CALCINED CLAYS IN MODERN BUILDING MATERIALS: POTENTIAL APPLICATIONS IN CONCRETE AND COMPOSITE CEMENTS
Eugen Kleen
Head, Mineral Building Material and Concrete Technology Division
MC-Bauchemie Mueller GmbH and Co. KG, Am Kruppwald 1-8, 46238, Bottrop, Germany eugen.kleen@mc-bauchemie.de
Abstract:
The use of calcined clays as additives in mortars and concretes dates back to antiquity. In light of the current focus on sustainability and due to the increased demands on the technical performance of modern construction materials, calcined clays are back in use in advanced civil engineering applications. The application areas being explored for calcined clays include: use as a concrete additive; use as a main ingredient in composite cements (OPC-Pozzolan Blends); and use as alumina siliceous components in geopolymer systems / geopolymer concrete. While the use of geopolymers in construction has limited applications, the first two fields open up a vast application potential for the use of calcined clays. Non-calcined clays exhibit no pozzolanic reactivity whatsoever, and are largely unsuitable for use, even as purely inert filler in cementitious systems. This is due to their special crystalline structure and the associated negative effects on concrete properties such as decreased frost resistance, decreased resistance to freeze-thaw, shrinkage/swelling, etc.
When calcined clays are used as additions to concrete, it is mostly burnt kaolin, or so-called metakaolins. With them, special specific concrete properties can be achieved, aside from an improved eco-balance. Metakaolin can be used in high-strength and ultra-high-strength concretes as an alternative to microsilica. Metakaolin can furthermore considerably increase the durability of concretes (increased resistance to ASR, increased chemical resistance, etc.). This is achieved by the optimal combination of physical, chemical and mineralogical mechanisms of the individual components in the mix. Ultrafine / nanoscale pozzolanic materials, such as calcined kaolin, facilitate better particle packing at similar corresponding water-binder ratios. This enhances the chemical resistance of the binder, even in case of slightly higher permeability in the matrix.
This paper reviews the latest applications / joint studies between Bauhaus University, Weimar, MC-Bauchemie Mueller GmbH and Co. KG and other industry partners incorporating these materials in the development of ceramic- like UHPCs and also their use in new generation composite cements.
INTRODUCTION
Fig. 1: Calcination Zone for Metakaolin
The experience of use of calcined clays in construction for mortars and concrete dates back centuries. For example, the water storage “cisterns” unearthed in Jerusalem makes use of a waterproof mortar consisting of fired brick powder (calcined clay) and hydraulic limes. This system, dating back to about 1000 BC is over 3000 years old. This principle was also used in develop cements and cementing mortars in Germany ca. 1400 and Great Britain ca. 1800 AD. Since the development of Portland Cements (1843, Joseph Aspdin), the importance of using calcined clays has somewhat declined. However, due to the current focus on sustainability and increased demands on the technical performance of modern construction materials, calcined clays are finding their way back for use in advanced civil engineering applications.
The main applications include:
- As an additive to concrete / mortar systems a. As a substitute to microsilica in UHPCs b. To improve concrete/mortars in terms of durability (increased resistance to Alkali Silica Reaction [ASR], increased chemical resistance, etc.)
- As major components in Portland composite cements
- As alumina-silicate component in geopolymer systems. However as application of geopolymer systems is limited, we shall cover only the first two applications in this paper.
THE CALCINATION PROCESS
Fig. 2: Formation of Metakaolin after Calcination of Kaolinite
Calcination is a prerequisite for processing clays for the applications stated above and to enhance their pozzolanic reactivity. In this case, the calcination involves removal of the hydroxide group from the clays and decomposition of the clay minerals into reactive aluminium and silicon compounds in the amorphous phase. The calcination temperatures required to achieve this depend on the individual clays. For Kaolinite, for example, 600°C to 700°C is sufficient, while montmorillonite and illite require temperatures of above 800°C and 900°C, respectively. Figure 1 shows the calcination process for the three types of clays. Equation I illustrates the decomposition reaction. Figure 2 shows metakaolin in the amorphous phase after calcinations [1].
THE REACTION PROCESS
The clays, following optimal calcination, are able to react as a pozzolan in presence of calcium hydroxide in cementitious systems to form additional strength-building C-S-H or C-A-S-H phases. Equations II (a, b, and c) illustrates these reactions:In terms of the reaction process, Figure 3 shows the 4-phases of reaction (example given for reaction of Metakaolin) viz., a. Introduction of metakaolin into the matrix; b. Dissolution of reactive calcined clay; c. Beginning of the hydration; d. Complete incorporation of the calcined clay into foil-like C-S-H, C-A-H (calcium aluminate-hydrate), C-A-S-H (calcium aluminosilicate-hydrate) and AFm (monosulphate hydrate) phases [2].
