and disrupt the passive oxide film. If the other essential conditions for corrosion exist, then an anodic site can form and corrosion can occur where the crack intersects the reinforcing bar.
For corrosion to occur, oxygen and moisture must be available at both the cathodic region and along the hydroxyl ion conduit (concrete) between the cathode and anode. Since these two requirements for corrosion are independent of the crack width, it follows that the corrosion rate of the steel reinforcing is also independent of the crack width. Many researchers report there is no correlation between crack width and steel reinforcing corrosion in concrete (Ref 4).
Therefore, the major factors controlling the risk of steel reinforcing corrosion of cracked concrete are the quality of concrete and concrete cover - not the crack width. Good quality concrete (i.e., low permeability) and adequate concrete cover inhibits the cathodic site and the hydroxyl ion conduit from forming. Without the cathode and hydroxyl ion conduit, the electrochemical corrosion cell does not form and steel corrosion does not occur.
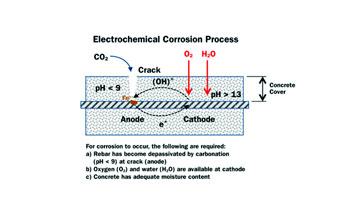 |
High quality of more specifically, dense concrete reduces the risk of corrosion by restricting the penetration of oxygen and moisture into the concrete, restricting ionic movements within the concrete and increasing the bond strength of the concrete to the steel. Of course, the quality or more specifically, the permeability of the concrete depends on several factors including the cementitious materials content, water-cementitious materials ratio, concrete consolidation and curing. Increasing the cement content can help reduce permeability but also increases the alkali loading or content of the concrete that helps maintain the concrete's alkalinity and preserve the passive oxide film on the steel reinforcement.
Building codes establish the minimum concrete cover according to the anticipated exposure of the concrete to moisture. As the concrete's exposure to moisture increases, the minimum specified concrete cover increases. For a #6 bar, the specified minimum concrete cover is three-quarters of an inch when concrete is not exposed to weather or in contact with the ground, two-inches when concrete is exposed to earth or weather and three-inches when concrete is cast against and permanently exposed to earth. Increasing the concrete cover reduces the risk of steel reinforcing corrosion.
Crack Orientation
There are two orientations of cracking in reinforced concrete:
- Longitudinal (i.e., cracks running parallel or coincidental with the steel reinforcing).
- Transverse (cracks intersecting the steel reinforcement) as illustrated in Figure 2.
Longitudinal cracks follow the line of reinforcement and transverse cracks cross the reinforcement. Transverse cracks include diagonal cracks.
Longitudinal Cracks
Depending on the width of the crack where it intersects the steel, longitudinal cracks may promote corrosion of the steel reinforcement. Increased risk of corrosion occurs because passivity of the steel may be lost at several locations along the reinforcing. In addition, the same crack may allow the migration of oxygen and moisture to the cathodic sites and to the hydroxyl ion conduit completing the formation of the electrochemical corrosion cells. Theory 1 applies to longitudinal cracks.
Typically, longitudinal cracks occur due to plastic settlement or subsidence of the concrete, poor concrete quality and inadequate concrete cover. Poor concrete quality and inadequate cover may allow the formation of electrochemical corrosion cells and expansive corrosion products and subsequently cause longitudinal cracks to occur. Of course, the formation of longitudinal cracks typically and classically promotes the corrosion of the steel reinforcing.
Transverse Cracks
Intersecting cracks may open a direct path for carbon dioxide, oxygen and moisture to reach the steel reinforcing. However, because the cathodic sites are primarily confined to the crack-free regions of the concrete, any oxygen and moisture that penetrates into the crack will not affect the onset or rate of steel corrosion along the rebar or where the crack intersects the rebar. Therefore, transverse cracks do not increase the risk of steel corrosion unless the concrete is of poor quality and/or the concrete cover is inadequate so that oxygen and moisture easily penetrate the concrete. Theory 2 applies to transverse cracks.
