P G Setty Construction Technology Pvt Ltd
Monolithic Construction Technology
25 million houses shortage in India on an average as per National Building Organization, NBO & NHHP 2007. It is estimated that this figure would go up by another 7 million by 2012 and thus bringing up the total shortage to approximately 32 million. Most of the shortage (99%) is for the lower income group (LIG) and economically weaker section (EWS) as per NBO and NHHP. Housing shortage in urban areas is increasing and demand for new housing is growing at a higher pace in urban areas and supply is not adequate.
The conventional technology cannot cater to the total need for the housing backlog and hence there is a need for an improved system, which will be faster, cost effective and environmental friendly. Housing standards and construction methods not being static, they are constantly evolving to reflect diverse and changing economic conditions, social values, traditions, and technological advances.
One such advanced technology that has emerged in recent times is the Cast-in-Situ Monolithic Reinforced Concrete Construction System. This provides an integrated solution to the problem of large-scale residential housing development. It is widely recognized as one of the most practical, economically and technically feasible solutions to the prevailing problem of building a cost-effective, descent, durable and earthquake-proof housing on a mass scale, quickly and efficiently. |
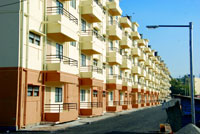 |
Built Expressions Bureau, in an interview with Somashaekar, Managing Director, PG Setty Construction Technology Private Limited, pioneers in the field of monolithic construction methodology using aluminium formwork, to understand more about this innovative technology and its implementation on large scale. Excerpts from an interview:
“our aim has always been to build, develop and maintain a good living environment for people. Today we are successfully catering to the Government’s requirement to build houses for urban poor, with “Fast Track Construction Techniques”. He further adds “We were constantly exploring all possibilities to improve speed of construction to cater to the present and future housing requirement for the urban poor in India. Our search for the right technology for mass house construction leads us to -Monolithic concrete construction with Aluminum formwork system”- says Somashekar.
Services offered by PG Setty
About the services offered by PG Setty in Mass housing, Ramaprasad, COO explains their three pronged offer.
Design Build and Transfer: We provide solution from conception, designing, planning to execution and handover of the project.
Design consultancy: For efficient use of technology, it is important that the structure itself is designed to be compatible with the technology. We provide complete design solution for our client, which includes architectural, structural, services and formwork system design.
|
 |
Formwork consultancy: If the architectural and structural designs are ready and the client wishes to adopt this technology, we help them achieve their goal in using the technology to its maximum potential. Our scope includes designing the formwork system, vendor contract management, formwork procurement management and training of workmen to achieve 2 days cycle time. Our efforts have always been to modify the technology and the method of working to be as per IS codes.
Monolithic Structure
The Cast-in-Situ Monolithic Reinforced Concrete Construction System uses a formwork system that allows the contractor to cast foundations, walls, and ceilings according to a pre-defined cycle. It combines the speed; quality and accuracy with the flexibility and economy of in-situ construction. The result is a reinforced concrete structure, the surfaces of which are of sufficiently high quality to require only minimal finishing for direct decoration.
According to Ramaprasad, COO, PG Setty, “ monolithic structure is a structure in which all the components of a building, like walls, slabs, staircases, sunshades etc are cast together with a homogenous material called- Concrete”.
System Philosophy
When asked about the philosophy behind the technology they have so successfully adopted and its relevance in Indian context, Somashekar, MD, explains at length the entire concept:
“With fast urbanization of the developing countries, the housing of economically backward masses has become a raging problem throughout the world.
According to the estimates made by the Ministry of Housing & urban Poverty Alleviation, Government of India, for the 12th five year plan (2012 – 17) the total housing shortage in the country will be about 30 million which is increasing every day.
Today only about 10 % of this demand has been addressed. The need to meet the huge demand over a short span of time calls for Fast Track construction techniques. Our main concern while selecting the right technology for mass housing was to identify a fool proof system which resembles an industrial assembly line production process. While our aim was to speed up the construction process, it was also our priority to deliver excellent quality living for the society. Our search ended with - ‘Monolithic construction using Aluminium Formwork system’. A Monolithic structure is one in which all the components of a building, like walls, slabs, staircases, sunshades etc. are cast together with a homogenous material –Concrete.