Fig. 3: Four phases of reaction of calcined clays
In terms of morphology, the primary difference between C-S-H formation in ordinary Portland cement and calcined clays is the formation of a more stable, foil like structure in case of calcined clays as opposed to the fibrous structure in case of OPC hydration [3]. Figure 4 shows the difference between C- S-H phases in OPC hydration and C-A-S-H phases in the Metakaolin hydration.
Fig. 4: Fibrous C-S-H phases of OPC hydration and foil-like C-A-S-H phases of metakaolin hydration
AS2 + 6CH + 9H
|
C4AH13 + 2C-S-H..........................................................(IIa)
|
AS2 + 5CH + 3H
|
C3AH6 + 2C-S-H.............................................................(IIb)
|
AS2 + 3CH + 6H
|
C2ASH8 + C-S-H............................................................(IIc)
|
Finally, in terms of reactivity, calcined clays such as metakaolin are much higher in pozzolanic activity as compared to flyash, slag and microsilica. This was ascertained by means of the “Chapelle Test” by Asbridge et al [3, 4]. Our results as per the test are given in Figure 5.
USE OF CALCINED CLAYS AS CONCRETE ADDITIVE
MECHANICAL PROPERTIES
Calcined clays when used as additives in HPCs and UHPCs, function on the basis of the micro-filler effect and its pozzolanic reactivity. Due to this combined mechanism, there is an increase in overall mechanical properties of the concrete and improvement in the denser material structure of the matrix, and
in particular, improvement in the Interfacial Transition Zone (ITZ) between the non-reactive aggregates
and the cement matrix. Figure 6 shows this improvement.
In our laboratory tests, the mechanical properties of UHPC based on metakaolin was evaluated and compared to UHPC based on microsilica. The compressive and flexural strengths of the two mixes were measured. It was seen that, although the compressive strength of the two UHPCs were comparable, there was a marked difference in the flexural strengths of the two concretes. Subsequent SEM studies showed that the substantially higher flexural strengths were due to the platy morphology of the unreacted metakaolin. Figure 7 shows comparison of the compressive and flexural strengths of the two UHPCs [5].
Fig. 5: Lime consumption by different pozzolans measured using Chapelle test
Fig. 6: Comparative SEM images showing improvement in the ITZ for normal OPC and an OPC-metakaolin blend
Fig. 7: Comparison of compressive and flexural strengths in UHPCs with microsilica and metakaolin
Durability
Calcined clays like metakaolin, when added to concrete as an additive or as replacement for cement, add to the durability of the concrete. The chemical resistance of concrete is improved due to the denser matrix and ITZ improvement of the calcined clays and reduction of free lime (Portlandite) in the cementitious matrix. Increased resistant to Alkali Silica Reaction is achieved through reaction of the aluminosilicate with alkalis to form stable compounds. These same actions also account for better resistance to chloride penetration through concrete. Lastly, addition of calcined clays also improved the sulphate resistance of tested mixes. This reaction is based on the highly densified matrix structure, the dense ITZ and conversion reactions of the ettringite (ATf) phases in the cementitious matrix to more stable AFm (monosulphatehydrate) phases. Figure 8 shows the results of testing in a cement sand mortar prism, wherein the levels of substitution of metakaolin in the cement binder were varied (0%, 10%, 20% and 30%) and the prisms stored in a sodium hydroxide solution for a fixed amount of time. The visual results of the 4 prisms are shown in Figure 8. It is seen that with higher levels of cement substitution, a better resistance to ASR deterioration is seen [7].
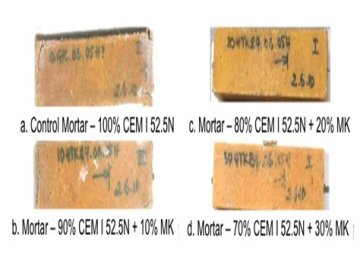 |
Fig. 8: Resistance of mortars with varying % of metakaolin when exposed to alkali. Source: Dr.Huettl, TU-Berlin, Germany
Due to the improvement in mechanical properties and durability that using calcined clays as concrete additives, the material opens up new avenues for production of various new forms of UHPCs. These new materials improve the properties that are crucial for the durability of high-performance concrete. In addition to reducing chloride migration, an exceptional chemical and resistance to aggressive media of the concrete can be achieved. The concrete matrix structure is simultaneously reinforced right down to nanoscale, density is improved and compressive and flexural strength as well as abrasion resistance of the high-performance concrete is increased. There is also a significant reduction of micro-crack formation, which makes it particularly suitable for the production of tunnelling concrete [6]. Successful examples of UHPCs incorporating metakaolin include acid resistant concrete for Budapest Central Wastewater Treatment Facility and acid resistant concrete for production of sewage pipes for Epiton GmbH and Co. KG [8].