When evaluating new cracks and the potential for rebar corrosion, crack orientation, concrete cover, quality of the concrete and exposure conditions are just as or more important than crack widths.
References
1. Darwin, D., "Debate: Crack width, cover, and corrosion," Concrete International, American Concrete Institute, www.concrete.org, May 1985
2. Beeby, A. W., "Cracking, Cover and Corrosion of Reinforcement," Concrete International, American Concrete Institute, www.concrete.org, February 1983
3. Technical Report No. 44, "The Relevance of Cracking in Concrete to Corrosion of Reinforcement," A Report of a Concrete Society Working Party, The Concrete Society,
4. Beeby, A.W., "Cracking, Cover and Corrosion of Reinforcement," Concrete International, American Concrete Institute, www.concrete.org, February 1983
Additional Reading
ACI 224R-01 Control of Cracking in Concrete Structures, ACI 224.1R-07 Causes, Evaluation and Repair of Cracks in Concrete Structures, ACI 222.2R-92 Cracking of Concrete Members in Direct Tension and ACI 222.3R-11 Guide to Design and Construction Practices to Mitigate Corrosion of Reinforcement in Concrete Structures, American Concrete Institute, www.concrete.org
President Obama Orders Cuts in Federal Greenhouse Gas Emissions
By Julie Hirschfeld Davis
WASHINGTON - President Obama signed an executive order on Thursday to set new goals for reducing the greenhouse gas emissions of federal agencies, his latest use of his executive authority to address the root causes of climate change and press private companies and foreign governments to follow suit.
Mr. Obama's directive orders federal agencies over the next decade to cut their emissions by an average of 40 percent compared with their levels when he won office in 2008, and to increase their use of electricity from renewable sources by 30 percent.
The goals are in line with a commitment that he announced in November as part of a climate agreement with China. In the deal, Mr. Obama said the United States would reduce its emissions of the heat-trapping gases that are warming the planet by 26 percent to 28 percent below 2005 levels by 2025.
They are also part of Mr. Obama's effort during his last two years in office to use an expansive interpretation of his presidential authority to push ahead with unilateral moves to combat climate change in the face of strong opposition from the Republican-controlled Congress to advancing legislation that would do so.
"We're proving that it is possible to grow our economy robustly while at the same time doing the right thing for our environment and tackling climate change in a serious way," Mr. Obama said during a visit to the Energy Department on Thursday to announce the order. "America once again is going to be leading by example."
The federal government's share of greenhouse gas emissions in the United States is minuscule - less than 1 percent in 2013, the last year for which data is available - so the order by itself is unlikely to make a major dent in the president's broader goals to cut emissions.
But because the federal government is the largest user of energy in the United States economy - encompassing 360,000 buildings, 650,000 fleet vehicles and $445 billion in annual spending on goods and services - it has the potential to influence private companies to step up their emissions-cutting targets.
In conjunction with the executive order, the Obama administration released a new scorecard to allow federal suppliers to disclose their emissions and track their reductions. Several large companies that do business with the federal government - including I.B.M., General Electric, Honeywell and Northrop Grumman - announced new emissions-cutting goals of their own.
"As we get economies of scale, and demand for solar and wind and other renewable energies grows, obviously that can help drive down the overall price, make it that much for efficient, and we start getting a virtuous cycle that is good for the economy and creates jobs here in America," Mr. Obama said after touring the Energy Department's solar-paneled rooftop.
At a round table with representatives of some of the private corporations taking part, Mr. Obama praised the companies for stepping up with new or enhanced emissions-cutting targets.
"You guys have done an outstanding job," he said. "Because of the prominence of many of the companies here, and the fact that they've got a whole bunch of suppliers up and down the chain, what you do with respect to energy efficiency is going to have a ripple effect throughout the economy."
Mr. Obama's directive extends a goal he set during his first year in office, when he signed an executive order to cut federal greenhouse gas emissions by 28 percent by 2020.
Since then, said Christy Goldfuss, the managing director at the White House Council on Environmental Quality, federal agencies have reduced their emissions by 17 percent, and increased, to 9 percent from 3 percent, the share of electricity they consume from renewable sources.