Some of the facts which bolstered our stand in adopting this technology were:
- The cycle time for one floor is drastically reduced since the all the components of the building are cast in one shot.
- These structures offer unmatched strength against natural disasters due to its single solid block nature as compared against a conventional building (column, beams & Slab)
- Number of activities as compared to conventional construction is very less.
- The most time and resource consuming activities i.e. Brickwork and plastering is completely avoided. The surface of concrete thus obtained is smooth enough to directly receive paint.
- All the service cutouts like electrical, plumbing and sanitary are embedded before casting.
- The Aluminum formwork is a self-aligning and leveling system which ensures correct dimensional stability of the structure. By virtue of this property, the dependability on the skilled carpenters is considerably reduced. Hence the scope for human errors is minimized. Also the panels require no heavy equipment for handling due to their light weight.
We believe this technology has the potential to meet the present and expected supply rate for this humungous demand.”
Essentials of Monolithic Construction
There are two important factors. Well designed ready mix concrete to ensure desired strength for early deshuttering and a well designed formwork system to allow speedy handling. While a well designed ready mix concrete is achievable, the real challenge is to decide on a formwork systems available. The forms are lighter than most other formwork systems.
The wall forms can be removed within merely five to eight hours. Each set of forms can be used up to two hundred times, provided it is properly maintained and serviced. This cycle can be repeated following a thorough overhaul of the formwork components. These forms are of high strength and flexural rigidity fewer nuts and bolts are used to join the constituent parts of the formwork system.
Advantages
Advantages of monolithic construction with Aluminium Formwork system can be listed as under.
- Fast track construction.
- Excellent surface finish.
- Better Dimensional stability.
- Avoids time consuming brickwork and plastering.
- Because of reduced dead load, superstructure and foundation cost are minimized without compromising on strength.
- Unparalleled strength against earth-quakes.
- Better water resistant surface.
- Helps in precise scheduling and assured quality control.
- Less Manpower.
- The repetitive, predictable nature of the tasks involved encourages familiarity with operations and, once training is complete, as construction progresses, a zero accident objective becomes more and more achievable. The minimum requirement for tools and equipment when moving the forms further reduces the risk of accidents on site.
- The entire structure, including the foundation, the walls and the ceilings functions as an integrated whole.
- All service runs can be pre-installed before the concrete is poured. Other facilities such as bathroom fixtures can be installed quickly as work progresses on other floors.
- Monolithic System of Formwork is extremely user-friendly. The system creates a rhythm for the worker. By taking advantage of the 48-hour cycle, the same steps in construction are repeated over and over again. The result is a workforce that can work effectively together as a highly productive team.
- The technology and the formwork system together create an efficient load-bearing structure for use in a variety of applications. It is particularly effective in projects suited to repetitive construction, especially large-scale mass-housing projects. The solid, strong monolithic structure can be 2-20 stories in height.
- Shorter site preparation and establishment.
- Easily adaptable to diverse topographical and climatic conditions.
- The walls, 10-20 cm. thick, are joined to the foundation and the ceiling slabs by means of dowel bars. The high levels of dimensional accuracy achieved with the continuous formwork system and the superior load distribution result in a strong, solid monolithic structure suitable for a multitude of uses. The system's excellent structural integrity provides opportunities to use non-load bearing internal partitions that can be moved to provide alternative layouts.
Construction Sequence
Pre construction planning - Every project has its own duration and budget. To ensure the successful performance of the technology without compromising on project requirements, a detailed initial planning needs to be done.
-
The designs for the project should be developed in coordination with an architect, formwork consultant, structural and service consultants keeping the technology being used in the mind. Once the designs are finalized, there shall be no scope for changes during execution.
- Firstly, a concrete pour diagram (a schedule showing the sequence of the concrete pours as per the target cycle time) has to be planned to meet project timelines. Based on this the area of formwork to be purchased is arrived at.
- Secondly, the formwork manufacturer has to be given inputs for designing the system to suit our concrete pour plan.
- Lastly, the concrete mix should be designed to develop enough strength to allow early de-shuttering as per our concrete pour plan.
|
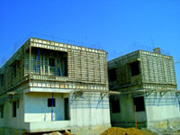
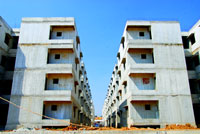
|
Construction
Foundation-We have developed a typical foundation system for mass housing to match the speed of construction of the superstructure. It consists of a strip footing for peripheral walls with a raft on top, on which the superstructure rests. We have achieved an average cycle time of 4 days for foundation.