USE OF CALCINED CLAYS AS COMPOSITE MATERIAL IN CEMENT
In light of the current sustainability and CO2 emission norms across the world, many research groups are trying to ascertain to what extent are calcined clays suitable as an additional principal constituent in the production of high performance composite cements. The normative framework for this exists. According to EN 197-1, these clays are to be allocated to the group of naturally tempered pozzolans. Beyond that, clays, due to their broad raw material base, are available worldwide and are not subject to seasonal or cyclical fluctuations, which is a prerequisite for any principal constituent in cements.
Metakaolins used as cement composite material until now were prohibitive due to their cost. For this reason, other clays were resorted to, which are partly contaminated and may contain other principal minerals of clay, such as illite or montmorillonite.
In terms of reactivity of the optimally calcined clays, the potential performances of the three types of clay are excellent. However laboratory tests indicate that the performance in clays increases from illite to monmorillonite to kaolinite. This was demonstrated by substituting 30% of OPC with the calcined forms of the three clays above. Observations from the tests show that 2-day compressive strength for the composite cements is lower, but 28- and 90-days compressive strengths are comparable. Of the three types of calcined clays, kaolinite shows the best performance. Figure 9 shows comparative compressive strength development of composite cements based on the different types of calcined clay.
Fig. 9: Comparative compressive strength development for composite cements based on different calcined clays
In conclusion, suitable clays can be activated by suitable thermal treatment or calcination. The reactivity
(strength contribution) of the clays in composite cements depends on a number of factors such as:
- Type and amount of clay minerals and minor constituents
- Calcination / firing conditions
- Particle size of clinker
- Firing temperature
- Holding time
- Overall fineness / particle size distribution
- Alkali content of the cement
- Sulfate content of the cement
- Workability time required (normal cements or fast-setting cements)
These parameters can be varied during cement production to achieve different properties in the composite cement. The extent of variations needs to be further studied in developing these composite cements for commercial use.
CONCLUSIONS
Calcined clays have been used in cementitious systems for over 3000 years. Newer calcination techniques and production methods in addition to focus on sustainability and environment is putting the spotlight back onto use of calcined clays in construction. In addition, inconsistent availability and quality of other pozzolanic material, makes a case for use of calcined clays such as metakaolin as a concrete additive and as a principal constituent in Portland composite cements.
The SEM studies and testing of mechanical properties of mixes incorporating metakaolin in concrete and mortars shows that it offers significant improvement in mechanical properties (especially flexural strength) and also in durability aspects of concrete (namely resistance to chemicals, acids, ASR and sulphates). Imparting these properties, opens up a wide variety of applications where, calcined clays can be used as additives to concrete. Some examples include tunneling concrete, acid resistant concretes for sewage treatment plants and sewage pipes, architectural concrete facades, etc.
In addition, the use of the calcined clays as principal constituent in Portland composite (Portland Pozzolana) cements would be good from sustainability as well as quality point of view. This is because the clays are available worldwide and their supply is not subject to seasonal, industrial or cyclic fluctuations. With the improvement in mechanical properties it provides in composite cement systems, the production methodologies can be further studied and refined to incorporate large-scale use of calcined clays in cements.
REFERENCES
- Ing. Horst-Michael Ludwig, M.Sc. André Trümer, (2013), Calcined Clays in Modern Construction Chemicals – Fundamentals and Application Potential, BFT International 02-2013, pp 13-14.
- Ing. Horst-Michael Ludwig, M.Sc. André Trümer, Bauhaus Universitaet, Weimar.
- Jayant D. Bapat, (2013), Mineral Admixtures in Cement and Concrete, Chapters 5 and 6.
- Asbridge, A.H., Walters, G.V., Jones, T.R., (1994), Ternary blended Concretes – OPC / GGBFS / Metakaolin, Concrete across Borders International Conference, Odense, Denmark.
- Eugen Kleen, (2010), Technical Director, MC-Bauchemie Mueller GmbH and Co. KG, Germany, Laboratory Testing.
- Technical data sheets and in-house testing of Centrilit NC, MC-Bauchemie Mueller GmbH and Co. KG, Germany.
- Test Data from Dr. Huettl, TU-Berlin, Germany.
- Technical Project References for Centrilit NC, MC-Bauchemie Mueller GmbH and Co. KG, Germany.