White House officials, who are increasingly describing Mr. Obama's environmental agenda in economic terms, estimated that the directive issued on Thursday could save up to $18 billion over the next decade by cutting down on wasted energy.
"For federal agencies who are looking at how to cover their energy needs, this is a very pragmatic dollars-and-cents issue," said Brian Deese, a senior adviser to Mr. Obama. "If they can consume less energy or they can consume renewable energy that is cheaper, more reliable or more sustainable, then they can achieve their environmental goals while they are saving money."
Having failed during his first term to push a cap-and-trade bill through Congress, Mr. Obama has undertaken a systematic effort to regulate pollution through the existing Clean Air Act, advancing new rules on emissions from cars and trucks, power plants and oil and gas wells.
Mr. Obama has also laid out an ambitious overall emissions-cutting goal for the United States ahead of a United Nations climate conference in December in Paris, and is expected by the end of the month to release his detailed plan for reaching those targets.
A version of this article appears in print on March 20, 2015, on page A20 of the New York edition with the headline: Obama's Order to Reduce Greenhouse Gas Emissions of Federal Government.
Curved Glass of New York's Residential Towers
At the construction site morphing skyward at 50 West Street, a curvaceous 64-story glass-and-steel condominium whose distinguishing exterior motif will be its transparent assemblage of rounded corners, Daniele Petroni, protected from a flutter of snowflakes by his fashionably gray hard hat, gave a huge curved glass panel near the base a paternal pat.
If Mr. Petroni, a project manager whose specialty is curtain walls, could have hugged the nascent building, where 151 luxurious residences are scheduled to be completed by the end of next year, he probably would have.
"I love curved glass," he said, his declaration lent a courtly cadence by his Italian accent, "because to me the views it makes possible translate into architecture having an open mind. Looking through this glass, your perspective instantly widens. It's magical. And it's gentle on the eyes."
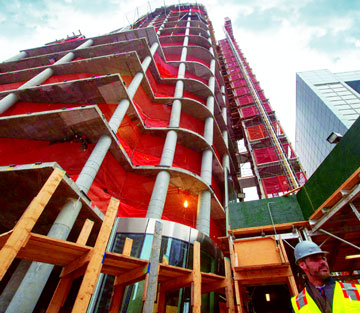 |
It's like looking through a fun house mirror that enhances rather than distorts, except that the experience is more expensive: One-bedroom apartments with 20-foot-high living room walls of curved glass start at $1.83 million, while penthouses with 360-degree views begin at $18.65 million. And because the virtually seamless vistas this technologically precocious triple-pane glass makes possible are gaining traction with high-end developers and their demanding clientele, Mr. Petroni's area of expertise, and passionate interest, is proving timely. In a 21st-century tweak of that oft-cited prophecy in "The Graduate," the future isn't plastics, it's glass, especially when the product in question is over-the-top urban spires.
According to Mr. Petroni, 31, curved glass's moment has just begun. The use of curved glass eliminates the need for corner panels and vertical mullions that obstruct views, and it gives the resident a much broader view with less interruption; in a sense, the view is magnified.
After Permasteelisa North America, a division of the global behemoth with a factory in Windsor, Conn., was chosen to source, design and install the highly unusual and complex curtain wall at 50 West, the company appointed Mr. Petroni as the project manager for the facade. Time Equities is the developer of the $500 million building, which was imagined by the innovative architect Helmut Jahn. Fifty West's glass was made in Northern Europe, sent to Spain for further refinement if it was to be flat, or to China if it was to be curved, and then to Connecticut to be inspected.
Mr. Petroni's qualifications? At his previous construction site, Extell Development's 157 West 57th Street a.k.a. One57, he managed to rectify the damage caused by a Hurricane Sandy-induced crane incident and to assemble a bold architectural envelope designed by Atelier Christian de Portzamparc, an ambitious jigsaw puzzle of some 8,200 panels of bluish glass, in 2,200 different shapes and shades, no more than 300 of which were identical.