Superstructure- Sequence of construction will be as follows
- Day 1 – Reinforcement for wall is laid in position and tied. All the service embedments like electrical conduits, junction boxes; plumbing and sanitary cutouts are placed in position and fixed on to the reinforcement. Later the formwork for wall and slab is completely fixed.
- Day 2 – Slab reinforcement and service embedments are fixed in position. The entire floor including walls, slab, sunshades, parapet walls etc are concreted together in one shot.
- After 12 hours from concreting, the wall panels are deshuttered and shifted for erection in the next pour. At the end of 36 hours the slab panels are de shuttered leaving an undisturbed central support in place.
- Once the entire floor is de shuttered, the staircase and the lift core will be cast which also follow a 2 day cycle will parallel to the floor.
Precast vs Monolithic
Table 1 shows the comparison between monolithic and precast construction.
Description
|
Monolithic Construction
|
Precast
|
Initial investment on technology
|
Moderate
|
Very High
|
Surface finish
|
Very good compared to conventional construction
|
Excellent due to controlled quality measures
|
Strength
|
Good
|
Good
|
Skill of Manpower
|
Skilled
|
Highly skilled
|
Manpower requirement
|
Moderate
|
Low
|
Equipment
|
None
|
Requires equipment
|
Minimum no of units to adopt the technology
|
500
|
1500
|
Access roads
|
NA
|
Requires good access roads (to and within the project) for transportation and erection
|
Security
|
Formwork materials are more prone to theft
|
More secured since it is a fixed setup
|
Adaptability for design changes
|
Cost money and time
|
Comparatively cheaper
|
The relevance of one of these technologies depends on the project requirement. For instance, consider a project with 500 units at a remote location. Considering Indian scenario, the condition of access roads to such locations poses a huge risk for transportation of precast elements. Even if one decides to set up a dedicated precast factory next to the project location itself, the return on investment of the technology in this project would be very low compared to monolithic construction with aluminium |
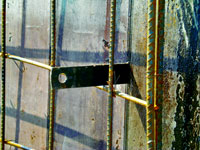 |
formwork. On the other hand if the units are distributed to different locations which have access roads but do not have Ready mix concrete plants in the vicinity, the most viable option will be to adopt precast technology.
Signature projects and Challenges
Expounding the challenges while executing some of their signature projects, Somashekar, MD recalled, “Construction of 1000 houses for Karnataka Slum Clearance Board at Mysore was our signature project. This project being our first venture with this technology was a huge challenge for us. The major hurdle was to break the mental block of the Government officials on using this technology. The concept of de shuttering the formwork so early was still new to everyone. The formwork of wall could be stripped off in 12 hours & the slab formwork after 72 hours leaving the mid supports in place, which is as per provisions in the code of practice. The code also says that the formwork could be stripped off when the structure gains 70% design strength. The concrete mix was designed to suit this criterion. The company established by theoretical computations, code provisions & the laboratory tests that 12 hours’ de-shuttering for the walls & 36 hours’ de-shuttering of slab under strict quality control mechanism can be achieved. Since this was never practiced in the country, the technical committee did not provide concurrence for a 2day cycle. However, because of the fact that the technology was new to us, achieving a 3 day cycle was still a challenge. With proper planning of formwork movement and specially designed concrete mix we were able to achieve a 3 day cycle on site which we once proved on paper. This project won us many accolades for introducing an innovative technology to deliver quality housing for the most underprivileged group of citizens. Ministry of housing and urban poverty alleviation bestowed on us the best project award under fast track and cost effective mass housing.”
He further added “The recognition of our efforts from Central Government and the quality of product delivered helped us to obtain permission for a 2 day cycle in our next project for Bangalore Development Authority. By now we had understood the shortfalls of the technology and knew how to overcome them. We suggested some important changes in the formwork system for the manufacturer which facilitated 2 day cycle. Today we are successfully delivering the concrete shell of each floor in just two 2 days. We believe that there is always scope for improvement. Our team is continuously striving to device ways in which the cycle time could be further reduced.”