Continue reading the main story
Mr. Petroni realizes that One57 elicited mixed reviews, but in his opinion, "It's a future landmark. To me, architecture is about emotion, and I'd rather be part of a project that draws a strong reaction from the community than to be ignored."
Mr. Petroni, an architect's son whose obsession with curved glass towers started early - "I always looked at tall buildings and saw squared-off cubes that could be so much more beautiful if their corners were curved" - has found his niche as a glass whisperer of sorts.
Before 50 West and One57, he worked on the facade of the One World Trade Center podium for the Port Authority of New York and New Jersey and the facade of 3 World Trade Center for Silverstein Properties. "During this project is when I almost said goodbye to my hair," he said of the difficulties he encountered there.
At 50 West, he is supervising the installation of 3,000 panels of glass - 500 of them curved, some of which weigh 1,900 pounds - framed by aluminum and braced by stainless-steel panels that are made in Italy. Mr. Petroni said that curved glass panels can cost 300 to 500 percent more than flat glass. He knows of no other building that uses curved glass in such volume, from street level to penthouse level, nor has he ever worked with so global a cast of artisans.
Coordinating their efforts occupies a significant amount of his time. "Four months ago I was in Italy to look at steel, three months ago I was in Shenzhen, China, for the curved glass, and then after it was shipped over, I spent days and days looking at panels at our corporate headquarters in Windsor," Mr. Petroni said. He usually spends two days a week at his apartment in West Hartford, Conn., and is apartment-hunting downtown near 50 West and the Permasteelisa office at the Avenue of the Americas and Canal Street.
"Needless to say, this is the most fascinating and challenging project I've had the opportunity to manage," said Mr. Petroni, whose first New York City project was at 475 Park Avenue South as an assistant site manager. "It's not only boundary-breaking in terms of curved glass technology, it's also brought together the world's best manufacturers."
Lean, bearded and blue-jeaned, Mr. Petroni grew up in Marina di San Nicola, a village near Rome. His father gave him a two-part lesson when he was 11 that eventually led him to his vocation: "He took me to a bench on the edge of our village and asked me what I saw. I saw two trees and an empty parking garage. He took me back to the same spot two years later and asked the same question, and I saw a big new building and families and kids on a playground. He told me I was looking at the real meaning of architecture."
When Mr. Petroni moved to New York from Rome at age 24 armed with an architecture degree from La Sapienza in Rome, he spoke only Italian and had no job lined up. These days he can converse in English, Spanish and Mandarin, and has a master's degree in construction administration from Columbia University. He has been working his way up the ladder at Permasteelisa, a firm with 6,500 employees, since 2009. The company's New York projects include 8 Spruce Street and the Hearst Tower.
"Permasteelisa was awarded our curtain wall contract after a worldwide bidding contest," said Robert Singer, the director of development for Time Equities. "There were firms that decided it was too complicated, and some that thought they could execute what we had in mind, and then there was Permasteelisa. They had an international reputation for engineering prowess and attention to logistics, proved to us that they could execute this job, and Daniele, the project manager for the facade, has been like a gift that came with the purchase. He's as obsessed with the quality of the glass as we are."
Mr. Singer said the decision to curve all four corners of 50 West was dictated by the site. "We felt it would not only create an interesting exterior, but inside it would give the homes the most natural viewing experience of the harbor and river. We're not trying to do fancy or complicated just for the sake of it," he added. "We realize we're pushing the envelope design-wise. This curved glass facade not only defines our project but also defines the legacy of Permasteelisa. It's like a site-specific artwork."
Mr. Petroni conceded that residential developments like One57 and 50 West are accessible only to a rarefied clientele. "Yes, it's only for a few on the inside, but it's for everyone on the outside. Anybody can build a cube," he said. "These special towers are what separate the developers who dream big from the ordinary guys."
About his contribution to the city's horizon, he said, "It's about the challenge. Wherever in the world the next big challenge is, that's where I want to be."