On-Site: Step by Step
- The foundation, the wall, and ceiling formwork systems are designed in strict compliance with the architectural plan in accordance with the design specifications in the fabrication plant.
- The construction site is leveled and compacted according to the project's technical requirements.
- A layer of lean concrete is placed before the foundation.
- Piping systems like Sewerage pipes etc are laid.
- Reinforcement bars of the foundation are installed after the lean concrete gains sufficient strength.
- The foundation forms are installed and poured.
- The wall reinforcement are put in place and connected to the starter bars of the foundation.
- The window and door frames or templates, electrical conduits and sockets, water pipes and sewer ducts are all built into the forms, thereby eliminating the need for drilling, boring and excavation work.
|
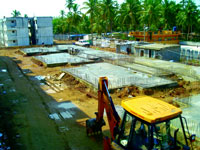
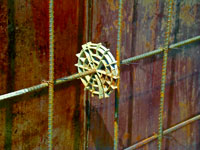
|
- The wall forms are then installed and poured monolithically.
- After removing the wall forms, first the ceiling reinforcement mesh and then the ceiling forms are installed.
- The ceiling reinforcement bars are joined to the wall by means of starter bars. At this stage, junction boxes, electrical conduits and water pipe ducts which pass through the ceiling are built into the forms.
- The ceiling forms are poured monolithically.
- Then the ground floor ceiling is prepared for the installation of the walls of the first floor.
- This cycle is repeated in the same manner for other floors.Somashekar, in his concluding remark says, “There is a tremendous scope for further improvement in terms of quality, speed and adaptability. The demand and supply chain of Mass Housing in India can be successfully addressed only if we use the right kind of technology and the right kind of formwork system keeping the sustainable development in mind. Monolithic Construction is the solution”
Conclusion
ABOUT PG SETTY
In 1964 Sri P Gopalasetty, Chairman laid the foundation for PG SETTY – construction firm as a family business in Kushalnagar, Coorg District, Karnataka. He has served the construction industry in State & Central Government and private sector. Major projects of his time included rehabilitation works for Tibetan resettlement, irrigation structures and other infrastructure projects in Coorg, Mysore and Hassan Districts. In the mid 80's the construction firm was reconstituted with his sons M. G Somashekar, Managing Director and M.G Gangadhar, Director.
Later in 2000's PG SETTY was Registered as a company (PG Setty Construction Technologies Pvt. Ltd.) a step towards moving away from family owned business to a professionally managed company. Corporate office moved to Mysore with Kushalnagar as the regional office and team of over 75.
Vision: Offer consistently high quality, best value-for-money service to our esteemed customers through an innovative approach to construction of building, backed by sound planning, and state of the art construction techniques.
Major projects by PG Setty
- The Golden Temple, Bylakuppe, Coorg District
- CLT Monastry at 2nd camp Bylakuppe, Coorg Dist
- Zong Dok Palri Monastry at Bylakuppe, Kushalnagar, Coorg Dist.
- Banneraghatta Butterfly Park at Bangalore.
- Indoor Sports Stadium for National Institute of Engineering at Mysore.
- 1000 houses for slum dwellers at Sathagalli, Mysore
Awards and Accolades
- Mass housing project at Mysore for Slum Dwellers in 2010 received the Prime Minister’s Award for implementation of best cost effective housing technology in India.
- Vishwakarma Award (2012) from Construction Industry Development council (CIDC) for best project under Design, Build, Transfer (DBT) format
- Builder of the year award (twice 2001 and 2011) by Builder’s Association of India (BAI)
- Birla Endowment Special Jury Award for outstanding Concrete Structure from Indian Concrete Institute – 2011
Mr. Somashekar, Managing Director
Mr. Somashekar is a Civil Engineer with over 30 years of service in the field of Construction. He graduated from the National Institute of Engineering, Mysore in 1985 and immediately joined his father in construction business.
He is a technology enthusiast whose dream has always been to mechanize the construction processes and make it less labor intensive. Today he is known for his expertise in efficient use of technology in the mass housing sector.
His ardent interest in emerging technologies and quality of work delivered has bagged him several challenging projects and won |
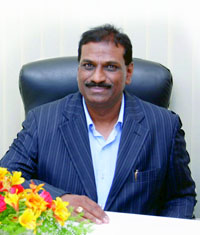 |
him several accolades which has enabled him to take P G Setty to new frontiers.